In-Depth Overview of Quenching Tanks in Industry
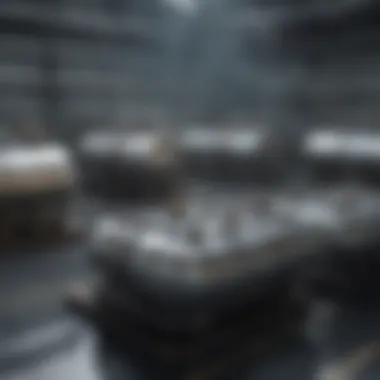
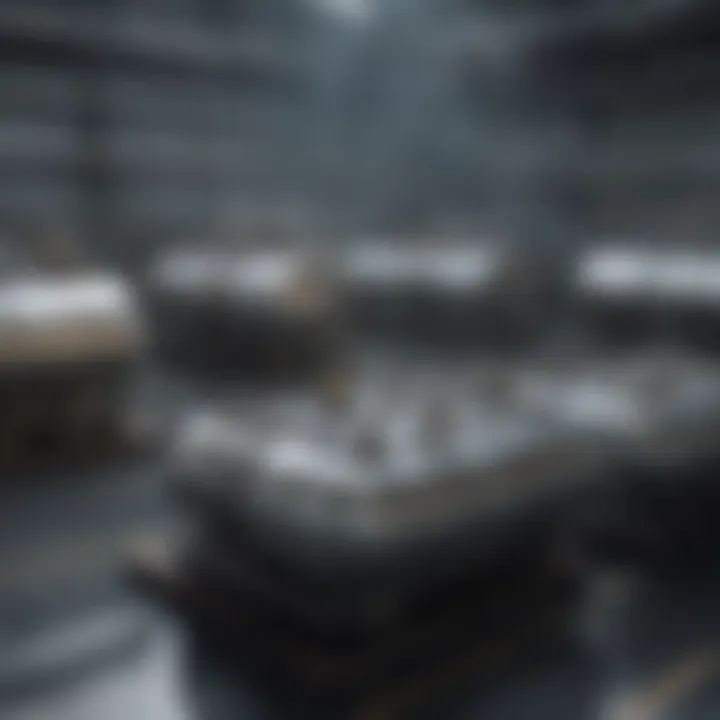
Intro
Quenching tanks are a fundamental component in thermal processing across various industries. Their primary function is to rapidly cool materials, often metals, to enhance properties such as hardness and strength. This article will provide a comprehensive analysis of quenching tanks, focusing on their designs, functions, and applications in industrial settings.
Understanding the operational mechanics of quenching tanks is crucial for professionals looking to optimize processes in manufacturing. The topics discussed will include material considerations – which affect the durability and effectiveness of the tanks – as well as safety protocols essential for handling heated materials.
Temperature control plays a significant role in the efficiency of quenching tanks. Fluid dynamics within the tank can influence not only the cooling rate but also the structural integrity of the materials being processed. This article will examine case studies that illustrate the evolving nature of these systems and the advancements in technology that enhance sustainability in manufacturing.
Given this backdrop, the first section of our analysis will shift into the methodologies employed to study quenching tanks and their operational efficiencies.
Methodology
The research presented in this article is based on a variety of investigation methods used to evaluate the performance and design of quenching tanks.
Overview of research methods used
Primary research involved interviewing industry experts who specialize in thermal processing. These discussions provided insights into real-world applications and innovations in quenching tank technology. Additionally, a review of existing literature on thermal processing was conducted to gather data on the operational mechanics and design variations of quenching tanks.
Data collection techniques
Data collection utilized case studies from various industries, such as aerospace and automotive manufacturing. These studies provided quantitative data regarding cooling rates, efficiency metrics, and material properties post-quenching. Furthermore, online resources like Wikipedia and Britannica were consulted to supplement the findings with reliable, contextual information.
The culmination of these methods allows for a nuanced analysis of quenching tanks, ensuring that the information presented is not only accurate but also relevant to current industry practices.
Future Directions
Looking ahead, the field of thermal processing is set to evolve rapidly.
Upcoming trends in research
Emerging trends indicate a growing interest in automation within quenching processes. Advanced control systems can provide more precise temperature regulation and monitoring, improving product consistency and reducing waste.
Areas requiring further investigation
While much research has been dedicated to the mechanical aspects of quenching tanks, there is a need for more studies focusing on the environmental impact of quenching fluids. Understanding the sustainability of these processes will be essential as industries shift towards greener practices.
The analysis of quenching tanks encapsulates not only the technical facets but also the broader implications for industry standards and environmental care. Engaging with case studies and data from various sectors will provide a deeper understanding of how these systems adapt to the challenges of modern manufacturing.
Prologue to Quenching Tanks
Quenching tanks play a pivotal role in the field of thermal processing. They are essential in the heat treatment of metals and other materials. Understanding their functions and designs is crucial for engineers, technicians, and researchers. Quenching tanks are not only vital for the production efficiency but also contribute significantly to the structural integrity of materials.
The primary purpose of a quenching tank is to facilitate rapid cooling of heated materials. This process alters the material properties, such as hardness and durability. By utilizing different mediums, these tanks optimize the cooling rates according to the requirements of specific materials. Therefore, knowledge of quenching tank characteristics directly impacts production outcomes.
Definition and Purpose
A quenching tank is a vessel designed to rapidly cool hot materials, typically metals, using a quenching medium such as water, oil, or other fluids. The cooling process is performed after a heating treatment, aimed at enhancing the material’s properties. It prevents deformation and ensures uniformity in the heat-treated product.
The purpose of quenching is to achieve desired microstructural changes in materials. For instance, quenching can lead to increased hardness in steel alloys. This change occurs due to the transformation of austenite to martensite, which is a harder phase of steel. Therefore, the effective use of quenching tanks can substantially enhance product quality in industrial applications.
Historical Context
The use of quenching in metallurgy has a rich history, dating back thousands of years. Initially, ancient blacksmiths discovered that cooling hot metals could improve their properties. This instinctive understanding led to the advent of various quenching methods. The Roman Empire, for example, employed quenching techniques to create stronger armor and weapons.
With the industrial revolution, quenching techniques evolved significantly. The introduction of specialized quenching tanks allowed for better control over the cooling processes. This was essential as production moved from artisanal methods to large scale manufacturing. Innovations in materials and technologies have continued to refine quenching methods. Today, the development of sophisticated quenching tanks incorporates automation and advanced monitoring systems. Understanding the historical context provides insight into the evolution of these critical systems in modern applications.
Fundamentals of Thermal Processing
Thermal processing is a critical aspect of materials engineering and manufacturing that focuses on altering the physical and sometimes chemical properties of materials through controlled heating and cooling. In this article, the exploration of fundamentals of thermal processing, particularly related to quenching tanks, unveils various dimensions of its importance. Quenching tanks are specialized equipment used during the heat treatment process that ensure optimal results in material strength, hardness, and overall durability. Their role is not merely auxiliary; it is fundamental to achieving desirable material properties.
Key elements of thermal processing include:
- Heat Treatment: This process is essential for modifying the properties of metals and alloys. It creates specific phases in materials that define their strength and toughness. Understanding how heat treatment aligns with quenching processes allows for more informed design and operational choices.
- Quenching Mechanism: This refers to rapidly cooling heated materials. The methods employed, whether using water, oil, or polymer solutions, greatly affect the final material properties. The efficiency of quenching relies heavily on controlling the cooling rate, which is where quenching tanks come into play.
- Material Behavior: Different materials respond distinctively to heat treatment and quenching processes. A comprehensive grasp of these behaviors is vital for industries aiming to meet specific mechanical properties in their end products. By examining how varying materials interact with heat treatment, one can better tailor quenching processes for various applications.
The benefits of incorporating efficient thermal processing within manufacturing are manifold:
- Enhanced Mechanical Properties: Proper thermal processing significantly improves the strength and hardness of materials, making them suitable for high-performance applications.
- Reduced Scrap Rates: Effective quenching reduces defects and increases yield, directly translating to economic benefits for manufacturers.
- Increased Reliability: Consistent thermal processing leads to predictable performance of materials, instilling confidence in manufacturing processes.
Heat Treatment Overview
The heat treatment process refers to various techniques applied to alter the physical and sometimes chemical properties of a material. It includes processes like annealing, normalizing, and tempering, each with distinct purposes and outcomes. The general objective is to improve hardness, ductility, and overall toughness, which are crucial for many applications.
This process entails heating a material to a specific temperature and maintaining it for a set period before cooling it rapidly, commonly known as quenching. The careful selection of temperature and time plays a significant role in achieving the desired mechanical properties.
Role of Quenching in Heat Treatment
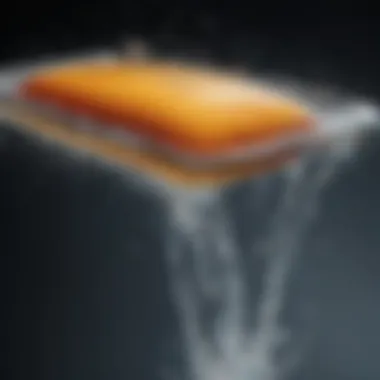
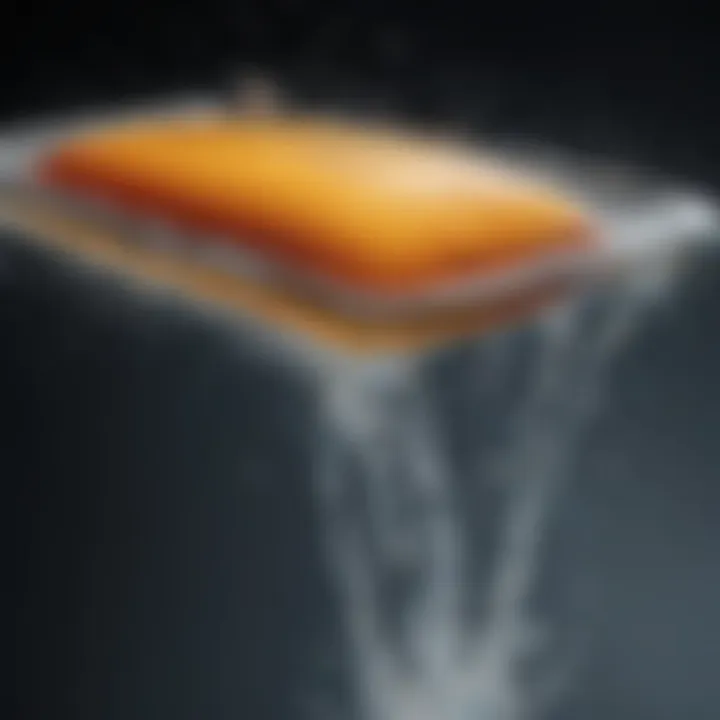
Quenching is a vital component of heat treatment. It involves cooling heated materials rapidly, often at rates higher than those achieved by air cooling or other heat removal methods. This rapid cooling process influences the microstructure of the material, leading to the formation of hard phases such as martensite in steel.
The role of quenching can be elaborated as follows:
- Formation of Hard Phases: The rapid cooling during quenching leads to desired phases in steel, which enhances hardness.
- Control Over Ductility and Strength: By varying quenching methods and mediums, the final properties of the material can be tailored to suit specific applications.
- Minimization of Internal Stresses: Well-executed quenching helps minimize internal stresses resulting from uneven cooling, a factor that can lead to warping or cracking.
Understanding quenching's role in heat treatment allows engineers and materials scientists to optimize the manufacturing processes for various materials, ensuring that products meet the necessary standards and requirements.
Types of Quenching Tanks
The various types of quenching tanks play a significant role in thermal processing. Each type serves distinct functions based on the materials being treated, the desired properties of the end products, and the operational parameters of the manufacturing process. Understanding the characteristics, benefits, and limitations of these tanks allows industry professionals to make informed decisions that optimize heat treatment processes.
Water Quenching Tanks
Water quenching tanks are commonly used due to the accessibility and cost-effectiveness of water as a quenching medium. In this method, the heated material is immersed in water, which leads to rapid cooling. This cooling rate is critical as it affects the microstructure and mechanical properties of the material.
The benefits of water quenching include:
- Cost-efficiency: Water is readily available and inexpensive compared to alternative quenching media.
- Rapid cooling: The high thermal conductivity of water ensures quick dissipation of heat, which is ideal for certain steel types that require martensitic transformation.
- Uniform cooling: Water quenching offers a consistent temperature distribution, reducing thermal gradients.
However, it is crucial to monitor the cooling rate closely. If excessive, it may lead to cracking or distortion of the workpiece. Thus, appropriate application and control are essential.
Oil Quenching Tanks
Oil quenching tanks utilize oil as the cooling medium, providing a slower cooling rate compared to water. This slower rate is particularly beneficial for certain alloys and parts, where reduced risks of cracking and distortion are required.
Key considerations for oil quenching include:
- Lower cooling rates: Favorable for materials sensitive to thermal shock.
- Enhanced lubrication: Oil not only cools but also lubricates the surface of the material, which helps prevent oxidation.
- Versatility: Different oil types can be selected based on specific cooling requirements.
Even though oil quenching reduces the chances of defects, the setup typically requires longer cooling times. Moreover, fire hazards must be managed due to the flammability of oil.
Polymer Quenching Systems
Polymer quenching systems are gaining popularity as a modern alternative to traditional water and oil quenching. These systems use polymer solutions that provide a rate of cooling between water and oil. The key feature of polymer quenching is the ability to customize the polymer concentration to suit specific cooling rates and applications.
Advantages of polymer quenching include:
- Reduced risks of cracking: By controlling the cooling rate, the stress levels induced into the material can be minimized.
- Environmentally friendly: Polymer fluids can be less harmful to the environment compared to oil.
- Consistency in performance: Polymer blends maintain stable properties over various operating conditions.
However, it may require a more complex setup and regular monitoring of polymer properties to optimize their effectiveness in quenching processes.
Brine Quenching Applications
Brine quenching involves using a saltwater solution as a quenching medium. This method offers certain advantages, especially in cooling performance. The higher density of brine enhances heat transfer compared to water alone. It leads to very efficient cooling rates, particularly suitable for high-carbon steels.
Benefits of brine quenching are:
- Faster cooling rates than water due to enhanced thermal properties.
- Improved hardness in certain materials that benefit from rapid cooling.
- Effective for complex geometries where uniform cooling must be ensured.
On the downside, brine solutions can be corrosive, requiring careful material selection for quenching tanks and equipment to prevent degradation.
In summary, an understanding of various types of quenching tanks aids industries in selecting the right mechanism for specific applications. Choosing the correct type ensures optimal heat treatment outcomes and leads to quality improvements in the final products.
Design Considerations
Design considerations play a pivotal role in the functionality and efficiency of quenching tanks. These elements are fundamental for optimizing performance, ensuring safety, and reducing operational costs. Each aspect—from material selection to dimensions and flow dynamics—carries significant weight in determining how effectively a quenching tank works in real-world applications.
Material Selection
Choosing the right materials for constructing quenching tanks cannot be overstated. Different materials exhibit varied thermal properties and resistances to corrosion, wear, and other environmental factors. Common materials include,
- Stainless Steel: Popular for its corrosion resistance and durability, stainless steel is often favored, especially in industries with strict hygiene regulations.
- Mild Steel: This option is cost-effective but may require protective enamel coatings to enhance its lifespan against rust and other corrosive factors.
- Special Alloys: In specialized applications, such as aerospace, certain alloys may be required to withstand extreme conditions.
The selection process involves assessing not only material properties but also the specific requirements of the quenching process—whether it's resistance to pitting from saltwater or thermal stress from rapid cooling.
Dimensions and Capacity
Dimensions and capacity are crucial variables. The size of a quenching tank must align with the volume of the parts being treated and their configuration. A tank that is too small may not provide adequate cooling, while one that is excessively large can lead to inefficient heat transfer and increased fluid costs.
Key factors affecting dimensions include:
- Part Size: Larger components require more space, influencing the tank's footprint.
- Batch Size: High production demands may necessitate larger tanks or multiple units in parallel.
- Heat Transfer Efficiency: Proper tank dimensions aid in achieving optimal heat transfer rates, ensuring uniform cooling of all surfaces.
Flow Dynamics
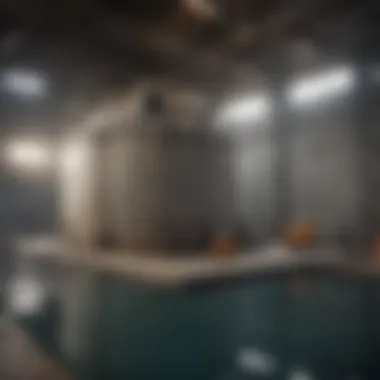
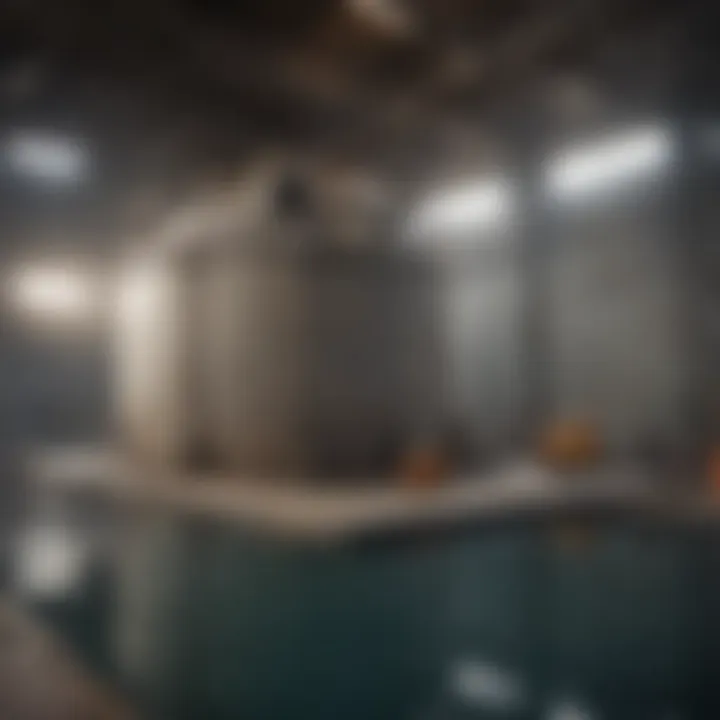
The flow dynamics within a quenching tank affect thermal exchange and the overall effectiveness of the heat treatment process. Understanding fluid behavior is vital for designing tanks that promote even cooling. Important aspects to consider include:
- Turbulence: Controlled turbulence enhances heat transfer by preventing localized hot spots. However, excessive turbulence can lead to uneven cooling rates.
- Inlet and Outlet Design: Proper placement of inlets and outlets ensures optimal fluid circulation. A well-designed system prevents stagnant areas, which can lead to inconsistent cooling.
- Fluid Viscosity: Different quenching fluids (water, oil, brine) have unique viscosity properties that influence flow patterns. This must be taken into account during the design phase.
Effective design maximizes the quenching process and minimizes risks associated with uneven cooling.
Each of these design aspects must be thoughtfully integrated. They not only enrich the functionality of quenching tanks but also contribute to the long-term reliability and safety of industrial operations. A robust understanding of these considerations enables professionals to make informed decisions that align with both production goals and safety standards.
Operational Mechanics
Understanding the operational mechanics of quenching tanks is critical for effective thermal processing. This section explores various aspects like heating, cooling cycles, temperature monitoring, and fluid dynamics. These elements are crucial because they directly impact the quality of the heat treatment process, which is essential in various industries, including automotive and aerospace.
Heating and Cooling Cycles
Heating and cooling cycles are fundamental to the quenching process. During heat treatment, materials often require precise heating to specific temperatures for sufficient duration prior to quenching. Once the desired temperature is achieved, rapid cooling is initiated. This is where quenching tanks play a vital role. The fluid medium in the tank must maintain consistent properties to ensure uniform cooling.
Generally, the cooling rate impacts the mechanical properties of materials. A fast cooling rate can lead to increased hardness but may also cause brittleness. Conversely, a slow cooling rate can achieve desired ductility but at the cost of hardness.
Considerations in cycle design include:
- Duration: How long to keep the material at target temperature.
- Fluid temperature: The starting temperature of the quenching medium.
- Quench medium choice: Different media, such as water or oil, offer varied cooling rates.
Temperature Monitoring
Temperature monitoring within quenching tanks is essential for controlling the heat treatment process. Accurate measurements ensure that the temperatures stay within the acceptable range.
Temperature can fluctuate due to several factors, including environmental conditions, fluid properties, and even the introduction of heated materials. Without effective monitoring, inconsistency in the treatment process can occur, affecting material performance.
Leveraging advanced temperature monitoring systems brings several benefits:
- Real-time data provides immediate feedback for operational adjustments.
- Enhanced quality control through systematic data recording.
- Reduced risk of overheating or underheating materials.
Fluid Dynamics Principle
Fluid dynamics is another critical aspect of quenching tank operations. It encompasses how fluids move and the forces exerted by and on these fluids during the quenching process. Adequate fluid circulation within the tank ensures consistent cooling across different parts of a material.
Key concepts include:
- Laminar vs. turbulent flow: Turbulent flow enhances heat transfer rates, which is beneficial for effective quenching.
- Heat transfer mechanisms: Conduction, convection, and sometimes radiation play roles in cooling processes.
Understanding these principles enables engineers and operators to optimize tank designs, improve cooling rates, and ultimately enhance the quality of the heat-treated materials. Utilizing computational fluid dynamics simulations can provide deeper insights and validate design choices.
Optimizing the operational mechanics of quenching tanks leads to better performance and efficiency in thermal processing applications.
Safety Protocols
In the context of quenching tanks, safety protocols hold significant importance. The processes involved in thermal treatments can be hazardous, and proper safety measures are essential for the well-being of operators and the integrity of equipment. Addressing safety not only complies with regulatory standards but also enhances operational efficiency and prevents costly downtime caused by accidents. Therefore, implementing robust safety protocols is fundamental to managing risks associated with quenching operations.
Hazard Identification
Recognizing potential hazards in quenching tanks is the first step in creating a safe operational environment. Some common hazards include:
- High Temperatures: The rapid cooling of metals can result in steam generation and possible explosions.
- Chemical Exposure: Quenching fluids can be hazardous chemicals that pose risks to health.
- Mechanical Risks: The equipment used in quenching can lead to injuries if not operated properly.
A thorough assessment of these hazards should involve identifying specific risks related to tank design and operation. Conducting regular risk assessments and maintaining up-to-date safety data sheets for quenching fluids can help in pinpointing areas for improvement.
Risk Mitigation Strategies
Once hazards are identified, implementing risk mitigation strategies becomes necessary. Here are some effective methods:
- Safety Training: Regular training sessions for personnel on operational and emergency procedures can significantly reduce risks.
- Protective Equipment: Ensuring that all workers wear appropriate personal protective equipment, such as gloves, goggles, and heat-resistant clothing.
- System Maintenance: Routine inspections and maintenance of quenching tanks help in preventing mechanical failures that can cause accidents.
- Emergency Protocols: Establishing clear emergency response plans to deal with incidents, including spills, leaks, and equipment failures.
Effective risk mitigation not only protects staff but also ensures consistent production quality, which is crucial in industries relying on heat treatment processes.
By continuously evaluating safety protocols and integrating new technologies, industries can greatly enhance the safety of quenching operations. As the field advances, the emphasis on safety will remain a pivotal aspect of operating quenching tanks.
Case Studies of Quenching Tank Applications
Examining the applications of quenching tanks in real-world scenarios provides valuable insights into their significance in various industries. The case studies reveal the practical benefits, choices made in design and material, and the implications of using different quenching methods. This section highlights how specific industries benefit from tailored quenching processes and offers lessons in efficiency and innovation.
Automotive Industry
In the automotive industry, quenching tanks play a crucial role in the heat treatment of components such as gears, axles, and frame parts. These components require precise heat treatment to achieve desired mechanical properties, including hardness and strength. The importance of quenching lies in rapidly cooling metal parts to lock in specific microstructures formed during heating.
Key Elements:
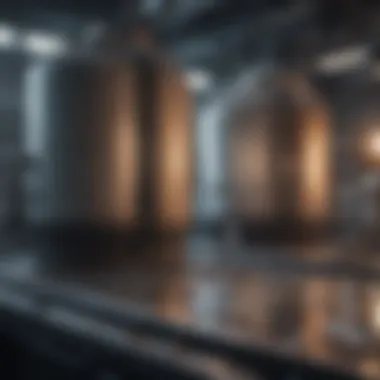
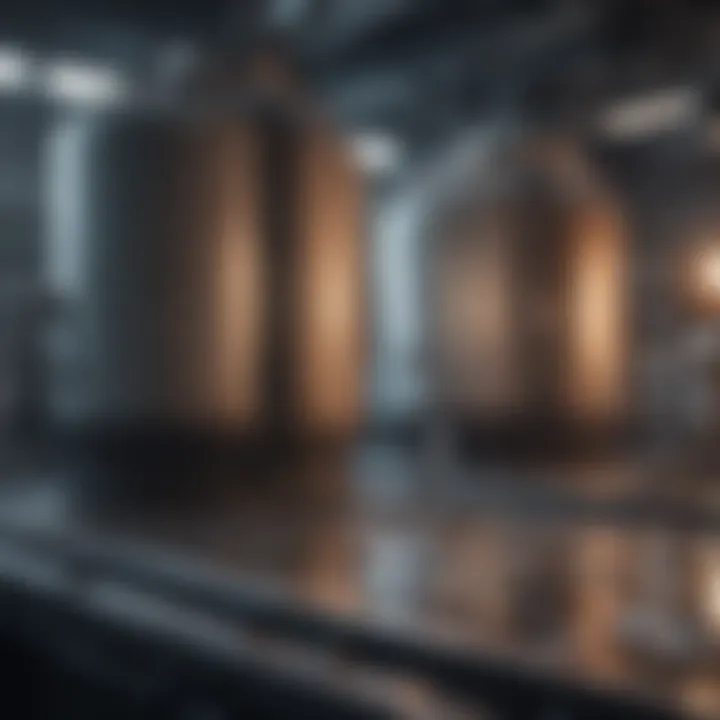
- Material Requirements: Automotive manufacturers often use steels like martensitic and alloy steels, which demand specific cooling rates.
- Process Design: Quenching processes are designed for high volume and consistency, ensuring each part meets stringent quality standards. This consistency reduces waste and improves production time.
Benefits:
- Enhanced performance and durability of automotive parts, resulting in safer vehicles.
- Improved fuel efficiency attributed to lighter and stronger components.
Aerospace Sector
The aerospace industry demands high-performance materials that can withstand extreme conditions. Quenching tanks are utilized for heat treating titanium alloys, steel components, and aluminum parts. These materials require careful thermal processing to maintain integrity and performance in flight.
Considerations:
- Precision Cooling: The quenching process must be exact. Too fast cooling can lead to cracking, while too slow may yield unsatisfactory mechanical properties.
- Custom Solutions: Different aviation parts necessitate various quenching mediums and temperatures.
Advantages:
- Increased reliability and performance of aerospace components.
- Compliance with stringent industry regulations, enhancing safety in air travel.
Tool Manufacturing
The tool manufacturing sector relies heavily on the quenching process to produce cutting tools, dies, and molds. The hardness and wear resistance of these tools directly impact their longevity and efficiency. Quenching tanks provide the necessary environment for obtaining required hardness levels.
Process Attributes:
- Diverse Materials: Tool steels and carbides are common materials that need very controlled cooling rates to achieve optimal characteristics.
- Innovative Technologies: Many manufacturers are integrating automated quenching systems to maximize efficiency and minimize manual intervention.
Impacts:
- Significant improvements in the life cycle of tools, reducing costs over time.
- Enhanced cutting performance, resulting in higher productivity in manufacturing processes.
"The role of quenching tanks in manufacturing is crucial. As industries evolve, so too must the processes that ensure part integrity and performance."
Through these case studies, it is clear that the application of quenching tanks is not merely a functional necessity but a strategic advantage in manufacturing. The detailed examination of how automotive, aerospace, and tool manufacturing industries employ quenching systems underscores the need for continual innovation in thermal processing.
Technological Advancements in Quenching Tanks
Technological advancements in quenching tanks play a critical role in enhancing thermal processing. These advancements can lead to improved efficiency, safety, and product quality in various industrial applications. As industries evolve, it is essential to adapt to new technologies that streamline operations while addressing existing challenges. Understanding the importance of these innovations is paramount for students, researchers, and professionals in the field.
Automation in Quenching Processes
Automation has revolutionized the way quenching processes are managed. Automated systems can monitor and control various parameters, such as temperature and fluid dynamics, ensuring consistent quality across batches. This decreases human error and allows for scaling up production without compromising the integrity of the products.
Some benefits of automation include:
- Increased throughput: Automated systems can operate continuously, reducing downtime and increasing output.
- Enhanced precision: Sensors can provide real-time data about the quenching process, leading to precise temperature control.
- Reduced labor costs: By minimizing manual intervention, companies can save on labor expenses.
The integration of robots and artificial intelligence in quenching tanks aids in precise manipulation of components during quenching cycles. This technology not only provides speed but also allows for better monitoring of processes, which is vital in environments with stringent quality requirements.
Integration with IoT Technologies
The integration of Internet of Things (IoT) technologies in quenching tanks is another significant advancement. IoT enables devices to communicate and analyze data in real time. This technology facilitates predictive maintenance, allowing for timely interventions that minimize downtime.
Key advantages of IoT integration include:
- Remote monitoring: Operators can oversee processes from different locations, enhancing flexibility in management.
- Data collection: Continuous data logging improves process analysis, helping to identify inefficiencies.
- Enhanced safety: Real-time alerts can warn operators about any irregular conditions before they escalate into serious issues.
IoT-connected devices can also optimize energy consumption in quenching tanks. By adjusting parameters based on actual usage, it's possible to maintain equilibrium and reduce waste.
"The future of quenching technology lies not just in better tanks, but also in how those tanks communicate and work with other systems."
Collectively, these advancements in automation and IoT technologies present a remarkable opportunity for industries reliant on quenching processes. By embracing these changes, companies can position themselves competitively in an increasingly demanding market.
Future Directions
As industries evolve and adapt to changing market demands, quenching tanks are positioned to play a pivotal role in the future of thermal processing. The focus on sustainability and technological integration will define the next steps in quenching tank design and utilization. Simple adjustments in these systems can lead to significant improvements in energy efficiency and environmental impact, making them a focal point for innovators and researchers alike.
Sustainability in Quenching Practices
Sustainability is increasingly becoming a critical consideration across sectors. In quenching practices, this involves the adoption of eco-friendly fluids and processes. Many manufacturers are exploring alternatives to conventional quenching media, such as developing biodegradable fluids or using recycled water. Implementing these strategies can drastically reduce chemical waste and almost eliminate potential hazards associated with traditional quenching methods.
Moreover, enhancing heat recovery in quenching tanks can optimize energy consumption. By integrating heat exchangers, facilities can capture waste heat and reuse it for pre-heating quenching fluids. This approach not only decreases operational costs but also reduces the carbon footprint of manufacturing activities. For companies to remain competitive, sustainability must not only be a regulatory necessity but also a strategic advantage.
"Innovating in sustainability is not just a trend; it is a requirement for the future of thermal processing."
Research Gaps and Opportunities
In the realm of quenching tanks, research gaps present significant opportunities for advancement. One area needing attention is the study of the effects of varying fluid properties on cooling rates. Understanding the relationship between fluid characteristics, such as viscosity and thermal conductivity, and their impact on quenching efficiency can lead to better material outcomes in heat treatment.
Another gap lies in the integration of smart technologies. Although IoT systems are beginning to emerge within the industry, comprehensive studies on their implementation in quenching tanks are scarce. Researching the potential of IoT technologies can uncover new efficiencies that align with Industry 4.0 principles. Implementing smart sensors to monitor temperature and fluid conditions in real-time could provide manufacturers with greater control and improve their products.
Finally, few studies have investigated the economic viability of reducing water usage in quenching processes, particularly in regions where water scarcity poses a significant challenge. Addressing this concern could lead to innovative solutions that mitigate environmental issues while maintaining high productivity levels.
Through targeted research and practical innovation, the future of quenching tanks holds the potential for significant improvements in sustainability and efficiency.