Exploring Low Pressure Chemical Vapor Deposition
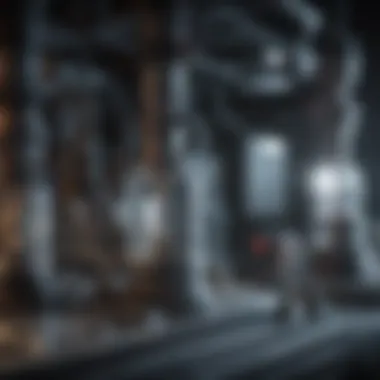
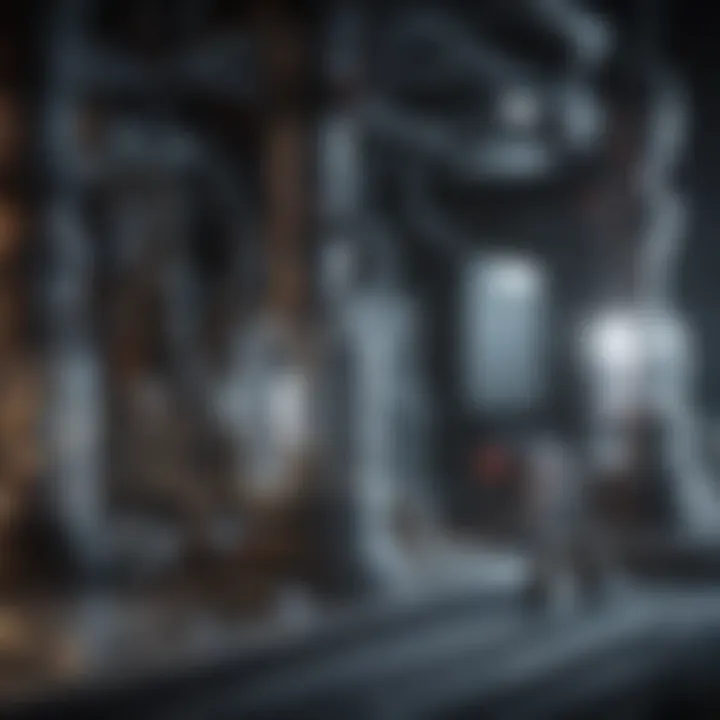
Intro
Low Pressure Chemical Vapor Deposition (LPCVD) is an essential method used in many industries. Its importance is particularly highlighted in semiconductor manufacturing and materials science. This section of the article aims to define LPCVD and illustrate its significance.
LPCVD operates under vacuum conditions, which allows for the deposition of thin films. This process is beneficial because it reduces the probability of unwanted reactions. The key principle is to transform gaseous precursors into solid films at low pressure. Such control over the environment results in high uniformity and purity of thin films.
Furthermore, LPCVD techniques have evolved. Recent advancements have improved efficiency and quality. They allow for better control over film thickness and composition. Understanding these techniques is crucial for researchers and professionals aiming to innovate in material development.
At its core, LPCVD fulfills a critical role in the electronics industry, paving the way for more efficient chip design and production. It is the go-to method for applications that require precision and reliability.
Methodology
The methodology for studying LPCVD techniques encompasses various research methods. Several approaches are utilized to gain a better understanding of their principles and effectiveness.
Overview of research methods used
Research often combines experimental and theoretical methods to offer a comprehensive view of LPCVD processes. Experimentation may involve actual LPCVD setups to analyze different variables, such as gas flow rates and temperatures. Many studies also utilize mathematical modeling to simulate the deposition process under different conditions. This dual approach provides insights not only into practical applications but also into the underlying physics.
Data collection techniques
Data collection techniques play a vital role in research. These may include:
- Spectroscopic methods: Used to analyze the material's properties after deposition.
- Microscopy: Techniques like Scanning Electron Microscopy (SEM) allow for viewing the thin films at high resolutions.
- Surface Profilometry: Measures film thickness and uniformity.
Combining these techniques leads to a deeper understanding of LPCVD materials and their respective properties.
Future Directions
As technologies advance, LPCVD remains a pivotal area of study. Future directions in this field suggest promising trends worth investigating.
Upcoming trends in research
- Neue precursors: Exploring alternative gaseous precursors that can enhance film properties.
- Environmentally friendly processes: Researching methods that reduce harmful emissions.
- Integration with other techniques: Combining LPCVD with techniques like Atomic Layer Deposition (ALD) for enhanced functionality.
Areas requiring further investigation
Today’s challenges include:
- Improving scalability for industrial applications.
- Understanding the long-term stability of coated films.
- Enhancing the deposition rates without compromising quality.
In summary, Low Pressure Chemical Vapor Deposition is more than just a deposition method; it is integral to many industry advancements. Its future looks bright, with ongoing research aimed at refining techniques and expanding applications.
Prolusion to Low Pressure Chemical Vapor Deposition
Low Pressure Chemical Vapor Deposition (LPCVD) plays a crucial role in the domains of semiconductor manufacturing and materials science. This technique enables the formation of thin films, vital for the production of various electronic devices and components. The importance of LPCVD arises not just from its functional capabilities, but also from the increasing demand for precision and efficiency in production processes. As devices become smaller and more complex, the need for high-quality deposits is paramount.
Historical Context
The roots of LPCVD trace back to earlier chemical vapor deposition (CVD) processes developed in the mid-20th century. Initial explorations focused on understanding how gases could be manipulated to create solid materials on substrate surfaces. The LPCVD process emerged as researchers sought to enhance uniformity and reduce deposition challenges, particularly in fabricating semiconductor devices. Significant advancements during the 1970s and 1980s positioned LPCVD as a reliable technique for producing thin films. As technology progressed, it adapted to meet the evolving standards of the semiconductor industry.
Definition and Overview
LPCVD is a chemical deposition method that occurs at lower pressures than traditional CVD processes. It typically operates within a vacuum environment, which promotes better control over film properties and uniform thickness. The fundamental principle of LPCVD is the chemical reaction between gaseous precursors at the substrate's surface, resulting in a solid film. This method is especially beneficial for applications requiring high purity and precise layer control. Key gases involved in the process may include silane for silicon deposition and other precursors dependent on desired material characteristics. The ability to tailor films for specific functionalities sets LPCVD apart as a vital technique in contemporary manufacturing.
Fundamental Principles of LPCVD
Understanding the fundamental principles of Low Pressure Chemical Vapor Deposition (LPCVD) is essential, as they shape the performance and effectiveness of the technology. This knowledge is crucial for students, researchers, and professionals involved in semiconductor manufacturing and material sciences. The LPCVD process primarily relies on gas-phase chemical reactions, controlled operational parameters, and the physics of gas flow. These elements work together to facilitate uniform and high-quality film deposition, highlighting the method’s advantages.
Chemical Reactions in LPCVD
The heart of LPCVD lies in its chemical reactions. LPCVD utilizes gaseous precursors which, under heat, undergo reactions leading to thin film formation on substrate surfaces. Precursors can vary in composition and reactivity, significantly impacting film characteristics. A common precursor for silicon deposition is silane (SiH₄). When heated in the presence of appropriate conditions, it decomposes to deposit silicon onto the substrate.
The reactions involved may take several pathways:
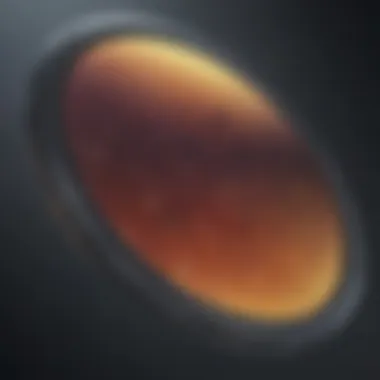
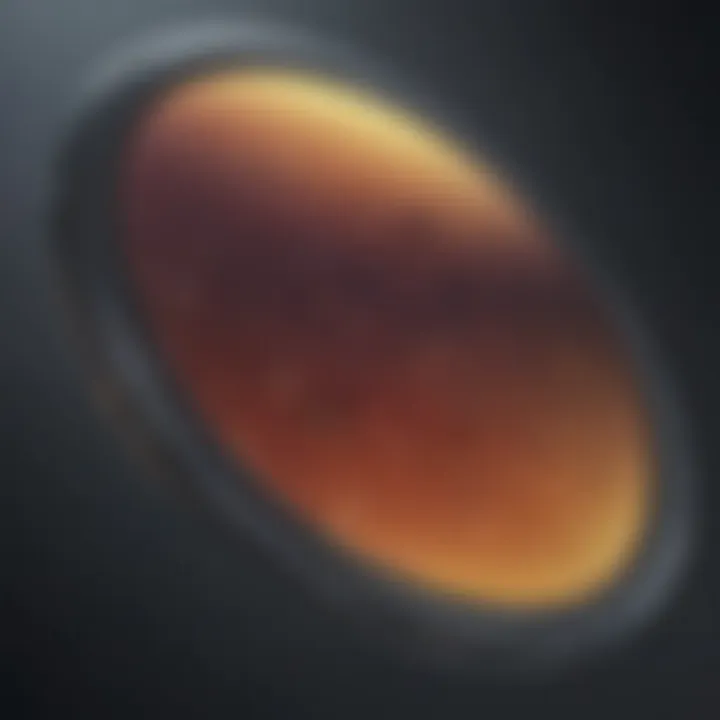
- Decomposition: The breakdown of a gaseous compound into simpler molecules, which deposit as solid materials.
- Surface Reactions: The reaction may occur on the substrate surface, where the solid phase forms directly.
- Volatile Byproducts: Some reactions produce gaseous byproducts that must be effectively managed to avoid contamination.
The efficiency of these chemical reactions determines the overall quality of the deposited films, influencing properties such as thickness, uniformity, and purity. Proper understanding and control of these interactions can optimize the deposition process.
Pressure and Temperature Control
Pressure and temperature control are critical variables in the LPCVD process. Operating at low pressures reduces unwanted gas-phase reactions, leading to purer films. The typical pressure range for LPCVD is between 0.1 to 1 Torr. This reduction in pressure enhances the mean free path of the gas molecules, promoting better gas transport to the substrate.
Temperature, on the other hand, directly affects the kinetics of the chemistry involved. Elevated temperatures increase the reactivity of precursors, leading to faster deposition rates but may also induce unwanted side reactions. Therefore, a balance must be struck. For instance:
- Low Temperature: Reduces unwanted reactions but may result in slower deposition rates.
- High Temperature: Facilitates faster processing but risks film quality degradation through unwanted chemical reactions.
Maintaining optimal conditions thus requires sophisticated monitoring and control systems to ensure that the equipment can adapt to variations, achieving high precision in temperature and pressure settings.
Gas Flow Dynamics
The dynamics of gas flow in the LPCVD reactor significantly influence the uniformity and properties of the deposited films. Proper gas flow management ensures that precursors reach the substrate evenly, preventing areas of rich or poor deposition.
Two primary aspects govern gas flow:
- Gas Distribution: Ideally, the design of the LPCVD reactor facilitates even distribution of precursor gases across the substrate. This is often done using gas inlets and distributors that are optimally positioned to enhance uniform flow.
- Exhaust Management: An effective exhaust system is essential to remove byproducts and maintain the purity of the deposited materials. It is vital that the exhaust does not create back pressure, which can adversely affect the deposition process.
Equipment Used in LPCVD
Low Pressure Chemical Vapor Deposition (LPCVD) relies heavily on specialized equipment that is critical to its operational effectiveness. The machinery used not only affects the quality of the films deposited, but also influences the overall efficiency of the manufacturing process. Understanding the equipment utilized in LPCVD provides insights into the mechanisms that drive this innovative technique.
Reactor Design and Functionality
The reactor in LPCVD serves as the heart of the process. It is designed to create a controlled environment where chemical reactions can occur efficiently. Primarily, LPCVD reactors are categorized into two types: vertical and horizontal. The vertical configuration often allows for better space utilization, while the horizontal setup is popular for uniform film deposition across large substrates.
The functionality of these reactors must maintain a specific low pressure, which is essential to achieve high deposition rates and quality films. This is conducted by utilizing vacuum systems to evacuate the chamber, thus creating the required low-pressure environment.
A critical design aspect refers to the heating mechanisms in the reactor. Most systems employ radiant heating or hot-wall configurations, where substrates are kept at elevated temperatures, enabling chemical reactions to proceed effectively. The choice of reactor design can substantially affect the deposition quality.
Material Compatibility
For LPCVD to be effective, material compatibility is crucial. Both the reactor materials and the substrates must withstand various chemicals used during the deposition process. Common materials used in the construction of reaction chambers include stainless steel and quartz. These materials are resistant to the corrosive nature of certain chemical precursors, ensuring durability and a contaminant-free environment.
Additionally, the substrates involved range from silicon wafers to other semiconductors. The choice of substrate greatly impacts the final material properties, such as conductivity and optical characteristics. Thus, careful consideration is necessary to select both reactor materials and substrates that complement each other.
Monitoring and Control Systems
An integral part of LPCVD operations is the monitoring and control systems. These systems are responsible for maintaining the desired process parameters, such as temperature, pressure, and gas flow rates. Advanced sensors and control mechanisms enable real-time adjustments to these variables, ensuring consistent and repeatable results.
Control systems often utilize programmable logic controllers (PLCs) and advanced software to track process conditions. This level of oversight allows operators to identify and rectify any deviations that could compromise film quality.
Moreover, the incorporation of data logging features aids in process optimization. Long-term tracking can assist in identifying trends, leading to improved formulations and enhanced production techniques.
"The efficiency and reliability of LPCVD is significantly influenced by the equipment used, making it essential to understand these elements."
In summary, the equipment used in Low Pressure Chemical Vapor Deposition encompasses a range of components that must all work together harmoniously. The reactor design, material compatibility, and advanced monitoring systems are vital for ensuring quality and efficiency in film production. Understanding these elements helps researchers, educators, and industry professionals alike appreciate the complexities involved in LPCVD.
Advantages of Low Pressure Chemical Vapor Deposition
Low Pressure Chemical Vapor Deposition (LPCVD) is a crucial technique in various industries. The advantages it offers are foundational to its adoption in semiconductor manufacturing, optoelectronics, and even solar cell production. Understanding these benefits helps clarify why LPCVD is preferred over other deposition methods.
Uniform Film Thickness
One significant advantage of LPCVD lies in its ability to produce uniform thin films across large surfaces. This uniformity is vital for semiconductor devices, which require consistent electrical properties throughout their structures. Achieving uniform thickness minimizes performance variations and improves overall product reliability.
The uniformity is attributed to the controlled environment in which the deposition occurs, allowing gas phase reactions to proceed in a manner that deposits material evenly. LPCVD enables precise control over both the chemical processes and the reaction parameters. This results in fewer defects and non-uniformities, essential for high-performance applications.
Enhanced Material Quality
Material quality is another essential factor where LPCVD excels. The low-pressure environment reduces unwanted secondary reactions that might degrade the deposited materials. As a result, the films produced exhibit superior purity and structural integrity.
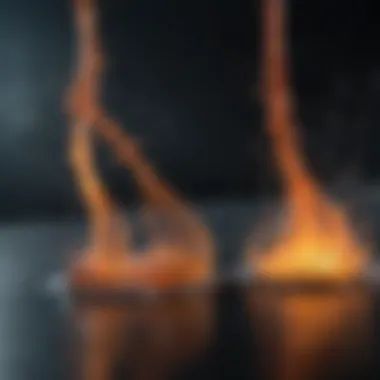
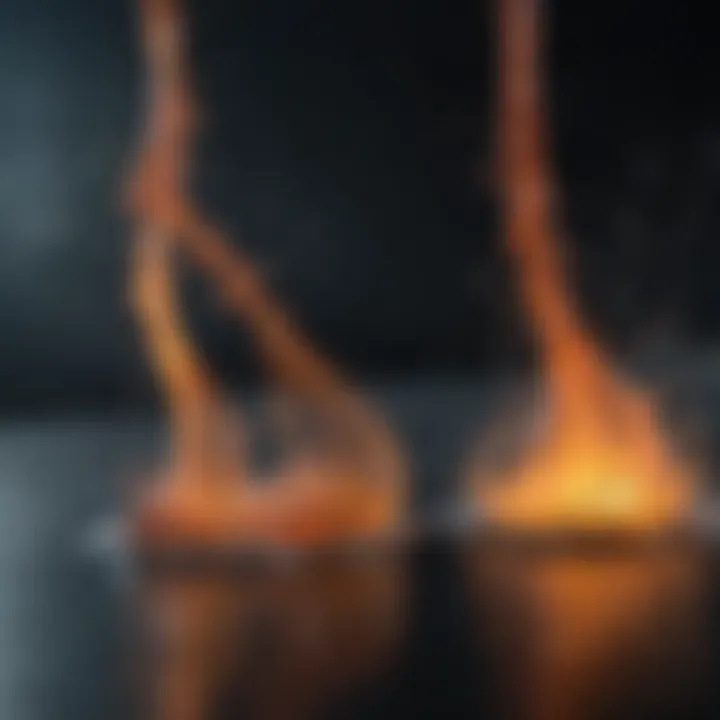
Furthermore, LPCVD processes often involve the use of high-purity precursors. This ensures that additional impurities do not integrate into the final thin film. The enhanced quality of the material also leads to better electrical and mechanical properties, which are necessary for applications like optoelectronic devices and advanced semiconductor components.
Scalability for Industrial Applications
LPCVD also stands out due to its scalability. This method can be adjusted to accommodate various production scales, from laboratory research to full-scale manufacturing. The versatility of LPCVD systems allows industries to maintain efficiency without sacrificing quality.
As manufacturers approach higher production demands, LPCVD can easily adapt. This scalability makes it an attractive option for companies looking to expand their production without needing significant alterations to their existing systems.
The ability to maintain high material quality while ensuring uniform film thickness is a key reason why many industries choose LPCVD for their deposition needs.
In summary, the advantages offered by LPCVD are multifaceted. Uniform film thickness, enhanced material quality, and scalability for industrial applications make LPCVD a pivotal technology in modern manufacturing processes.
Applications of LPCVD
Low Pressure Chemical Vapor Deposition (LPCVD) has established itself as a crucial technique across various industries. Its ability to create high-quality thin films makes it widely used in semiconductor manufacturing and materials science. The relevance of LPCVD extends beyond its basic functions; it contributes significantly to advancements in technology and materials research. This section will examine some specific applications in detail, providing insights into how LPCVD contributes to these fields.
Semiconductor Manufacturing
In the semiconductor industry, LPCVD plays a vital role in the fabrication of integrated circuits. This method is known for depositing uniform films of materials like silicon dioxide and silicon nitride, which are essential for fabricating various components. The process facilitates the creation of precise and repeatable layers, improving the reliability and performance of semiconductor devices.
Factors such as low temperature processing help minimize thermal stress on delicate substrates, enhancing yield rates in manufacturing. Moreover, the flexibility of LPCVD allows for scalable production, making it suitable for both research and mass production scenarios.
Optoelectronic Devices
LPCVD is equally applicable in the production of optoelectronic devices. These devices rely on the precise deposition of materials to control light and electronic signals. For instance, LPCVD can create thin films for light-emitting diodes (LEDs) and lasers. This approach ensures optimal thinness and quality of layers, crucial for device efficiency.
The ability to tailor the film properties during deposition enhances the performance of such devices. In turn, improved performance translates directly into better energy efficiency and functionality, which are critical in modern electronics.
Solar Cells Production
The solar energy sector leverages LPCVD for manufacturing thin-film solar cells. Here, the technique optimizes the deposition of materials like amorphous silicon, significantly contributing to the efficiency of solar power conversion. LPCVD allows for the deposition of layers that maximize light absorption while minimizing defects—parameters critically linked to energy production.
Additionally, the cost-effectiveness of LPCVD supports large-scale production initiatives. As global energy demands rise, innovations in solar cell technology through LPCVD could play a pivotal role in sustainable energy solutions.
Coatings for Industrial Tools
LPCVD also finds significant application in the coatings of industrial tools. The method is used to produce hard, durable coatings that enhance the tools' longevity and performance. Materials like titanium nitride are commonly deposited via LPCVD to improve the wear resistance of cutting tools.
This application reflects the versatility of LPCVD, catering to both specialized and general-use tools. By extending the lifecycle of industrial tools, LPCVD contributes to reduction of costs and increase in productivity within various manufacturing environments.
Challenges and Limitations of LPCVD
The adoption of Low Pressure Chemical Vapor Deposition (LPCVD) techniques in various sectors is significant. However, it is essential to understand the challenges and limitations involved in this method. These issues can affect both the operational efficacy and the overall quality of the final products. By addressing these elements, one can gain insights into the practical constraints that researchers and engineers often encounter.
Cost Implications
The economic considerations associated with LPCVD cannot be overlooked. The initial setup cost for LPCVD systems tends to be high. Purchasing specialized reactors and maintaining them can require substantial investment. Moreover, the uptick in materials costs for the deposition processes further compounds these financial implications.
Operating expenses also play a role. The need for high-purity gases and advanced control systems can elevate ongoing costs. There are indirect expenses as well, including those related to training personnel to operate complex LPCVD equipment effectively. These factors may deter some organizations from fully embracing LPCVD techniques, particularly smaller enterprises with limited budgets.
Material Encapsulation Issues
While LPCVD is notable for its ability to create high-quality films, there are challenges related to material encapsulation. The nature of LPCVD processes often leads to difficulties in achieving consistent encapsulation across various substrates. This can limit the applicability of LPCVD in certain scenarios, particularly where uniformity in coating is essential. Some materials may not bond effectively, creating weak points within the layers.
In applications where adhesion is critical, these encapsulation challenges can lead to failures or reduced performance. Careful selection of materials and thorough understanding of the substrate properties become paramount to mitigate these issues.
Deposition Rate Variability
Another key challenge in LPCVD is the variability in deposition rates. The efficiency of LPCVD can be hindered by fluctuations in environmental factors such as pressure and temperature. Inconsistent gas flow dynamics can also result in variations in the rate of film deposition. This variability can lead to uneven film characteristics, which might not meet the stringent requirements of high-precision applications.
To optimize deposition rates, careful monitoring and control systems must be implemented. Failure to ensure consistent rates can not only affect product quality but also complicate the scalability of LPCVD processes for larger industrial operations. As such, addressing this variability is critical for optimal LPCVD performance.
Emerging Trends in LPCVD Research
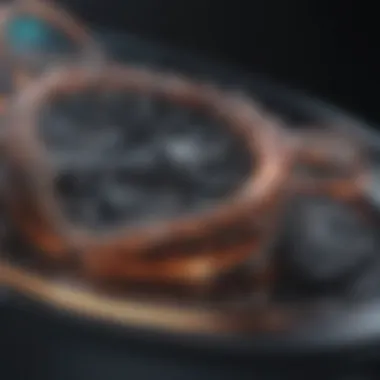
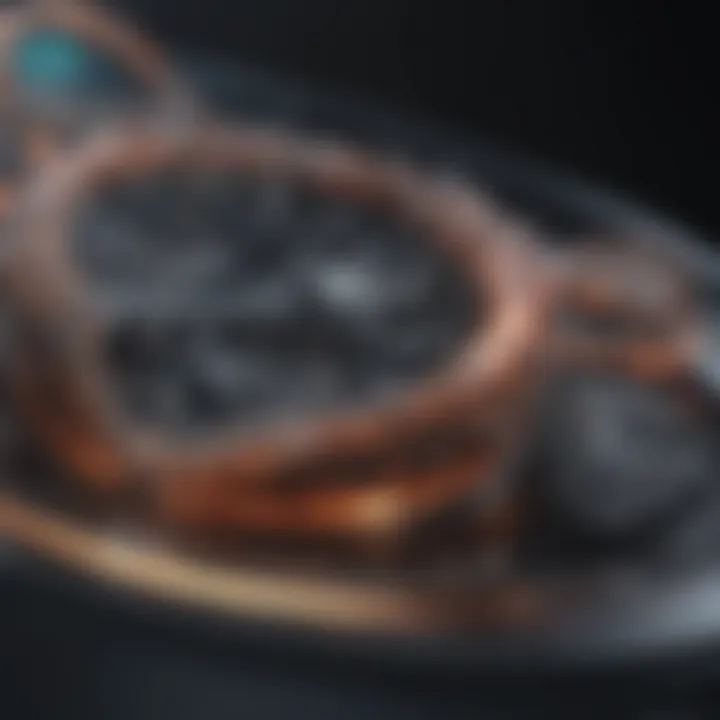
Emerging trends in Low Pressure Chemical Vapor Deposition (LPCVD) research reflect the ongoing advancements required to keep pace with the demands of modern technology. As industries such as semiconductor fabrication and materials science evolve, the integration of innovative methodologies and materials becomes increasingly important. This section discusses three pivotal trends: the integration with nanotechnology, the development of new precursors, and automation coupled with process optimization. Each trend not only enhances the capabilities of LPCVD but also addresses specific challenges faced by researchers and engineers in the field.
Integration with Nanotechnology
The integration of LPCVD with nanotechnology presents exciting opportunities for material innovation. Nanotechnology allows for the manipulation of materials at the atomic level, creating unique properties that often differ from their bulk counterparts. This integration enables the fabrication of thin films with enhanced electrical, thermal, and optical characteristics. Researchers are exploring how LPCVD can deposit nanoscale coatings that significantly improve the performance of devices, particularly in the semiconductor industry.
Utilizing LPCVD in conjunction with nanotechnology involves precision in controlling both the chemical processes and the deposition environment. This control leads to the development of ultra-thin films and precise layer structures. The research in this area is also concerned with scalability, ensuring that these advanced materials can be produced in a cost-effective manner for industrial applications.
"Nanotechnology in LPCVD is expanding the horizons of what is possible in material science, making previously unimaginable innovations a reality."
Development of New Precursors
The evolution of new precursors for LPCVD processes is critical. Traditional precursors may encounter limitations in terms of efficiency, safety, and environmental impact. Therefore, researchers are actively investigating alternatives that can improve the efficiency and versatility of the LPCVD process. For example, more efficient precursors can lead to reduced byproduct formation, which in turn minimizes the need for complex post-deposition cleanup procedures.
Moreover, the selection of precursors affects the quality and properties of the films produced. Improved precursors can facilitate better control over film composition and, thus, influence mechanical and electronic properties. For instance, the development of organo-metallic compounds has opened up new possibilities for depositing high-quality semiconductor layers with specific characteristics tailored to different applications.
Automation and Process Optimization
Automation and process optimization are becoming essential components of modern LPCVD systems. As the demand for higher efficiency and reproducibility grows, automated systems are addressing previous inconsistencies in the deposition process. The goal is to minimize human error, enhance precision, and streamline operations.
With advancements in machine learning and artificial intelligence, LPCVD systems can now analyze data in real-time. This capacity allows for dynamic adjustments to be made to the deposition conditions, thereby optimizing the process continually. For instance, the algorithms can predict potential issues and make adjustments that enhance film quality and deposition rates. Automation also enables a more systematic approach to experimental setup, thereby speeding up the research and development cycle.
In summary, the emerging trends in LPCVD research are pivotal for advancing the field. Integrating nanotechnology, developing new precursors, and embracing automation and process optimization collectively push the boundaries of what is achievable with this versatile deposition technique. These trends are not merely enhancements but essential evolutions reflecting the needs of contemporary scientific and industrial challenges.
Comparative Analysis with Other Deposition Techniques
When examining Low Pressure Chemical Vapor Deposition (LPCVD), it is essential to contrast it with other deposition techniques in use today. This evaluation reveals not only the strengths and weaknesses of LPCVD but also highlights its unique advantages in specific applications. Understanding these differences helps to inform choices in material fabrication, especially in industries like semiconductors and optics.
LPCVD vs. APCVD
Atmospheric Pressure Chemical Vapor Deposition (APCVD) also serves as a technique for producing thin films, but it operates at much higher pressure compared to LPCVD. The distinction in pressure levels significantly influences the deposition process and the characteristics of the films produced.
One primary benefit of LPCVD over APCVD is its ability to create higher quality films. LPCVD generally facilitates better uniformity and control over the film thickness due to the lower pressure environment. This results in fewer defects and improved overall material properties. Additionally, LPCVD processes tend to have better step coverage, which is crucial for complex structures, such as those found in semiconductor devices.
In terms of operational cost, LPCVD may seem more beneficial in specific applications despite its higher initial equipment cost. Its energy consumption can be lower because, in many cases, the heat required can be less than that for APCVD. However, APCVD equipment is often less complex, leading to potentially lower operational expenses.
Some might find APCVD advantageous due to its simpler setup and quicker processing times. However, this might come at the expense of material quality. Each technique presents trade-offs that necessitate careful consideration based on the specific requirements of the project.
LPCVD vs. ALD
Atomic Layer Deposition (ALD) is another important technique for thin film deposition, characterized by its capability to deposit materials at the atomic scale. Compared to LPCVD, ALD excels in achieving supreme conformity and precision in thin film dimensions due to its sequential layer-by-layer deposition process.
The primary advantage of LPCVD lies in its scalability, which allows for producing films over larger substrates, making it suitable for mass production in semiconductor fabrication. While ALD provides exceptional precision, it often involves longer deposition times. LPCVD is favored in situations where throughput is a critical factor, such as during the manufacturing of silicon wafers.
Both techniques also differ in their operational processes. LPCVD uses a continuous flow of reactive gases, which can lead to higher deposition rates than those typically achievable with ALD. However, ALD's capability to form ultra-thin films with atomic layer precision is unmatched, suitable for applications that require exact control over the material's thickness.
As both methods continue to evolve, the choice between LPCVD and ALD largely depends on the specific needs of the application. For instance, where high precision is essential, ALD may be preferable. Conversely, for scenarios involving larger scalable processes, LPCVD might be the more advantageous option.
Culmination and Future Directions
The conclusion and foresight on Low Pressure Chemical Vapor Deposition (LPCVD) techniques is essential for anyone involved in semiconductor fabrication or materials science. As the demand for advanced materials continues to rise, understanding the shifts and developments in LPCVD will guide future innovations. This section summarizes crucial points from the article while exploring potential avenues for further investigation and exploration.
Summary of Key Points
LPCVD offers unique advantages that make it a cornerstone technology in various applications. Key points include:
- Uniform Film Thickness: LPCVD achieves consistent deposition across substrates, creating high-quality thin films crucial for semiconductor devices.
- Enhanced Material Quality: The low pressure environment minimizes contamination, leading to superior material properties.
- Scalability: LPCVD processes can be adapted for small-scale lab research or large-scale industrial needs, catering to diverse production volumes.
- Emerging Trends: Research integrating LPCVD with nanotechnology and automation shows promise in enhancing efficiency and innovation.
These factors underline why LPCVD remains pivotal in advancing technologies that underpin modern electronic systems and materials.
Potential Areas for Further Research
Future research could explore numerous aspects of LPCVD techniques, aiming to refine processes and broaden their application scope:
- New Precursor Development: Investigating new chemical precursors may unlock improved material properties and allow for more complex coatings.
- Optimization of Process Parameters: Researching how variations in pressure and temperature impact film characteristics can lead to more controlled and efficient deposition methods.
- Integration with Advanced Materials: Examining how LPCVD can be employed for new types of materials, such as 2D materials or high-k dielectrics, may broaden its applicability in cutting-edge electronics.
- Automation and Real-Time Monitoring: Implementing machine learning technologies for real-time process optimization could enhance productivity and reliability.
- Environmental Impact Assessments: As regulatory concerns about chemical processes grow, assessing the environmental footprint of LPCVD will be critical.
By addressing these areas, researchers can contribute to the evolution of LPCVD, ensuring it meets the challenges posed by future technological advancements.
"The horizon of LPCVD is broad and filled with potential. Future efforts must be geared towards innovation while ensuring sustainable practices."
Through a concentrated focus on these domains, the relevance of LPCVD in industrial processes can only increase, potentially leading to breakthroughs in numerous fields.