Techniques and Advances in Optical Fiber Manufacturing
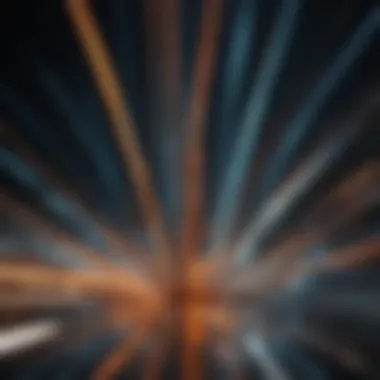
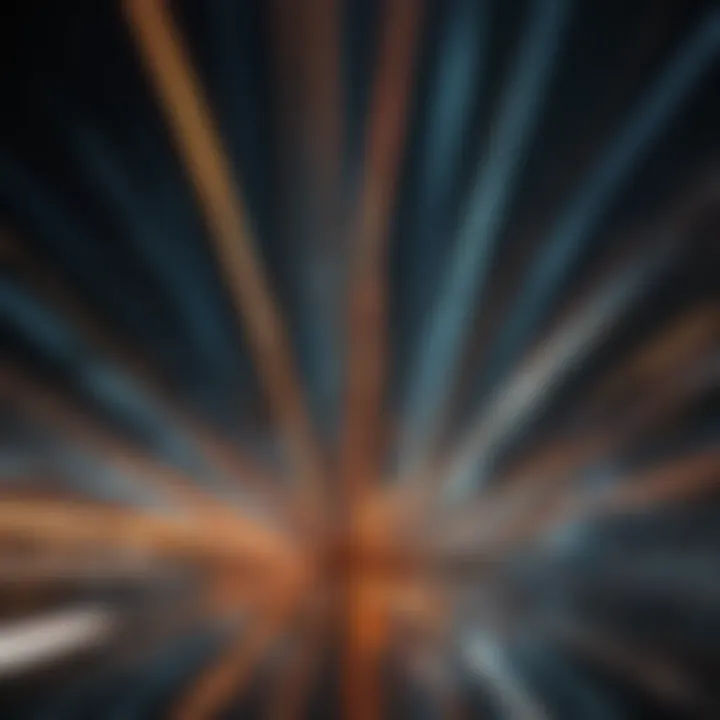
Intro
The world of optical fiber manufacturing is intricate and technically demanding, offering a wealth of challenges and opportunities. Optical fibers are not merely strands of glass or plastic; they are vital components of modern communications, enabling rapid data transfer over long distances. With increasing demands for bandwidth and speed in our interconnected societies, understanding the techniques and advancements in optical fiber production has never been more critical.
Within this realm, various techniques shape the final product. From the raw materials selected to the process of fiber drawing, every step impacts the performance and efficiency of optical fibers. This article aims to take a closer look at the critical pathways involved in manufacturing optical fibers, diving deep into both historic and cutting-edge technologies.
Moreover, as the landscape of fiber optics continues to evolve, new methodologies are being explored, pushing the boundaries of what’s possible. This exploration is essential not only for existing manufacturers but also for students and professionals keen on understanding this dynamic field. Whether you're trying to solve complex communication problems or simply looking to broaden your knowledge, the insights offered will be relevant to individuals at every level of expertise.
Intro to Optical Fiber
Optical fiber is at the heart of today’s telecommunication data highway. Its capacity to transmit large quantities of information at the speed of light has revolutionized the way we communicate. This section will explore the definition of optical fiber, its significance in modern technology, and its historical evolution, providing a foundation for understanding the manufacturing processes that follow.
Definition and Importance
Optical fiber is essentially a flexible, transparent strand of glass or plastic that transmits light signals over long distances. The ability of optical fibers to carry vast amounts of data with minimal loss has challenged traditional methods of communication, such as copper wires. This advancement has paved the way for high-speed internet, telephony, and video streaming.
Moreover, optical fibers are pivotal in various other applications, including medical equipment like endoscopes, industrial sensors, and military communications. The efficiency, low energy consumption, and ability to operate in harsh environments make optical fibers indispensable in a range of sectors.
Historical Evolution
The journey of optical fibers began in the early 19th century when scientists started to investigate the principles of light. A significant milestone was achieved in 1823, when Daniel Colladon and Jacques Babinet showed that light could be transmitted through water. Fast forward to the 20th century, where key advancements came from researchers like Narinder Singh Kapany, who is often called the "father of fiber optics." His work on the transmission of light through optical fibers during the 1950s laid the groundwork for fiber optics technology.
In the 1970s, the introduction of fiber-optic communication systems transformed the telecommunications realm. Researchers focused on creating fibers with minimal attenuation and dispersion, enabling longer distance communications without significant signal degradation. Companies like Corning Glass Works developed high-purity optical fibers, which played a crucial role in this technological leap.
The ongoing evolution of optical fibers now encompasses innovations in materials, design, and manufacturing techniques, making them a key component of modern infrastructure. As we dive deeper into the manufacturing processes of optical fibers, it’s essential to recognize how history has shaped current practices and opened doors to future advancements.
"Optical fiber technology has not just shaped telecommunications—it is shaping how we connect with the world."
Understanding these fundamental aspects of optical fiber sets the stage for our exploration of its manufacturing techniques and the advances that are continually propelling the technology forward.
Raw Materials in Optical Fiber Production
The foundation of optical fiber manufacturing lies heavily on the raw materials involved. Understanding these materials is crucial, as they not only determine the fiber's quality but also impact the overall performance and efficiency of communication systems relying on fiber optics. In this segment, we’ll delve into the primary materials used in optical fiber production, examining the significance of silica and dopants, highlighting their roles, and understanding their characteristics.
Silica as the Primary Material
Chemical Properties of Silica
Silica, or silicon dioxide (SiO₂), is the cornerstone of optical fiber manufacturing. The unique characteristic of silica lies in its exceptional transparency to light, crucial for minimizing attenuation and maintaining signal integrity. A significant property of silica is its high refractive index. This quality enables light to bend effectively as it travels through the fiber, allowing for efficient transmission over long distances.
Moreover, silica displays high levels of purity, which is essential since impurities can lead to scattering and loss of signal quality. The thermal stability of silica, with its ability to withstand high temperatures without melting or deforming, makes it a reliable choice for constructing optical fibers. This is particularly beneficial in environments where excessive heat may be a concern. In essence, the chemical properties of silica lay the groundwork for reliable and efficient optical fiber performance.
Sources of High-Purity Silica
The quest for high-purity silica is critical in optical fiber production. The primary sources include natural quartz and synthetic silica, obtained through various chemical processes. Natural quartz sand, with its crystalline structure, is a commonly used material. This source is favored due to its abundance and relative low cost.
High-purity synthetic silica is produced using methods like the sol-gel process, which allows for finer control over impurities. This control is paramount; even the smallest contamination can lead to significant losses in data transmission. By concentrating on reliable sources of high-purity silica, manufacturers can ensure that the raw material meets the stringent standards required for optical fiber applications. The balance between cost, availability, and purity remains a delicate dance in this aspect of production.
Dopants and Their Functions
Dopants play an important role in refining the characteristics of optical fibers. By introducing specific elements into the silica matrix, manufacturers can fine-tune the fiber's optical properties to enhance performance. These enhancements are vital for creating fibers tailored to specific applications, like telecommunications or sensor technologies.
Common Dopants Used
Among the most common dopants are germanium dioxide (GeO₂) and phosphorus pentoxide (P₂O₅). Germanium is particularly useful for increasing the refractive index of the silica core, allowing for greater light confinement. This characteristic is crucial in the development of low-loss fibers, where signal strength is maximized. On the other hand, phosphorus can enhance the fiber's sensitivity in sensor applications. The subtle interplay of these dopants is essential for building fibers that serve specific technological needs, thereby driving innovation in the field.
Impact on Performance Characteristics
The impact of these dopants extends beyond basic functionality. They significantly influence parameters like attenuation and bandwidth, which are critical for communication applications. For example, fibers doped with germanium exhibit lower attenuation rates, which translates into longer transmission distances without repeaters. Additionally, the refractive index profile can be finely tailored to optimize signal propagation. The introduction of each dopant must be carefully calibrated, as excessive amounts can lead to undesirable effects, such as increased scattering or changes in the fiber’s mechanical properties.
In summary, understanding the raw materials in optical fiber production reveals much about the potential of fiber optics technology. From the choice of silica, characterized by its chemical traits, to the thoughtful inclusion of dopants, each element plays a defining role in the capabilities and efficiencies of optical fibers. Emphasizing the purity and properties of these materials not only aids in fostering better technological solutions but also ensures that the industry progresses in a direction that meets the growing demands for quality and performance.
Fiber Preform Fabrication Techniques
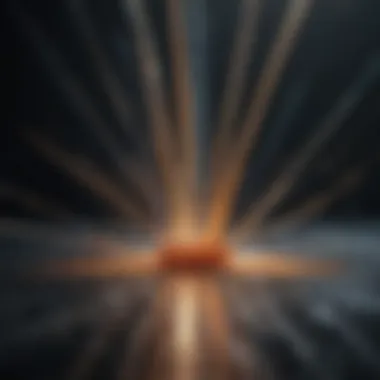
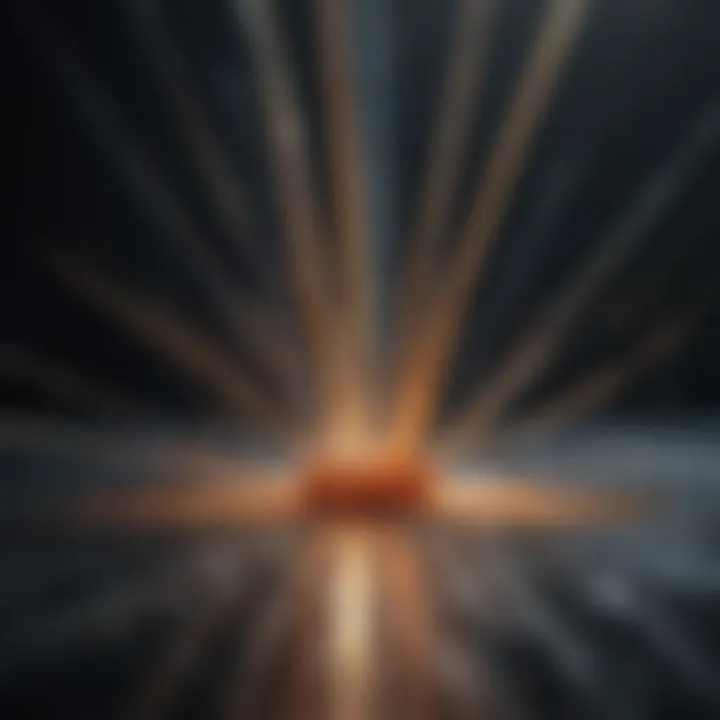
The technique of fabricating preforms is vital for the production of optical fibers, serving as the foundational step before drawing the final fiber. A preform can be thought of as a large optical fiber where the dimensions are scaled up. Its composition and structure directly influence the optical characteristics, performance efficiency, and eventual applications of the completed fiber.
Vapor-Liquid-Solid Growth
This method involves the formation of the fiber's core through a unique process that merges vapor and liquid phases to create solid material. In the Vapor-Liquid-Solid (VLS) technique, a thin catalyst particle initiates the growth, allowing the material to deposit layer by layer. The elegance of this technique cannot be understated; it yields highly pure silica fibers that show exceptional transmission properties. This method is often favored for its ability to produce fibers with minimal defects, critical for achieving high-performance communication networks.
"A flawless preform leads to a stellar fiber, and that’s what keeps the world connected today."
In practical terms, VLS growth is adaptable. It supports a range of dopants, which are essential for tuning the refractive index and other optical properties of the fiber. Through careful management of the temperature and materials used, manufacturers can significantly influence the characteristics of the final product, promising versatility and reliability.
Modified Chemical Vapor Deposition
Modified Chemical Vapor Deposition (MCVD) is another prominent technique in the realm of preform fabrication. It intricately combines gaseous reactions to deposit material onto the inner walls of a rotating silica tube. This approach allows for controlled layering of different materials, which can optimize the optical properties based on specific requirements.
Notably, the gradual build-up of layers in MCVD enables precise control over the refractive index profile, which plays a big role in managing the light propagation characteristics. Applying MCVD also allows adjustments or additions to the composition of the core and cladding materials during the deposition process, giving manufacturers the upper hand when it comes to crafting fibers tailored to specific applications from telecommunications to medical instruments.
External Vapor Deposition
In this technique, external vapor deposition involves the application of material in vapor form under controlled conditions, which accumulates on a substrate. This approach to fabricating preforms stands out due to its simplicity and effectiveness. External Vapor Deposition focuses on the consistent and uniform application of material, resulting in high-quality preforms.
By utilizing this method, manufacturers can achieve a variety of layer compositions, allowing for complex performance characteristics to be embedded within the fiber's structure. This becomes crucial when aiming for innovative designs. Additionally, with advancements in technology, External Vapor Deposition has gained traction for its scalability and cost-effectiveness, making it a prime candidate for mass production of optical fibers.
Through these varied techniques, it's evident that fiber preform fabrication is an intricate dance of science and art, where precision meets creativity to pave the way for next-gen optical fibers.
Fiber Drawing Process
The fiber drawing process plays a pivotal role in the manufacturing of optical fibers. This step transforms the preform into long, thin fibers, ensuring that the final product meets stringent performance and quality standards. That's no small potatoes, as the efficiency and precision of fiber drawing directly influence the optical properties of the fiber and how well it can transmit light.
Fundamentals of Fiber Drawing
In essence, fiber drawing involves pulling the glass preform to reduce its diameter to a fraction of its original size. This is done while simultaneously heating the preform, making the glass malleable. The process is akin to stretching a piece of taffy; with the right temperature and technique, it can be drawn out to form a fine, even fiber.
One of the key components in this initial phase is the use of a draw tower, where the preform is lowered into a heated zone and then drawn vertically downwards. The temperature within this zone is meticulously controlled, ensuring that the glass softens appropriately for consistent drawing. An even draw is crucial; uneven stretching can lead to variations in performance, which can affect signal integrity.
Optimization Techniques
To ensure that the fiber drawing process yields optimal results, manufacturers adopt several optimization techniques. These methods fine-tune the drawing conditions to achieve the desired characteristics of the finished fiber, such as its strength, clarity, and overall optical performance.
Temperature Management
Temperature management is fundamentally important in fiber drawing. A precise temperature needs to be maintained to ensure that the glass is not too brittle or too soft. If the temperature is too high, the fiber may sag or warp; on the flip side, if it's too low, the glass might not flow properly. It's a delicate dance that requires careful calibration.
Key characteristics of effective temperature management include:
- Consistency: Maintaining a uniform temperature throughout the draw is essential. Fluctuations can introduce weaknesses or other defects that can affect overall fiber performance.
- Control Systems: Advanced control systems help operators monitor and adjust the temperature in real-time, ensuring that the process remains steady.
Using optimized temperature management techniques offers several advantages:
- Enhanced Performance: By achieving the ideal draw temperature, manufacturers can produce fibers that meet or exceed industry standards for attenuation and bandwidth.
- Reduced Waste: Proper heat management can minimize material wastage by reducing defective fibers or broken draws.
However, there are also disadvantages; for example, overly complicated systems might require higher initial investments in technology.
Drawing Speed Adjustments
Drawing speed is another significant factor impacting the fiber drawing process. Adjusting the speed at which the fiber is drawn from the preform can alter the fiber’s characteristics. A slower draw speed can lead to a more uniform fiber, but it may not be practical for large-scale production.
Key characteristics of drawing speed adjustments are:
- Precision: Slower speeds can result in finer control over fiber uniformity, which is critical for achieving desired light transmission properties.
- Production Rate: On the contrary, fast drawing speeds promote higher output but can risk inconsistencies in diameter.
Speed adjustments can greatly contribute to the quality of the fiber, offering benefits like:
- Customizable Characteristics: By tweaking drawing speed, manufacturers can fine-tune optical properties and physical strength characteristics of the fiber produced.
- Efficiency in Production: Faster speeds translate directly into higher production volumes, a key factor for meeting commercial demands.
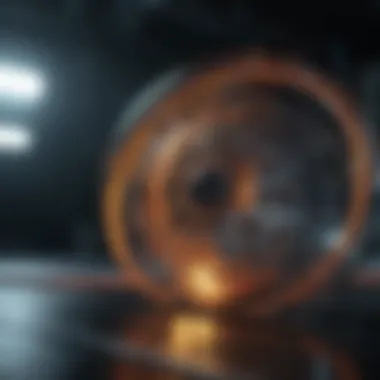
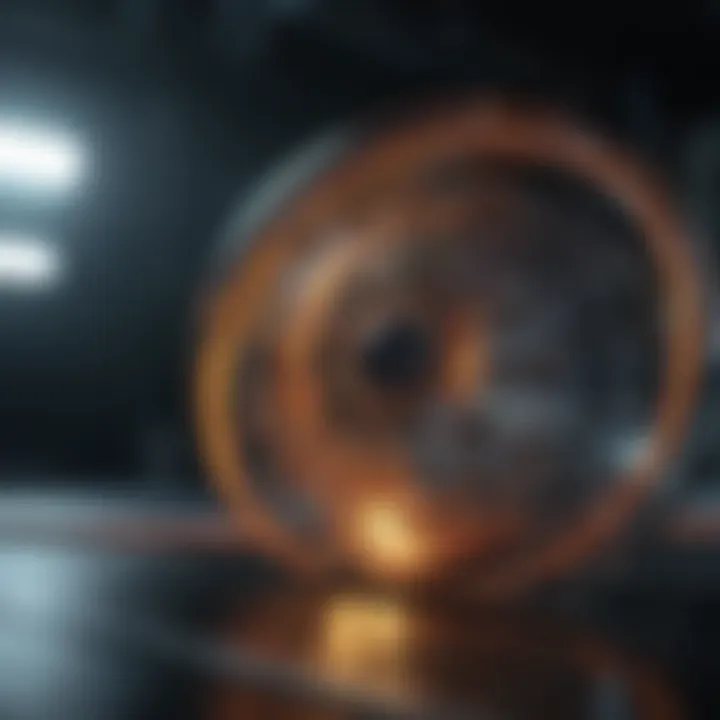
Nonetheless, this advantage comes with its own set of disadvantages. The risk of producing irregular fibers increases with speed, which can lead to further issues down the line.
"The fiber drawing process is not just about producing a product; it's about mastering the balance between precision and efficiency."
In summary, the fiber drawing process is essential for the successful manufacturing of optical fibers. Through careful management of temperature and drawing speed, manufacturers are able to produce fibers that not only meet but often exceed the stringent requirements of modern communication systems.
Coating and Buffering
Coating and buffering in optical fiber manufacturing are crucial elements that enhance fiber performance and longevity. These processes serve not only to protect the delicate glass core but also to optimize the fiber's operational capabilities. A deeper look at the particulars reveals the considerable impact these techniques have on the overall functionality of the fibers, ensuring they can withstand various forms of stress encountered during installation and throughout their lifecycle.
Purpose of Coating
The primary purpose of coating is to insulate the optical fiber from environmental factors and mechanical stresses. Without proper coating, fibers would be quite vulnerable; external threats like moisture, dust, and physical abrasions could lead to performance degradation. Additionally, the coating allows for flexible handling during installation, minimizing the risk of breakage. Another important aspect is that the coating helps maintain signal integrity within the fiber by reducing attenuation losses. This ensures that data transmission remains swift and reliable.
Types of Coating Materials
The choice of coating materials is vital and varies depending on the intended application of the optical fiber. Some common types of coating materials include:
- Polyurethane: Known for its exceptional durability and high mechanical strength, making it ideal for outdoor applications.
- Acrylic: This is often utilized in indoor fibers, offering a balance between flexibility and protection from harsh environments.
- Silicone: Typically used in specialized components due to its high resistance to temperature fluctuations.
Each material brings unique properties, contributing to factors like thermal stability and abrasion resistance, which are essential for durability and reliability in various environments.
Application Methods
The method by which the coating is applied significantly affects the quality and functionality of the optical fiber. Several techniques can be employed:
- Dip Coating: In this method, the fiber is submerged in a coating solution, allowing an even layer to form as it is withdrawn.
- Extrusion: This involves forcing melted coating material through a die, wrapping it around the fiber as it is drawn.
- Spray Coating: A more modern method where a fine spray of coating material is applied to the fiber surface, suitable for specific applications requiring precision.
"A well-executed coating process can extend the lifespan of optical fibers significantly, enhancing their performance in challenging conditions."
Choosing the right coating method is essential for ensuring that the process is efficient and results in a high-quality product. Each technique has its advantages and will be selected based on the specific requirements of the fiber and its intended use.
Overall, coating and buffering are fundamental components of optical fiber manufacturing that impact not just the performance, but also the durability and effectiveness of fiber optic systems in diverse applications.
Quality Control Measures
Quality control is a fundamental aspect in the manufacturing of optical fibers. It ensures that the fibers produced meet the required standards for performance, reliability, and safety. In an industry that is constantly evolving and pushing technological boundaries, maintaining rigorous quality checks is critical. Each stage of optical fiber production, from raw material selection to the final product, requires detailed scrutiny.
The importance of quality control measures can’t be overstated. It not only guarantees the end product's consistency but also bolsters consumer trust and market competitiveness. The implications of overlooking quality could result in subpar products that fail to function optimally in their intended applications, like telecommunications or medical devices. Therefore, effective quality management can significantly minimize the risks, ensuring a robust final product that can handle extreme conditions and deliver optimal performance.
Standards and Certifications
In the realm of optical fiber manufacturing, adherence to standards and certifications is non-negotiable. Various national and international organizations set forth guidelines that define acceptable quality levels for optical fibers. For instance, standards from the International Organization for Standardization (ISO) and the Institute of Electrical and Electronics Engineers (IEEE) stipulate precise requirements that manufacturers must meet. These standards also help streamline processes, making quality assessments more reliable across different manufacturers.
Testing Procedures
Testing procedures form the backbone of quality assurance in optical fiber production. These methods allow for the extensive evaluation of the fibers at various stages of their lifecycle. Two primary testing procedures include attenuation tests and refractive index profiling. Let’s delve deeper into each one.
Attenuation Tests
Attenuation tests measure the loss of signal strength as light travels through the fiber. This is a crucial aspect because higher attenuation leads to less efficient communication. The key characteristic of attenuation tests is that they quantitatively assess the fiber’s performance over distance, making them widely recognized in the optical fiber industry.
One unique feature of attenuation tests is their ability to identify specific loss points within the fiber, which can help manufacturers quickly diagnose and resolve issues in production. While beneficial in providing timely insights, it's worth noting that these tests require precise setup and calibrated equipment, or the results could be misleading.
Refractive Index Profiling
Refractive index profiling is another pivotal testing method. It evaluates the refractive index of the fiber, which is essential in determining how light propagates through it. The main advantage of this method lies in its ability to create a detailed profile of the refractive index across the fiber's cross-section, illuminating any potential anomalies that could affect performance.
This technique is favored for its precision and the level of detail it offers. However, it might require advanced equipment and trained personnel for accurate execution, which could impose additional costs on manufacturers.
"Quality control is not just a process—it's a promise to the end user that the product they are receiving is reliable and effective."
Understanding these processes and their significance in the optical fiber manufacturing landscape is critical for any professional involved in the field. By focusing on quality control measures, manufacturers can not only meet but exceed consumer expectations, paving the way for future advances in fiber optics technology.
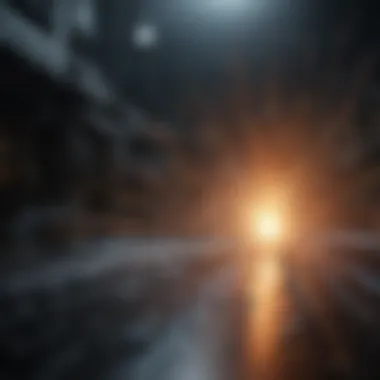

Challenges in Optical Fiber Manufacturing
The optical fiber manufacturing process, while sophisticated and crucial to modern communication, encounters various challenges that can hinder efficiency and production quality. Understanding these challenges is essential for anyone involved in the field, from students to seasoned professionals. These hurdles reflect not just the technical aspects but also the broader market landscape affecting production processes.
Material Limitations
One of the most significant challenges faced in optical fiber production lies in the availability and quality of raw materials. The principal material used is silica, which must be of high purity to ensure effective signal transmission. However, sourcing high-purity silica can be quite difficult. Various impurities can degrade optical performance. For instance, even minute amounts of aluminum or iron can significantly alter the refractive index, leading to undesirable signal loss.
Moreover, the processes of doping, which involve introducing specific elements to modify the fiber's properties, also present complications. For example, while germanium is a common dopant for increasing refractive indices, its extraction and processing can be costly and environmentally damaging. Hence, manufacturers often find themselves navigating a fine line between optimizing material properties and minimizing costs.
"Material purity is the name of the game. A slight misstep can mean a loss not just in quality, but also in reputation."
Environmental Constraints
The environmental considerations involved in optical fiber manufacturing can't be overlooked. As the industry evolves, there's a growing emphasis on sustainable manufacturing practices. Traditional methods for producing fiber optics often result in significant waste and environmental pollution.
For instance, chemical vapor deposition techniques, while effective, can emit harmful by-products. Manufacturers are increasingly pressured to adopt cleaner practices, not only due to regulatory requirements but also as a response to consumer demand for sustainable products. This shift can require substantial investment in new technologies, which might not yield immediate returns. Thus, while the commitment to sustainability is essential for operational compliance, the financial implications can present a serious constraint for manufacturers, especially smaller companies.
Market Competition
The landscape of optical fiber manufacturing is fiercely competitive. With advances in technology, new players continue to emerge, often disrupting traditional market dynamics. This competition isn't just about product quality; it's also deeply rooted in cost-efficiency and innovation.
Established companies face the peril of being outpaced by newer entities that may offer innovative approaches or more cost-effective solutions. The rush to innovate can lead to oversights in quality or accountability, as firms scramble to gain a competitive edge. Thus, balancing innovation with rigorous quality control becomes another significant challenge.
Furthermore, when considering global markets, manufacturers must navigate varying regulatory frameworks, leading to added complexity in adherence to standards across different regions. This dynamic makes for a complicated environment where success hinges on adaptability, foresight, and strategic planning.
In summary, the challenges in optical fiber manufacturing—material limitations, environmental constraints, and rigorous market competition—highlight the intricate balancing act required to thrive in this field. Understanding these aspects is essential not only for manufacturing efficacy but also for gaining insight into the broader industrial landscape.
Future Trends in Optical Fiber Production
The field of optical fiber production is continuously evolving, and keeping an eye on future trends is key to understanding where the industry is heading. Evolving technologies and methodologies not only promise to enhance the performance of optical fibers, but also aim to meet the growing demand for high-speed communication, robust infrastructure, and, importantly, sustainability. In this section, we will explore the major facets impacting the future landscape of optical fiber production, including innovations in materials, automation in manufacturing processes, and sustainability initiatives.
Innovation in Materials
Materials play a pivotal role in determining the efficiency and capabilities of optical fibers. Innovations in this area are not merely for show. They're essential to push the boundaries of what’s possible. Researchers are looking beyond standard silica fibers to develop fibers made from materials like chalcogenide or photonic crystal fibers.
These advanced materials offer significantly higher performance in certain contexts. For instance, photonic crystal fibers display exceptional control over light propagation and can be designed for specific applications, such as in sensors or high-power laser delivery systems.
The introduction of new dopants also comes with its own set of benefits. Materials like germanium or phosphorus can be added to silica to enhance specific characteristics, such as lowering the loss of signal over long distances. The development of specialized polymers might also augment lightweight and flexible fiber options, increasing ease of installation and reducing material costs for large-scale projects.
Automation in Manufacturing
Let’s not kid ourselves - the future of production relies heavily on automation. As development speeds up, manufacturers are adopting smart technology and robotics to streamline operations. This can be summarized with a couple of main ideas:
- Increased Efficiency: Automated systems can operate continuously and with less error. They enhance the precision of processes, from preform fabrication to fiber drawing.
- Cost Reduction: By reducing manual labor costs and human error, companies can produce optical fibers at a lower cost, which is vital in a competitive market.
Automation also opens doors to real-time monitoring and data analysis. This means manufacturers can gather valuable insights throughout the production process. They can adjust parameters dynamically based on conditions, thus optimizing performance. For example, an automated optical inspection process can ensure the fiber's quality at nearly every stage of production, resulting in fewer defects in the final product.
Sustainability Initiatives
In an age where ecological concerns take center stage, the optical fiber industry isn’t lagging behind. Manufacturers are under increasing pressure to adopt stable practices. Sustainable efforts can manifest in several ways:
- Eco-Friendly Materials: The exploration of biodegradable materials or recycled products for creating fiber optic cables demonstrates a commitment to reducing landfill impact.
- Energy Efficiency: Companies are investing in energy-efficient machinery that consumes less power during production. The move to renewable energy sources is also becoming more popular.
- End-of-Life Solutions: It's imperative to think about what happens to the materials once they reach end-of-life. Strategies for recycling or repurposing used optical fibers could lessen waste and promote a circular economy.
The trend toward sustainability isn't just an option; it’s becoming a core part of how successful businesses operate today.
In summary, the future of optical fiber production is poised for remarkable advancements. Through innovation in materials, automation in manufacturing, and a heightened focus on sustainable practices, the industry is preparing itself for the challenges and demands of tomorrow. By grasping these trends, stakeholders can not only ensure better products but also contribute positively to the environment and society.
The End
In the fast-paced world of technology, understanding optical fiber manufacturing looms large, not just for specialists but for anyone interested in the underpinnings of modern communication. This article shines a light on the multifaceted processes behind optical fibers, emphasizing that the manufacturing techniques and advances are more than mere technical specifications. They represent a confluence of art and science, one that has revolutionized the way information travels.
Reflecting on the content discussed throughout the article, let’s distill the core elements essential to grasping the significance of optical fiber manufacturing:
Recap of Key Points
- Raw Materials: The quality of raw materials, primarily silica, sets the foundation for high-performance optical fibers. The intricacies involved in sourcing high-purity silica are crucial to the fiber’s overall performance.
- Preform Fabrication: Techniques like vapor-liquid-solid growth and modified chemical vapor deposition are pivotal. Each method offers unique advantages and is selected based on the desired fiber properties.
- Draw Process: The art of drawing fibers from preforms requires meticulous control of temperature and speed. Recognizing how these factors interact can help mitigate imperfections in the strands produced.
- Coating Significance: A well-applied protective layer isn’t just an add-on; it’s vital in enhancing durability and performance — ensuring the fiber maintains integrity during installation and use.
- Quality Assurance: Quality control methods, including attenuation testing and refractive index profiling, guarantee that fibers meet stringent standards. This aspect is non-negotiable in a quality-over-quantity market.
- Challenges and Innovations: The challenges of material limitations and environmental impacts fuel ongoing innovations in manufacturing processes, reiterating the importance of adapting to market demands and ecological concerns.
- Future Trends: The shift towards automation and sustainability initiatives signals a promising future, encouraging new thinking and practices in the optical fiber landscape.
In summation, the tapestry of optical fiber manufacturing is rich and complex, woven together by advances in technology, rigorous testing, and passionate pursuit of excellence. For students and professionals alike, understanding these nuances not only enhances knowledge but also ignites a curiosity to explore how future innovations will continue to shape this dynamic field. As optical fibers continue to influence our daily lives, their manufacturing processes will remain a crucial area of study and advancement, reflecting broader trends in global communication and technology.