Understanding Viscosity Curves in Injection Molding
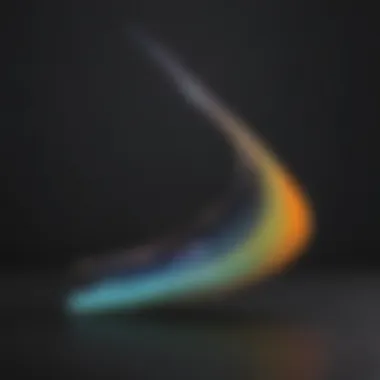
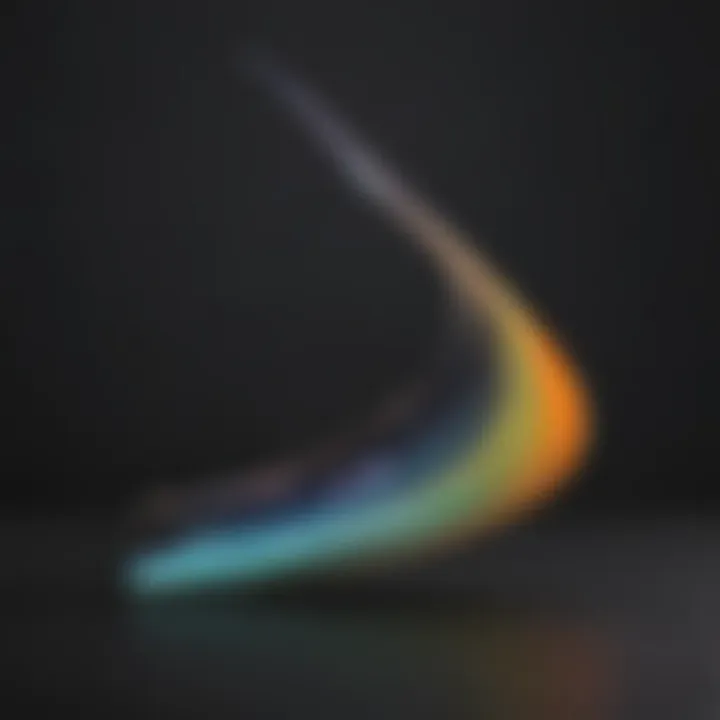
Intro
Understanding viscosity is crucial in the field of injection molding. The viscosity curve provides a visual representation of how material flow behaves under different conditions. This curve is influenced by several factors including temperature, pressure, and the properties of the polymer itself. Each of these elements can change how a material fills a mold, impacting the overall efficiency and quality of the manufacturing process.
Manufacturers aim for optimal mold filling to reduce waste and enhance productivity. To achieve this, a deep analysis of viscosity and its behavior during injection molding is necessary. Various methodologies exist to examine these factors, such as experimental techniques and computational simulations. These approaches reveal insights that not only enhance understanding but also lead to better practices in real-world applications.
As we explore this topic, it’s essential to consider both theoretical aspects and practical implications. Key insights will address the challenges faced and solutions available that can facilitate better outcomes in manufacturing. By examining the viscosity curve, professionals and researchers alike can gain valuable knowledge to improve their processes.
Prologue to Injection Molding
Injection molding is a crucial method in modern manufacturing, particularly effective for producing complex parts at scale. Understanding this process is essential, especially when investigating the influence of material properties like viscosity on the overall quality of molded products. This section will outline the fundamental aspects of injection molding, illustrating its significance in various industries.
Definition and Overview
Injection molding is a manufacturing process where molten material is injected into a mold to create solid parts. Typically, thermoplastics or thermosetting polymers are used. The process begins by heating the material until it reaches a liquid state. Then, this liquid is injected into a closed mold, where it cools and solidifies into the desired shape. This method is favored for its accuracy and ability to produce intricate shapes at a high rate of production.
The advantages of this technique include high repeatability, minimal waste, and the flexibility to use different materials. Therefore, it plays a pivotal role in sectors such as automotive, healthcare, and consumer goods.
Historical Context
The history of injection molding dates back to the mid-19th century. The first patent for an injection molding machine was filed in 1872 by John Wesley Hyatt, who aimed to create a way to mold objects out of celluloid. Initially, the process was labor-intensive and used manual techniques. However, technological advancements in the 20th century significantly improved efficiency. Automated systems were developed, allowing for faster production rates and better control over part dimensions.
Over the years, materials and technologies have evolved. With the advent of computerized controls and sophisticated software, manufacturers can manage the injection process more precisely. This historical perspective informs today’s injection molding practices and addresses the complexities of viscosity in contemporary applications.
Applications in Modern Manufacturing
Injection molding has left a profound impact on various industries due to its versatility. Some of its primary applications include:
- Automotive Industry: Production of components like dashboards, housings, and fuel tanks.
- Consumer Products: Items such as containers, toys, and household appliances benefit from the cost-effectiveness of injection molding.
- Medical Devices: Precise components in medical equipment ensure quality and reliability.
The broad range of applications showcases not only the importance of this process but also the challenges posed by material properties, including viscosity. Understanding how viscosity affects these applications is vital for enhancing performance and reducing defects in molded products.
Understanding Viscosity
Viscosity is a critical aspect of injection molding, influencing both product quality and manufacturing efficiency. By comprehending viscosity, professionals can make informed decisions about material selection and processing conditions. This understanding allows for optimized performance and fewer issues during production.
Basic Definition of Viscosity
Viscosity measures a fluid’s resistance to flow. It can be likened to the thickness of a liquid. A material with high viscosity flows slowly, like honey, while a low-viscosity fluid acts more like water. This property directly affects how materials move through the injection molding process. Properly assessing viscosity helps predict how materials will behave under different conditions, which is essential for designing effective mold and processing strategies.
Measuring Viscosity
Viscometers and Their Types
Viscometers are instruments that measure viscosity, playing a crucial role in quality control during injection molding. There are several types of viscometers, each with its method and application. Some common types include:
- Capillary viscometers: These measure the time a liquid takes to flow through a narrow tube. They are accurate for low-viscosity fluids.
- Rotational viscometers: These measure viscosity by rotating a spindle in a fluid. They are suitable for a wide range of viscosities, making them versatile in industrial applications.
The key characteristic of viscometers is their ability to provide precise readings under controlled conditions. Their benefit lies in ensuring that the right viscosity levels are achieved for specific materials used in injection molding.
Dynamic vs. Kinematic Viscosity
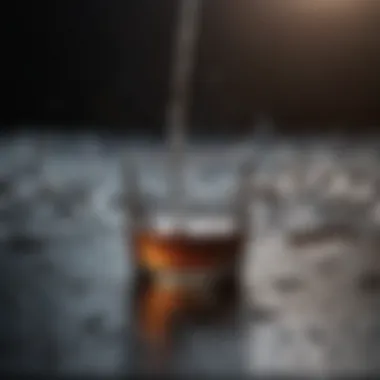
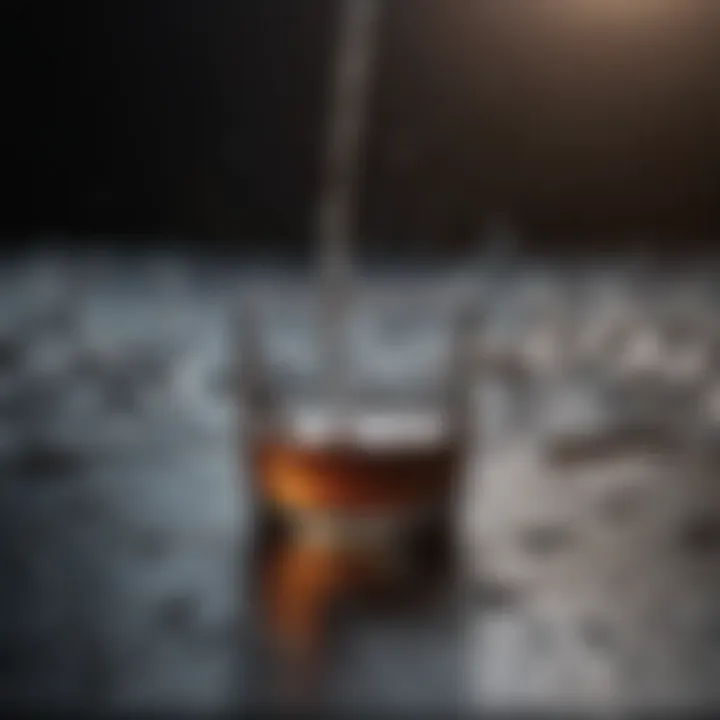
Dynamic viscosity formulates the internal resistance to flow under shear stress. It directly links to the force needed to move a fluid. Kinematic viscosity, in contrast, evaluates the fluid’s resistances to flow, including the effects of density. Both measures are essential for understanding material behavior.
Dynamic viscosity is valuable for calculating the forces necessary for processing, while kinematic viscosity provides insights into how materials will fill molds. Knowing both helps in optimizing the injection molding process by choosing the correct parameters and ensuring high-quality outputs.
Factors Affecting Viscosity
Understanding the factors that influence viscosity is vital for successful injection molding.
Temperature Influence
Temperature plays a significant role in determining a material’s viscosity. Generally, increasing temperature will reduce viscosity, allowing materials to flow more easily. This behavior is essential when adjusting processing parameters. Utilizing proper temperature control enables smoother flow through the mold, improving mold filling and reducing defect risks. In some cases, materials can behave unpredictably if temperature fluctuations occur, making consistent monitoring necessary.
Shear Rate Variability
Shear rate refers to how quickly a fluid is being deformed. It significantly impacts viscosity. High shear rates tend to decrease viscosity for shear-thinning fluids, while shear-thickening fluids display the opposite behavior. Understanding how shear rate affects viscosity is critical for accurately predicting material behavior during injection molding cycles. Adjusting shear rates can help mitigate flow issues, ultimately enhancing production efficiency.
Material Composition
The materials used in injection molding affect viscosity significantly. For example, polymers with different molecular weights or additives can change flow characteristics. The nature of these materials means that viscosity can vary widely even within similar substances. Recognizing how material composition influences viscosity helps manufacturers tailor their processes to reduce defects and achieve consistent product quality.
The Viscosity Curve Explained
Understanding the viscosity curve is crucial in the context of injection molding. It serves as a fundamental basis for material processing and performance. The curve provides valuable insights into how well a material will flow under various conditions, which directly influences the efficiency of the mold filling process and the overall quality of the final product.
Definition of the Viscosity Curve
The viscosity curve is a graphical representation that illustrates the relationship between viscosity and shear rate for a particular material. It showcases how a material will behave when subjected to different levels of stress, which is common in manufacturing processes like injection molding. By analyzing this curve, manufacturers can predict how materials will flow and fill molds efficiently.
Components of the Viscosity Curve
Viscosity Range
The viscosity range indicates the different viscosity values a material can exhibit during processing. This range often varies significantly with changes in temperature and shear rate. A narrower viscosity range can be beneficial. It allows for more precise predictions during the molding process, leading to consistent results. When materials have a well-defined viscosity range, the control over flow behavior is enhanced. However, if the viscosity range is too wide, it can result in processing challenges, such as uneven filling or increased likelihood of defects.
Flow Behavior
Flow behavior refers to the manner in which a material moves and deforms under applied stress. In injection molding, understanding this behavior is essential. It determines how well the molten material fills the mold and the speed at which it does so. A fluid that exhibits a Newtonian flow behavior has a constant viscosity, regardless of shear rate, making it easier to predict and manage during processes. Conversely, non-Newtonian materials exhibit varying viscosity, which can complicate the process, leading to issues in filling and potential defects.
Interpreting the Viscosity Curve
Interpreting the viscosity curve requires careful analysis of the data presented on it. Factors such as temperature, composition of the material, and shear rate must be considered. By understanding these elements, professionals can tailor their injection molding process more effectively. A well-interpreted viscosity curve allows for better planning in terms of material selection and process optimizations, reducing the chances of defects and enhancing overall product quality.
"Understanding the viscosity curve is key for optimizing the flow process in injection molding."
In summary, the viscosity curve is a pivotal tool that not only aids in material selection but also enhances process efficiency during injection molding, making it indispensable for manufacturers seeking to improve their production methods.
Role of Viscosity in Injection Molding
The viscositiy plays a crucial role in the injection molding process. Understanding this role helps optimize production methods and enhances product quality. Proper management of viscosity is essential for achieving desired flow characteristics, which directly influences material handling in the molding machines. This aspect is not just a theoretical concern; its practical implications can affect efficiency, cost, and product performance.
Impact on Material Flow
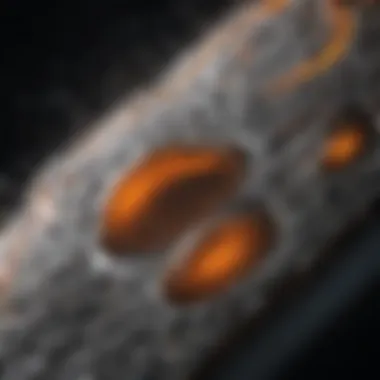
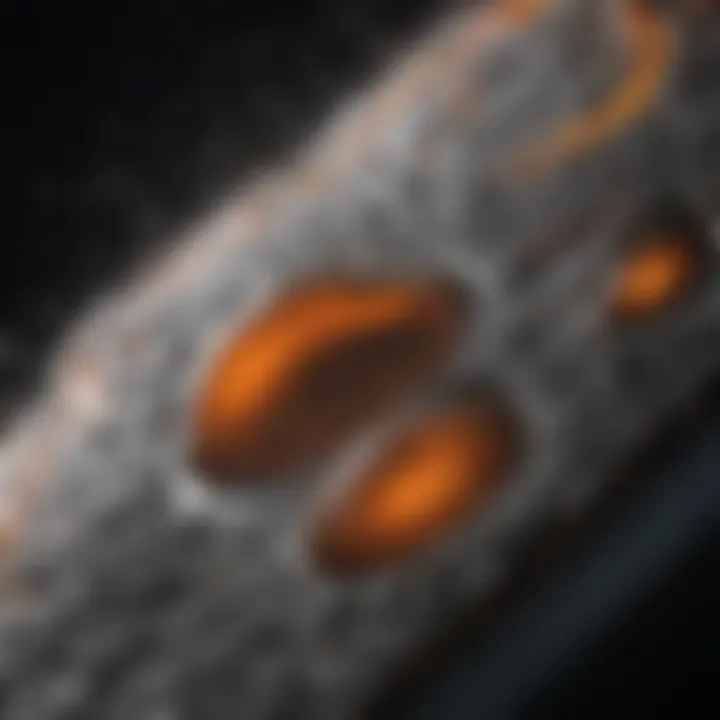
Material flow is a fundamental aspect of the injection molding process. Viscosity determines how easily the material can move through the injection system and fill the mold cavity. If viscosity is too high, the flow rate may decrease, leading to issues such as short shots, where the material fails to completely fill the mold. Conversely, if viscosity is too low, the material may flow too easily, compromising the structural integrity of the final product.
Maintaining the right viscosity is crucial for uniform material flow. By adjusting processing conditions like temperature and shear rate, manufacturers can manipulate viscosity to achieve the desired flow behavior. This ensures that materials are delivered consistently during the injection phase, minimizing defects and enhancing the overall quality of the molded parts.
Mold Filling Efficiency
Mold filling efficiency directly relates to how effectively the material occupies the mold cavity. A well-controlled viscosity leads to improved mold filling. This efficiency is paramount for large-scale production, where time and material costs are critical. Higher filling efficiency reduces cycle times and prevents defects associated with incomplete mold filling.
When viscosity is accurately monitored and adjusted, it allows for optimal injection speeds and pressures, maximizing the filling process. Such precision ensures that the channels within the mold are filled without leaving any gaps, thereby enhancing product quality and reducing rework.
Cooling and Solidification Considerations
After the injection phase, effective cooling and solidification of the molded product are essential. The viscosity of the material at various stages affects how quickly it cools and solidifies. As the material transitions from a molten state to a solid form, the cooling rate is influenced by its viscosity.
If the viscosity is too high during cooling, it may lead to uneven solidification. This can result in warping or dimensional inaccuracies in the final part. On the other hand, optimal viscosity helps achieve a balanced cooling rate, preventing defects and ensuring that parts maintain their designed specifications.
In summary, understanding and managing viscosity is vital in the injection molding process. High material flow, efficient mold filling, and precise cooling solidification are all heavily dependent on it. Careful consideration of these factors allows manufacturers to enhance production efficiency and product quality.
Common Issues Related to Viscosity in Injection Molding
The relationship between viscosity and injection molding is essential, as it influences the quality of the final product. Understanding the common issues related to viscosity can help professionals optimize the injection molding process. This section explores two main categories of problems: flow induced defects and inconsistent product quality.
Flow Induced Defects
Flow induced defects arise from the interaction between resin viscosity and processing conditions. These defects can significantly impact production efficiency and product performance.
Short Shots
Short shots refer to a situation where the mold does not fill entirely with material. This issue can lead to incomplete products, affecting their usability. The key characteristic of short shots is their ability to indicate issues in material flow. Often, short shots occur when the viscosity of the resin is too high for the injection speed. This problem is a crucial aspect of injection molding as it directly correlates to production yield. The unique feature of short shots is that they can serve as indicators of process parameters that need adjustment. For example, if a specific material frequently results in short shots, it may highlight the need for either a different processing strategy or material. Understanding short shots can lead to better material and process choices.
Flash Formation
Flash formation happens when excess molten plastic escapes from the mold cavity, leading to thin, unwanted features on the part. The key characteristic of flash formation is the surplus of material caused by improper mold clamping or viscosity mismatches. It is a significant issue because it not only affects aesthetics but also can compromise the structural integrity of a component. The advantage of recognizing flash formation is that it prompts necessary inspections of the molding process. The unique feature here is that flash can often indicate a need for improved mold design or better material selection. Although flash may at first seem to be a minor defect, it has substantial implications for product performance and appearance.
Inconsistent Product Quality
Inconsistent product quality reflects the reliability of the manufacturing process. Variability can arise from numerous factors, primarily tied to viscosity.
Dimensional Variability
Dimensional variability refers to deviations from specified measurements in produced parts. This issue can emerge from fluctuations in viscosity during the injection process. The key characteristic of dimensional variability is its direct effect on product specification compliance. It is a major concern because it can result in parts that do not fit or function as intended. Understanding dimensional variability can be crucial in achieving a consistent manufacturing process. This unique feature means that producers must monitor viscosity closely to maintain uniformity in product dimensions. Addressing these issues often involves constant evaluation of both material inputs and processing parameters.
Surface Finish Problems
Surface finish problems arise from inconsistencies in the texture and appearance of molded products. Factors such as viscosity changes during molding can exacerbate these issues. The key characteristic of surface finish problems is their impact on the visual and functional quality of the final product. This issue is particularly significant in consumer-facing applications where aesthetics matter. The unique feature is that surface finish problems can often be corrected by adjusting processing conditions, such as temperature and injection speed, ensuring a smoother final product. Recognizing surface finish problems allows manufacturers to hone in on improvements to production methods and material selection.
Addressing these common issues is essential for enhancing the efficiency and reliability of the injection molding process.
Optimizing the Injection Molding Process via Viscosity Management
Optimizing the injection molding process through effective viscosity management is critical for achieving desired product quality and operational efficiency. The viscosity of the material used in injection molding dictates how well the material flows during processing, influencing a range of outcomes from mold filling to cooling times. By carefully managing viscosity, manufacturers can minimize defects and improve the consistency of their final products.
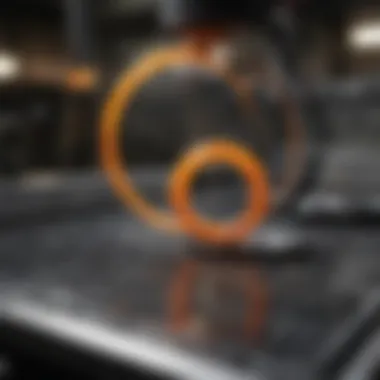
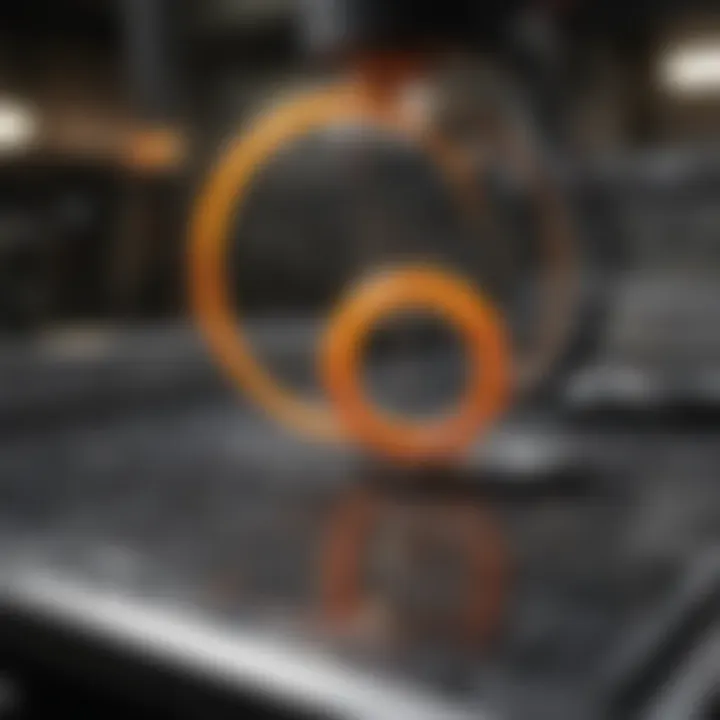
Material Selection
Material selection is a fundamental aspect when it comes to viscosity management in injection molding. Each polymer has its unique viscosity characteristics, which directly affect the processing behavior. Selecting the right material with appropriate viscosity can lead to improved flow properties and better mold filling. It is vital to consider not only the viscosity but also how it may change under different processing conditions, such as temperature and shear rates. Some materials may offer higher initial flow but become too viscous under heat, leading to processing complications. Thus, careful material selection lays the groundwork for a successful injection molding operation.
Processing Parameters
Adjusting processing parameters is another essential factor in viscosity management. This includes controlling temperature and injection speed. Each element plays a significant role in flow characteristics, which in turn affects the overall efficacy of the injection molding process.
Temperature Control
Temperature control in the injection molding process is crucial for managing material viscosity. Higher temperatures can reduce viscosity, allowing for better flow during the injection phase. This is essential as flow behavior directly correlates to mold filling and eventual product quality. The key characteristic of temperature control is its ability to modify the viscosity of thermoplastic materials, making it a popular choice among manufacturers. However, excessive heat can also degrade materials, leading to unwanted chemical reactions. Hence, a balanced approach in temperature management is vital to ensure ideal viscosity without compromising material integrity.
Injection Speed Adjustments
Injection speed adjustments are another vital optimization technique in injection molding. The injection speed impacts the shear rates experienced by the material, affecting its viscosity. Each material may respond differently to varying injection speeds, which can enhance or hinder the filling of complex mold geometries. The key characteristic of injection speed is its direct influence on the flow of the polymer melt. Adjusting the speed allows for customized process control tailored to specific molds and materials.
Altering injection speed can often lead to improved part quality and reduced cycle times. However, it is also important to recognize that rapid injection can cause defects such as jetting or increased pressure within the mold. Thus, finding the optimal injection speed is critical for achieving the best flow characteristics while maintaining product quality.
By integrating meticulous material selection and precise processing parameter adjustments, manufacturers can effectively manage viscosity and optimize their injection molding processes, resulting in products of higher quality with reduced defect rates.
Future Trends in Viscosity Measurement and Injection Molding
The landscape of viscosity measurement and injection molding is undergoing significant transformation. It is essential to recognize the factors driving these changes, as they can greatly impact efficiency and the quality of products produced. Understanding future trends allows professionals in manufacturing to anticipate challenges and capitalize on emerging technologies.
Advancements in Technology
Recent developments in technology are reshaping the way viscosity is measured and managed in injection molding. Innovations such as laser-based viscometers and microfluidic devices are becoming more prevalent. These devices provide more accurate and faster measurements of viscosity, which in turn can inform immediate adjustments in processing parameters.
Furthermore, automation and digitalization are streamlining viscosity measurement. Automation reduces the likelihood of human error and ensures consistent data collection. Sensors integrated into molding machines can now monitor viscosity in real-time, allowing for immediate feedback. This leads to better control over the injection process and improved material flow, ultimately enhancing production efficiency.
The Role of Smart Manufacturing
Smart manufacturing is redefining traditional manufacturing processes through the integration of data analytics, machine learning, and the Internet of Things (IoT).
- Data Analytics: By analyzing historical viscosity data, manufacturers can predict trends and optimize future molding cycles. This predictive capability allows for adjustments in real-time, minimizing defects and improving product conformity.
- Machine Learning: Algorithms can adaptively learn from ongoing processes. They adjust parameters dynamically, ensuring that viscosity remains within optimal ranges for various materials and environmental conditions.
- IoT Implementation: IoT devices can connect machinery and sensors, facilitating seamless communication. This interconnectedness enhances monitoring and control, ensuring that viscosity data is readily available to operators and engineers.
In summary, as viscosity measurement technology progresses and smart manufacturing techniques are adopted, the injection molding process is expected to become more efficient. This transformation is crucial not only for maintaining competitiveness in the industry but also for addressing the complexities of modern production demands.
By focusing on future trends in viscosity measurement and injection molding, professionals can prepare for changes that will not only enhance efficiency but also lead to innovative applications in materials science and engineering.
Closure
The conclusion serves as a critical focal point within this article. It encapsulates the essential insights that have been discussed, illustrating the significance of the viscosity curve in the injection molding process. The viscosity curve provides invaluable information about how materials behave under various conditions, influencing both the efficiency and quality of manufacturing outcomes.
A primary benefit of understanding the viscosity curve is its role in optimizing the injection molding process. With knowledge of how temperature and shear affect viscosity, professionals can make informed decisions about processing parameters. This aids in minimizing defects and improving mold filling efficiency.
Furthermore, the various factors that affect viscosity, such as material composition, cannot be overlooked. They play a pivotal role in shaping the final product's quality. Thus, a comprehensive grasp of these aspects leads to better material selection and processing strategies.
In summary, this article emphasizes the importance of the viscosity curve. It serves as a foundation for further exploration and research in injection molding. The insights provided are not just theoretical; they have practical implications for industry practitioners and researchers alike, guiding them toward effective solutions and innovations in manufacturing practices.
Summary of Key Points
- Understanding the viscosity curve is essential for optimizing injection molding.
- Viscosity influences mold filling and cooling rates directly.
- Factors such as temperature and shear rate are crucial.
- Proper management of viscosity can reduce defects in products.
- Material composition plays a significant role in viscosity behavior.
Future Implications for Research and Practice
Research focused on viscosity measurement technologies and their evolution will likely yield significant benefits for the industry. For instance, advancements in real-time viscosity monitoring could provide manufacturers with immediate feedback, leading to quicker adjustments in production parameters.
Moreover, the integration of smart manufacturing practices, including machine learning and IoT monitoring, can enhance decision-making processes regarding viscosity. By analyzing historical data related to viscosity, companies can develop predictive maintenance schedules and optimize their materials for efficiency. Overall, the future of viscosity in injection molding promises opportunities for both innovation and improved processes, warranting further investigation and commitment from industry stakeholders.