Comprehensive Insights into AB Coating
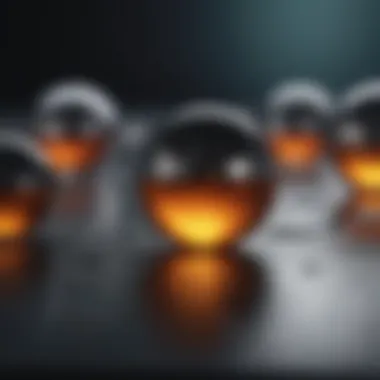
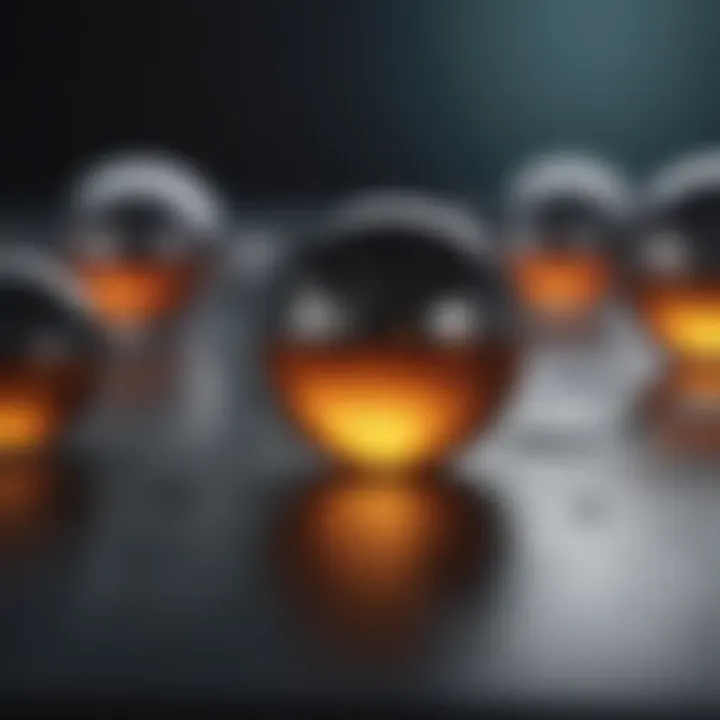
Intro
AB coating represents a significant advancement in material science. This technique is crucial for enhancing material properties across a variety of industries. Understanding this process can help in the development of innovative technologies and applications.
The fundamental principle of AB coating lies in its ability to modify surface characteristics of materials. This modification is instrumental in improving attributes such as durability, corrosion resistance, and adhesion properties.
Through this article, we will explore the intricate chemical and physical processes involved in the AB coating method. Additionally, various applications in scientific fields will be examined. There is a growing interest in the potential future directions that AB coating may take. This analysis will not only bolster existing knowledge but also inspire further research efforts in this field.
Methodology
Overview of research methods used
This section provides an overview of the research methods employed to study AB coating. Both qualitative and quantitative approaches have been used to gather information about the principles and applications of AB coatings.
Data collection techniques
Data for this article was collected through several techniques, including:
- Literature review: An extensive review of existing literature, including academic journals and industry reports, provided a solid foundation of the principles surrounding AB coating.
- Case studies: Key case studies were analyzed to illustrate effective applications of AB coating in various industries.
- Interviews: Discussions with experts in the field contributed insights into ongoing research trends and challenges.
Applications of AB Coating
AB coating finds use in diverse sectors, necessitating a comprehensive understanding of its applications:
- Electronics: Enhanced conductivity and insulation properties are critical in electronic components. AB coating can improve reliability.
- Automotive: Protective coatings are essential for vehicle longevity. AB coatings help resist wear, corrosion, and damage.
- Aerospace: In an environment where factors can vary drastically, AB coating can provide insulation and protection against extreme conditions.
These applications showcase how AB coating technology can enhance performance and durability in products and processes.
Future Directions
Upcoming trends in research
The field of AB coating is advancing rapidly. Several trends are emerging that highlight the future of this technology:
- Nanotechnology: The integration of nanomaterials in AB coating is offering new avenues for enhancing performance.
- Sustainability: Increased focus on environmentally friendly materials and processes is guiding research efforts toward sustainable AB coating solutions.
Areas requiring further investigation
Further investigation is needed in areas such as:
- Long-term stability: Understanding the longevity of coatings in various environments is crucial for application reliability.
- Scalability of production: As interest grows, the feasibility of scaling up production methods needs thorough exploration.
Continued research into AB coating will likely yield new innovations that can be integrated into existing technologies, improving performance and sustainability.
This article aims to provide a thorough understanding of AB coating, emphasizing the principles, applications, and future directions of this essential technology.
Understanding AB Coating
AB coating represents a significant advancement in material science, whose principles and applications resonate across various industries. Understanding this coating method is crucial for both scientific and practical reasons. By delving into its core aspects, one can appreciate how AB coating improves material properties, enhances durability, and enables innovative solutions to complex problems. It bridges the gap between theoretical research and practical applications, hence its rising importance in modern technology.
Defining AB Coating
AB coating, often referred to as atomic layer deposition, is a thin-film deposition technique that allows for the precise control of layer thickness at the atomic level. This method is essential in producing uniform and conformal coatings on substrates with complex geometries. The process fundamentally relies on sequential self-limiting surface reactions. This ensures that each reaction step deposits one atomic monolayer, resulting in high precision and reproducibility in film growth.
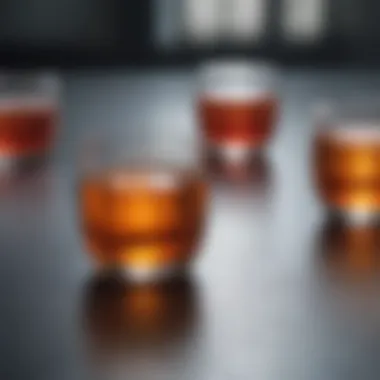
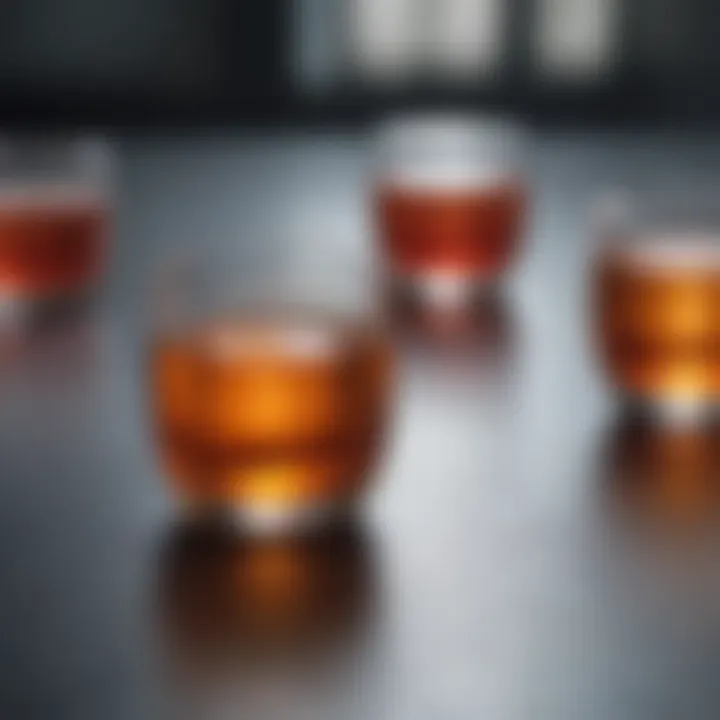
The significance of AB coating extends beyond its technical details. Many industries, including electronics, optics, and biomedical, reap the benefits of its unique properties. Enhanced surface characteristics mean fewer defects and improved performance in applications such as semiconductors, solar cells, and medical implants.
Historical Context and Evolution
The development of AB coating can be traced back to the 1970s, when researchers began exploring thin-film technologies. Its origins are rooted in the need for higher purity materials and precise thickness control. Early applications focused on the aerospace and electronics sectors, where performance and reliability were paramount. Over time, interest in AB coating expanded into various fields including energy, healthcare, and environmental science.
The evolution of AB coating technology has been marked by several key innovations.
- Advances in precursor materials enhanced deposition rates and improved film qualities.
- The introduction of new substrates allowed for wider compatibility across different applications.
- Innovations such as plasma-enhanced atomic layer deposition transformed the capabilities of coating processes.
In summary, understanding AB coating entails recognizing its definition, historical development, and its ongoing impact across diverse fields. This comprehension lays the groundwork for further exploration into its chemical fundamentals, physical processes, and practical applications.
Chemical Fundamentals of AB Coating
The chemical fundamentals of AB coating are crucial for understanding its mechanisms and benefits. This section highlights the core chemical processes at play, which underpin the effectiveness of AB coating in various applications. Understanding these fundamentals is essential for students, researchers, educators, and professionals who seek to innovate or improve existing coating technologies. This knowledge enables the selection of appropriate materials and processes tailored to specific applications, ultimately leading to enhanced material performance.
Key Chemical Reactions
AB coating relies on several key chemical reactions that form the foundation of its application. These reactions often involve polymerization, adhesion mechanisms, and other surface interactions that define the quality of the final coating.
- Polymerization: This is the primary reaction where monomers chemically bond to form polymers. The polymerization process can be thermal, UV-initiated, or chemical initiated depending on the formulation of the coating. The choice of initiation method can vastly affect the properties of the final product, including its durability and adhesion characteristics.
- Cross-linking: Once polymer networks form, additional chemical reactions may occur, leading to cross-linking. This helps to enhance the mechanical strength and thermal stability of the coating, allowing it to withstand environmental stressors.
- Surface interactions: Understanding the interactions between the coating materials and the substrate is essential. These interactions can include hydrogen bonding, van der Waals forces, and electrostatic interactions. High-quality bonding can enhance the lifespan and utility of the coating in practical applications.
"Chemical reactions in coating processes are critical for determining the effectiveness and performance of the final product."
Material Selection for Coating
Selecting the appropriate materials for AB coating is vital for achieving the desired properties and performance. The choice depends on several considerations:
- Compatibility: The materials used in the coating must be compatible with the substrate. This ensures optimal adhesion and performance.
- Chemical Resistance: Depending on the intended application, the selected materials need to withstand specific chemicals. Materials like polytetrafluoroethylene (PTFE) can offer excellent chemical resistance but may require specific processing conditions.
- Mechanical Properties: Strength, elasticity, and flexibility are practical concerns. The balance of these properties should match the intended use of the coated product.
- Environmental Impact: Increasingly, the choice of materials incorporates sustainability factors. Biodegradable or less toxic options are becoming more feasible as technology advances.
Physical Processes in AB Coating
Understanding the physical processes in AB coating is essential for grasping how this technique enhances various material properties. The processes involved in AB coating can significantly affect the resulting film characteristics, including adhesion, thickness, and uniformity. This section will analyze the key coating techniques and methods applied, as well as how to effectively characterize the coated surfaces.
Coating Techniques and Methods
AB coating employs a variety of techniques and methods to achieve desired properties in coated materials. These techniques are critical, as they directly influence the efficiency of the coating application as well as the quality of the final product. Some of the common methods include:
- Dip Coating: In this process, the substrate is submerged in a solution containing the coating material. The substrate is then withdrawn at a controlled speed. This method is simple and effective but requires precise control to avoid dripping.
- Spray Coating: Utilized for larger surfaces, this technique involves spraying a fine mist of the coating solution onto the substrate. It allows for good control over thickness but may require extensive surface preparation.
- Spin Coating: This method employs centrifugal force to spread the coating material uniformly across the substrate. Itโs mainly used for small, flat surfaces and is renowned for producing thin, even films.
- Electrostatic Coating: Here, an electric charge is used to attract the coating particles to the substrate. This technique enhances adhesion and is particularly useful for complex geometries.
Each of these methods has specific advantages and limitations. Selection of the appropriate coating technique must consider factors such as the substrate material, desired film thickness, and the environmental conditions during application.
Characterization of Coated Surfaces
Characterization is a pivotal aspect of the AB coating process, as it determines the quality and functionality of the coating on the substrate. Several techniques exist, each providing insights into different characteristics:
- Surface Roughness Measurement: Tools such as atomic force microscopy (AFM) or profilometers assess the roughness of the coated surface. Surface roughness can influence properties like adhesion and fluid dynamics.
- Thickness Measurement: Techniques like ellipsometry or X-ray reflectivity are employed to measure the film thickness. Understanding the thickness distribution across the substrate is important for optimal performance.
- Chemical Composition Analysis: Methods such as X-ray photoelectron spectroscopy (XPS) can analyze the surface chemistry of the coating. This aids in understanding how the coating interacts with the environment and the substrate.
- Adhesion Tests: The durability of the coating often depends on its adhesion to the substrate. Techniques like tape tests or scratch tests evaluate the bonding strength.
These characterization methods provide crucial data that inform both the production process and potential applications. A thorough understanding of these processes not only helps in achieving high-quality coatings but also in advancing research in AB coating technology.
Applications of AB Coating
AB coating has emerged as a versatile technology with numerous real-world applications. This section explores its significance across various sectors, including industry, healthcare, and environmental sciences. The specific benefits offered by AB coating include enhanced material properties, improved durability, and tailored surface characteristics. Understanding these applications helps to underscore the vital role AB coating plays in advancing technologies.
Industrial Applications
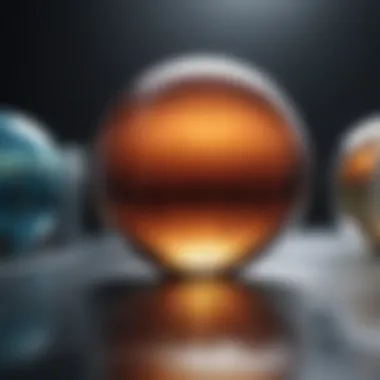
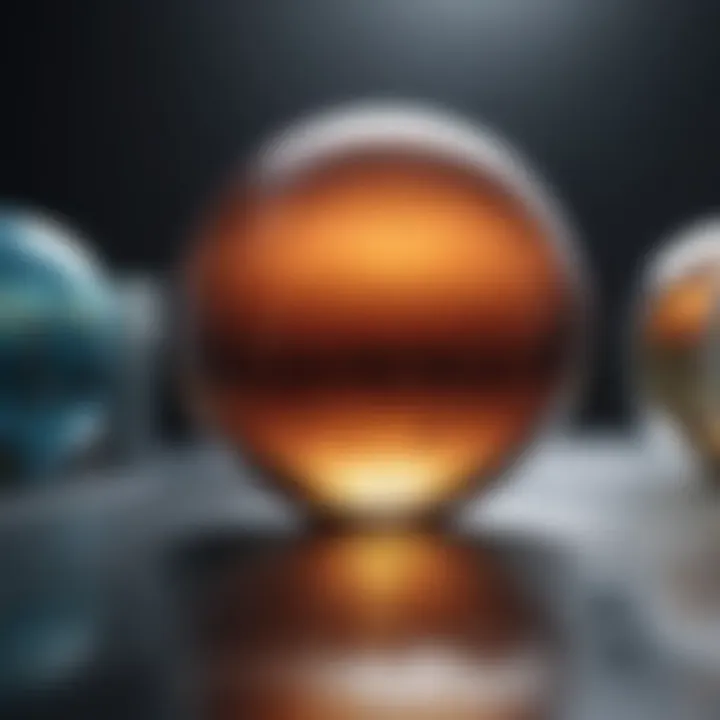
In the industrial landscape, AB coating is integral for enhancing the performance of materials. This method improves corrosion resistance, hardness, and aesthetic appeal of surfaces. Applications range widely from automotive components to electronic devices.
- Automotive: Components such as engine parts and body panels often undergo AB coating to resist wear and extend lifespan. The robustness of the coating ensures higher performance, which is essential for vehicles in harsh environments.
- Electronics: In this field, AB coating is utilized for its excellent dielectric properties. This is especially important for printed circuit boards where insulation from elements or other conductive pathways is necessary.
Overall, the industrial applications of AB coating exhibit how crucial it is for meeting standards of safety, efficiency, and durability.
Medical and Healthcare Uses
In medical settings, the applications of AB coating have profound impacts. The coatings can provide anti-bacterial properties, which minimizes infections during surgical procedures and enhances the safety of medical devices. Additionally, AB coating is essential in producing biocompatible materials that are safe for human contact.
- Implants: Coated implants enhance integration with bone and tissue, reducing the chances of rejection. This increases the success rate of procedures like hip replacements.
- Medical Devices: Devices such as stents and catheters benefit from AB coating, offering smoother surfaces that reduce friction. This is vital for ensuring safer procedures and improved patient outcomes.
The medical sector showcases AB coating's capacity to revolutionize patient care by significantly improving device functionality.
Environmental Applications
The contributions of AB coating to environmental fields are noteworthy. These coatings can be designed to be eco-friendly, promoting sustainability. They are increasingly employed to improve energy efficiency and optimize resource use.
- Solar Panels: AB coating enhances the efficiency of solar panels by increasing light absorption. This can lead to more sustainable energy practices as the demand for renewable energy sources rises.
- Pollution Control: In applications targeting air or water purification, AB coatings can be used as part of filters or traps. They can enhance filtration processes, making water treatment plants more efficient.
In summary, the environmental implications of AB coating highlight its potential to support sustainability efforts. The versatility of AB coating illustrates its importance across multiple sectors, demonstrating its role in enhancing material performance and contributing to modern solutions.
Advantages and Limitations of AB Coating
The advantages and limitations of AB coating are pivotal in understanding its practical applications and future directions. Insights into these elements help researchers and professionals make informed decisions regarding the adoption or development of AB coating technologies. This section will dissect the strengths and challenges of AB coating, providing a balanced perspective on its usage and potential.
Strengths of AB Coating
AB coating offers numerous strengths that make it an appealing choice in various fields. Some key strengths include:
- Enhanced Material Properties: AB coating improves durability, scratch resistance, and chemical resistance of surfaces. This enhancement increases the lifespan of products and reduces maintenance costs.
- Versatility: The application of AB coating spans a wide range of industries. From automotive to electronics, it caters to diverse needs, offering tailored solutions specific to each sector.
- Advanced Performance: The coatings have superior performance characteristics compared to traditional coatings. For instance, they provide better adhesion, flexibility, and thickness uniformity, which can significantly affect the overall efficacy of the product.
- Eco-friendliness: Many AB coatings are formulated to be environmentally friendly, reducing VOC emissions and enhancing sustainability. This attribute aligns well with modern industry trends toward greener practices.
"AB coating stands out due to its capability to significantly elevate material performance while minimizing environmental impact."
Challenges and Limitations
Despite its advantages, several challenges and limitations must be considered when deploying AB coating technologies. Notable concerns include:
- Application Complexity: The application process can be complex and requires specialized equipment and skilled technicians. This complexity can lead to increased operational costs for some companies.
- Cost Factors: Although the long-term benefits can outweigh initial investments, the cost of high-quality AB coatings can be relatively high. Some organizations may find it challenging to justify the higher prices compared to conventional options.
- Adhesion Issues: Proper surface preparation is crucial for ensuring strong adhesion of the coating. Any inconsistency in surface treatment can lead to failures, which may undermine the benefits of AB coating.
- Limited Knowledge Base: As AB coating is a continually evolving field, there may be limited knowledge and research in certain applications. This could restrict widespread adoption in some sectors.
Future Directions in AB Coating Research
The future directions in AB coating research represent a crucial aspect of this field, signifying the ongoing advancements and potential improvements in coating technologies. One of the most significant elements to consider is the pursuit of innovative materials. Researchers are constantly looking for alternative substances that can enhance the properties of coatings, making them more effective in various applications. As industries demand more efficient and durable coatings, the investigation of novel polymers, nanomaterials, and hybrid coatings will play a vital role in determining the success of future projects.
The benefits of such innovative approaches are manifold. Not only can new materials offer improved adhesion and resistance to wear, but they can also lead to coatings that require less material, promoting cost efficiency and environmental sustainability. Furthermore, advancements in the understanding of molecular interactions may lead to coatings with tunable properties, allowing for customization according to specific needs. By exploring the latest innovations, the field can refine existing methodologies and push the boundaries of what is achievable.
Considerations about these future directions include the need for rigorous testing and validation of any new material before it can be widely adopted. Ensuring compatibility with existing processes is also vital for industrial applications. By addressing these concerns, researchers can pave the way for safe and effective implementation of new AB coatings into various sectors.
Innovative Materials and Coatings
The exploration of innovative materials is at the forefront of AB coating research. Incorporating advanced materials can significantly alter the performance characteristics of coatings. For example, graphene and carbon nanotubes have gained attention due to their remarkable mechanical and thermal properties. These materials can lead to coatings that not only offer superior protection but also enhance the functionality of the coated surfaces. Researchers are examining how these materials can be integrated into AB coating processes to achieve enhanced performance.
In addition to graphene, biomimetic materials derived from nature are gaining traction. These materials often exhibit unique properties that can be adapted for various applications. The use of smart coatings that respond to environmental stimuli is another exciting area of research. Such coatings could change color, composition, or properties based on conditions, providing alerts or enhancing their protective functions.
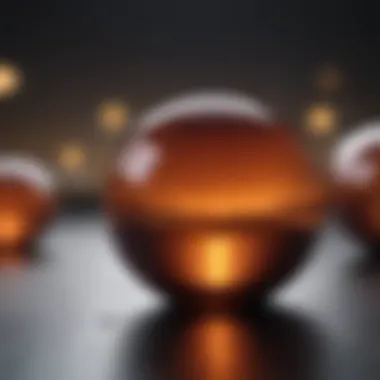
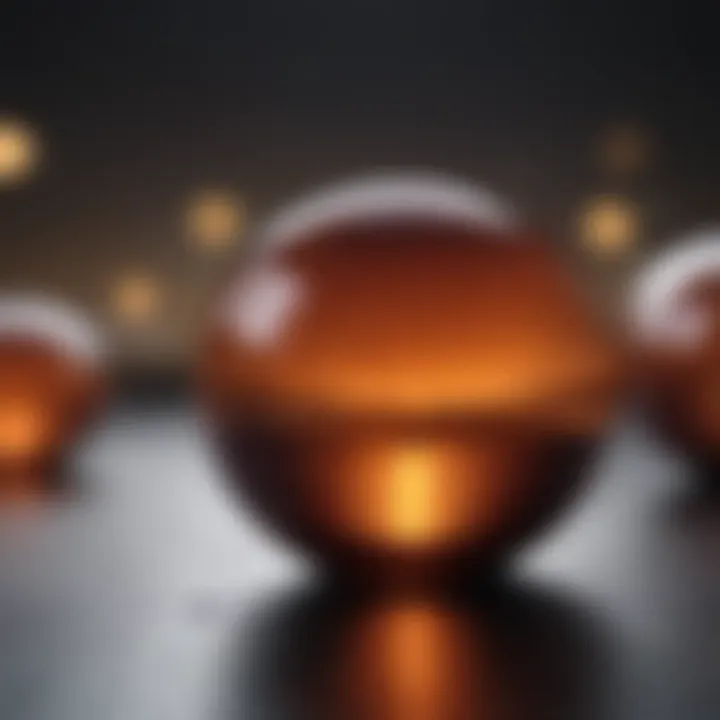
Research institutions and industries alike are collaborating to drive the development of these innovative materials. By focusing on practicality and scalability, it is possible to translate laboratory results into commercial products that offer significant advantages over traditional options.
Sustainability in Coating Processes
Sustainability in coating processes has emerged as an essential consideration in the future trajectories of AB coating research. The coating industry is scrutinizing its environmental impact, particularly concerning resource use and waste generation. One approach is to develop coatings that use less harmful chemicals and promote safe disposal methods. Innovations such as water-based coatings and those that utilize bio-based materials are paving the way for a more sustainable future. These alternatives reduce volatile organic compounds (VOCs) and lessen the ecological footprint of production.
Another significant element of this sustainable focus is the recycling of materials. Research into reclaiming coating materials from end-of-life products could mitigate waste and enhance resource efficiency. The idea of a circular economy in the coatings industry is becoming a reality, with efforts directed towards creating coatings that can be easily removed and recycled without compromising their properties.
Additionally, the energy consumption associated with the application of coatings is under review. Developing low-temperature curing processes and high-efficiency application methods can greatly reduce energy usage. These improvements are crucial in addressing global energy concerns and aligning with broader sustainability goals.
"The integration of sustainability into AB coating processes is not just a trend but a necessity for future advancements. Efficiency, environmental consideration, and innovation must work side by side to ensure a viable future for coatings."
In summary, the future directions in AB coating research highlight the importance of innovative materials and sustainability in driving the field forward. By focusing on these elements, researchers can contribute to more effective, eco-friendly coatings that meet the evolving demands of industries globally.
Comparative Analysis with Other Coating Methods
The role of comparative analysis in the discussion of AB coating holds significant importance. Such an analysis highlights how AB coating functions alongside more conventional methods. It provides insights into the strengths, weaknesses, and optimal applications of each technique. Understanding these differences is vital for students, researchers, and professionals as they choose the most suitable coating method for specific purposes.
AB Coating versus Traditional Coating Techniques
AB coating differentiates itself markedly from traditional coating techniques. Traditional methods often include paint, varnishes, and powder coatings. These methods have been prevalent for years and provide various benefits, such as cost-effectiveness and ease of application. However, they tend to lack in precision and the ability to adhere to intricate geometries.
AB coating, on the other hand, offers superior control over thickness and uniformity. The precision in AB coating allows for effective customization of surface properties. This method excels in producing coatings that are not only thinner but also more effective in terms of function. For example, coatings applied via the AB method often show enhanced resistance to environmental stressors, which is crucial in industrial applications.
The choice between AB coating and traditional methods can depend on several factors:
- Application Surface: Areas with complex shapes may benefit more from AB coating.
- Cost Restrictions: Traditional methods might be more budget-friendly in some cases.
- Performance Requirements: AB coating usually provides superior performance in terms of durability.
The effectiveness of AB coating becomes apparent in areas such as automotive and aerospace industries where performance is critical.
Performance Metrics and Data
To effectively compare coatings, analyzing performance metrics is essential. Various criteria are used to measure the efficacy of both AB coating and traditional methods.
In the realm of coatings, key performance metrics often include:
- Adhesion Strength: AB coating frequently exhibits higher adhesion levels, improving longevity and performance on challenging surfaces.
- Thickness Uniformity: AB processes can maintain consistent thickness on surfaces, a feat more challenging with traditional techniques.
- Durability: Resistance to wear and environmental conditions tends to be superior in AB coatings. Studies show that these coatings can last significantly longer under extreme conditions compared to traditional options.
- Curing Times: AB coating processes often offer faster curing times, leading to increased productivity in industrial settings.
Research indicates that coatings using AB techniques demonstrate a decrease in failure rates by up to 30% in comparison to traditional methods.
The compiled data allows manufacturers and researchers to make informed decisions. Using a systematic approach toward performance metrics leads to selecting the appropriate method that aligns with project needs and long-term viability.
Epilogue and Implications
The examination of AB coating has revealed its profound significance in various industries. Understanding this coating method is pivotal for advancing material science and engineering applications. The key elements to consider include the techniques utilized, the diverse applications, and the potential for innovation in coating materials and processes.
Summary of Key Insights
AB coating stands out due to its unique chemical and physical processes. Key insights derived from this article include:
- Versatility: AB coating can be tailored for numerous applications, spanning from industrial uses to healthcare.
- Materials Improvement: The capability to enhance material properties, such as corrosion resistance and durability, is a compelling advantage.
- Innovative Potential: As research progresses, there are opportunities for developing new materials, leading to improved performance and sustainability in coating practices.
AB coating's role in modern technology places it at the forefront of coatings research. Thus, ongoing study into its methods and impacts will benefit future applications.
Impact on Future Research
The implications of the insights on AB coating are substantial for future research endeavors. It paves the way for:
- New Materials Exploration: Innovations in materials will likely emerge as researchers explore different substrates and coating compositions. This could introduce performance enhancements that current materials cannot achieve.
- Eco-Friendly Solutions: With increasing emphasis on sustainability, future studies might focus on environmentally friendly coating processes that reduce toxic byproducts.
- Interdisciplinary Approaches: Researchers from various disciplines may consider AB coating for novel applications, integrating insights from biology, chemistry, and engineering to develop unique solutions.
In sum, the understanding and development of AB coating methods have critical implications for both academia and industry. By investing in this area, stakeholders may unlock new technologies and elevate the functional performance of coated materials.