Exploring Innovations in Multi-Material Additive Manufacturing
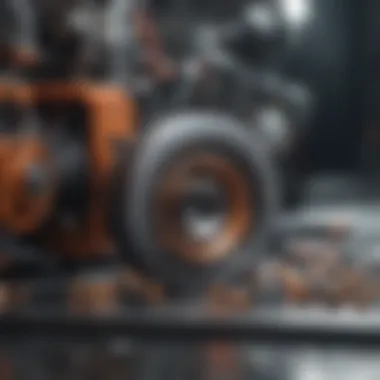
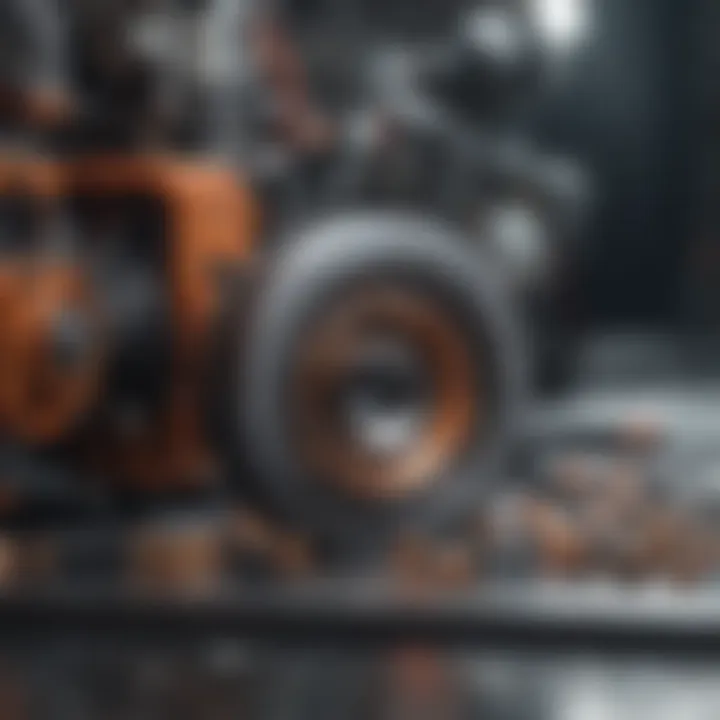
Intro
The progression of technology is often marked by significant shifts that redefine existing paradigms. Multi-material additive manufacturing, an innovative approach blending diverse materials, has surfaced as a game changer in multiple industries. By utilizing additive techniques, manufacturers can revolutionize the way products are created, tackling challenges that traditional methods cannot accommodate.
In this article, a deep dive will be taken into various facets of multi-material additive manufacturing. We will explore key innovations sprouting from this domain, elucidate applications across sectors such as aerospace, healthcare, and automotive, and address the challenges that accompany these advancements. Issues around materials integration and structural integrity cannot be overlooked; thus, we will scrutinize the implications these developments hold for the future of manufacturing.
Key Points to be Covered
- Technological Advances: We will explore the tools and processes behind multi-material fabrication, shedding light on the mechanisms that facilitate the incorporation of multiple materials.
- Applications Across Industries: An examination of how this technology is being harnessed in specific fields will be provided, highlighting noteworthy case studies that showcase its benefits.
- Challenges and Implications: A candid discussion on the obstacles facing multi-material additive manufacturing and the consequences for manufacturers and customers alike.
- Future Directions: Insight into emerging trends and necessary areas for further exploration will guide possible next steps in this evolving field.
"The future of manufacturing lies in the ability to integrate diverse materials in a singular process, offering not just cost-effectiveness but also enhanced performance across the board."
In embarking on this exploration, the reader will gain a comprehensive understanding of multi-material additive manufacturing, setting the stage for informed discussions about its potential disruptiveness in various industries.
Prologue to Multi-Material Additive Manufacturing
In an ever-evolving industrial landscape, multi-material additive manufacturing stands out as a groundbreaking technique that reshapes the way products are designed and produced. It allows the combination of different materials in a single fabrication process, leading to enhanced performance and functionality. This innovation removes the traditional constraints that separate material types and opens up a myriad of possibilities—both technical and creative. Manufacturers can produce components with tailored properties, meaning parts can be lightweight yet strong, flexible yet rigid, and even electrically conductive in certain areas while insulating in others.
The significance of multi-material additive manufacturing cannot be overstated. For industries like aerospace and healthcare, this technology can streamline production and improve product performance. Complex geometries that were once thought impossible to achieve with conventional methods are now within reach, paving the way for more efficient and sustainable manufacturing practices. Furthermore, the potential for customization means that products can be better aligned with user needs, leading to increased satisfaction and utility.
However, embracing this technology also comes with its own set of considerations. Factors such as material compatibility, design intricacies, and technological capabilities need to be evaluated carefully. There’s a lot at stake when integrating different materials because inconsistencies may lead to weakened structures or increased manufacturing costs. Therefore, a thorough understanding of the implications and challenges of multi-material printing is vital.
Defining Multi-Material Additive Manufacturing
Multi-material additive manufacturing refers to the process of using multiple materials to create a single object through additive techniques. Unlike traditional manufacturing methods, which often require additional assembly or post-processing, this technique enables various materials to be deposited simultaneously within the same build process. This capability can significantly reduce assembly time, thus increasing efficiency.
Some of the primary applications for this technology include:
- Functional Prototyping: Creating prototypes that mimic the properties of the intended final product, including differing material characteristics.
- Composite Structures: Building lightweight yet sturdy designs suitable for aerospace applications.
- Medical Devices: Enhancing the performance of implants and devices tailored to individual patient needs through biocompatible materials.
In summary, the definition revolves around the strategic integration of varied materials, enabling innovative solutions that were previously lagging behind traditional manufacturing capabilities.
Historical Context and Development
The journey of multi-material additive manufacturing is a fascinating one, rooted in the broader evolution of 3D printing technologies. Initially, additive manufacturing was focused on single-material processes, with early machines primarily using thermoplastics. As advancements progressed, researchers and manufacturers began to explore the intricacies of combining different materials to enhance performance.
The advent of multi-material printers in the 2000s marked a significant turning point. Companies like Stratasys pioneered technologies that enabled the simultaneous deposition of multiple materials, leading to the development of products with highly specific functional characteristics. This advancement captured the attention of various sectors, from automotive to aerospace, pushing forward the boundaries of what was previously thought feasible.
Today, innovations continue to emerge at a rapid pace, driven by both academic research and corporate investment. Initiatives that bridge the gap between material science and engineering design are becoming increasingly common, signaling a momentous shift in the manufacturing landscape. The historical context of multi-material additive manufacturing serves as a testimony to the ingenuity and creativity that define this exciting field. In essence, it’s a blend of imagination and precision that is transforming traditional manufacturing approaches into something remarkable.
Technological Mechanisms in Multi-Material Manufacturing
In the landscape of modern manufacturing, technological mechanisms play a pivotal role in multi-material additive manufacturing. These mechanisms enable the seamless integration of diverse materials into a single object, facilitating innovations not just in the fabrication process but also in the properties of the final products. Understanding these technologies is crucial for maximizing their potential across various sectors, from aerospace to healthcare.
Additive Techniques Overview
The diverse additive techniques employed in multi-material processing form the bedrock of this innovation-driven field. Unlike traditional manufacturing methods, which often involve subtracting material from larger blocks, additive manufacturing builds components layer by layer. This process allows not only for intricate designs but also for varied material properties to be embedded within a single part. Techniques like fused deposition modeling, selective laser sintering, and binder jetting enable designers to create complex geometries that were once an unrealizable dream.
Compared to conventional production methods, additive techniques often produce less waste, save on material costs, and reduce time from concept to prototype. In this contemporary manufacturing era, where speed and efficiency reign supreme, these benefits cement the relevance of additive techniques.
Material Extrusion and Inkjet Technologies
Material extrusion and inkjet technologies stand out as particularly versatile methods in the additive process. Material extrusion, primarily seen in Fused Deposition Modeling (FDM), involves extruding thermoplastic filament through a heated nozzle. This method is renowned for its capability to print both PLA and ABS materials effectively, and more recently, it's been adapted for multi-material applications, allowing different filaments to be used simultaneously. This integration results in parts that can showcase varying rigidity and surface properties, enhancing functionality significantly.
Inkjet technologies, conversely, make use of liquid materials that are jetted onto a substrate, where they solidify layer by layer. This method has earned its stripes in the realm of producing high-resolution models and prototypes. Importantly, inkjet technologies allow for a combination of materials to be printed simultaneously, offering a broader palette of options when it comes to material properties and finishes. The adaptability of both methods indeed provides an impressive toolkit for engineers and designers alike, encouraging creativity and practical solutions through nuanced material choices.
Powder Bed Fusion Methods
Powder bed fusion methods, including selective laser sintering and electron beam melting, present another tier of multi-material additive manufacturing. These techniques operate by building parts from a pool of powdered material, where a laser or electron beam selectively fuses the powder particles together, layer by layer. This process is not only efficient for creating complex geometries but also enables the mixing of powders from different materials, such as metals and polymers.
Consider the aerospace industry, where weight and strength are critical; the use of powder bed fusion techniques allows manufacturers to design lightweight, strong components tailored to specific applications. However, the complexity of controlling the properties of various materials during the fusion process can present challenges—one needs to ensure compatibility and optimal settings for successful fabrication.
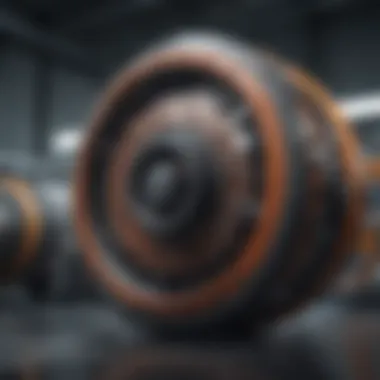
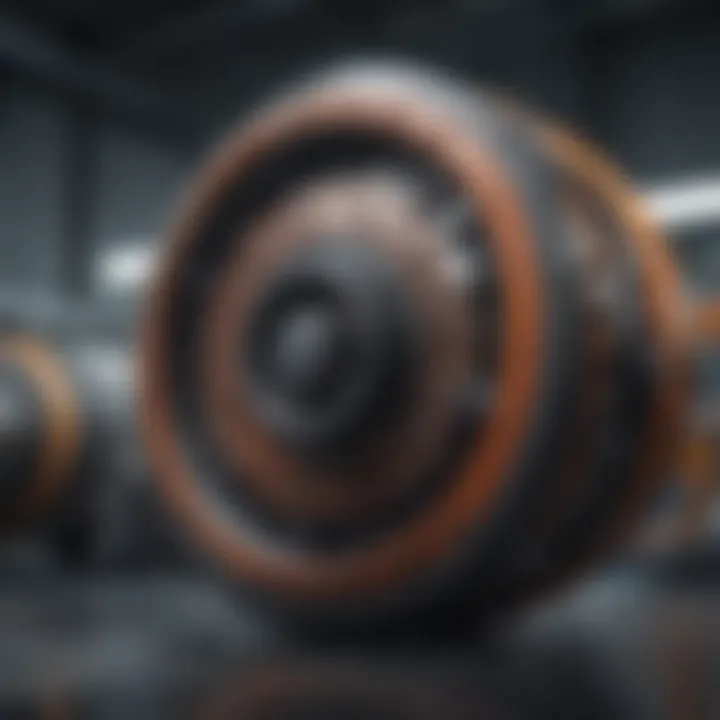
"The advent of multi-material additive manufacturing techniques represents a paradigm shift in how we view design and fabrication solutions."
In summary, the understanding of these technological mechanisms offers crucial insights into how multi-material additive manufacturing reshapes the landscape of production. As industries continue to explore the advantages of integrating diverse materials, these methods elucidate the path forward, presenting unique solutions that bridge gaps in traditional manufacturing paradigms.
The narrative of additive techniques, material extrusion, and powder bed fusion forms a core understanding of the capabilities and considerations that drive multi-material innovations.
Materials in Multi-Material Additive Manufacturing
The significance of materials in multi-material additive manufacturing lies in their ability to enhance the functionality, durability, and overall performance of the finished products. In a world increasingly dependent on innovative manufacturing techniques, the proper selection and application of materials can mean the difference between an average and an outstanding solution. This section will delve into the types of materials that are suitable for multi-material printing, particularly focusing on their interactions, compatibilities, and the benefits they bring to diverse applications.
Types of Compatible Materials
When discussing compatible materials, it becomes apparent that not all materials are created equal. The seamless integration of different materials involves a deep understanding of their properties and behaviors during the additive manufacturing processes. Here are the primary categories:
- Thermoplastics: These materials can be repeatedly melted and solidified, maintaining their inherent properties. Their versatility makes them ideal for a variety of applications.
- Metals: Often prized for their strength, metals like titanium and aluminum are increasingly being included in multi-material prints, allowing for unique structural properties.
- Ceramics: Lightweight yet robust, ceramics can enhance aesthetic appeal and thermal resistance when combined with polymers or metals.
Understanding these materials enables engineers to design components that are not only functional but can also withstand the rigors of their expected environments.
Polymer-Metal Combinations
Polymer-metal combinations are at the forefront of advancements in multi-material additive manufacturing. They provide a fascinating exploration of how disparate materials can work together to produce optimized solutions.
The blend of polymers with metals enables the creation of parts that are both lightweight and strong. For instance, using nylon reinforced with aluminum can lead to components that are easier to handle yet can support substantial loads.
Some benefits and considerations of polymer-metal combinations include:
- Enhanced Durability: Certain polymers, when combined with metals, can improve wear resistance – crucial for applications in the aerospace and automotive sectors.
- Weight Reduction: Light designs maintain strength, providing companies the advantage of fuel efficiency, particularly related to the automotive industry.
- Thermal Properties: Mixing polymers with metals can create materials that withstand extreme temperatures while maintaining functionality.
Ceramic and Composite Materials
Ceramic and composite materials offer a different aspect of multi-material additive manufacturing. These materials can tackle complex challenges in applications demanding not only strength but also heat resistance and electrical insulation.
The integration of ceramics with other materials opens up several unique possibilities, such as:
- High Thermal Stability: Ceramics can be combined with polymers to create components capable of enduring high-temperature environments, which is particularly useful in aerospace applications.
- Improved Structural Properties: Composites can combine the lightweight nature of polymers with the strength of ceramics, suitable for medical devices or automotive parts that require both rigidity and lightness.
- Aesthetic Qualities: Ceramics add a visual aspect that can enhance product appeal, often found in consumer electronics and luxury automotive interiors.
The evolving landscape of materials in multi-material additive manufacturing is not just about what's available now, but also includes what lies ahead for future innovations. As new substances are introduced and tested, the potential of multi-material combinations expands, providing an exciting frontier worth exploring.
Design Considerations in Multi-Material Printing
Design considerations for multi-material printing are paramount for leveraging the full potential of additive manufacturing. When using multiple materials in a single print, the design phase takes on a heightened level of complexity but also unlocks a multitude of benefits. This section will delve into the fundamental aspects of Design for Additive Manufacturing (DfAM) and topology optimization that shape how objects can be created more effectively and efficiently.
Design for Additive Manufacturing (DfAM)
Design for Additive Manufacturing (DfAM) is a methodology that focuses on creating products optimized for the additive manufacturing process. In the context of multi-material printing, DfAM allows designers to exploit material properties to produce parts that are not only functional but also tailored for specific applications.
- Material Selection: Choosing the right materials is crucial. Each material comes with its own characteristics such as strength, ductility, and thermal resistance. Understanding these traits helps in determining which material combination aligns with the operational demands of the final product.
- Geometric Freedom: Unlike traditional manufacturing methods, additive techniques provide significant freedom in terms of geometry. Designers can create complex shapes that were previously impossible to fabricate. This flexibility means that engineers can design intricate cooling channels in an aerospace component or create highly detailed structures in a healthcare application.
- Integration of Parts: Utilizing multiple materials paves the way for integrating various functionalities into a single part. For instance, a brake component in an automotive application could combine lightweight polymers with durable metals, enhancing both performance and efficiency.
- Iterative Design Process: DfAM encourages an iterative approach where prototypes are tested and refined. Rapid prototyping capabilities inherent in additive manufacturing help to quickly adapt designs based on real-world performance.
- Cost-Effectiveness: Thoughtful design can lead to reduced waste and minimized production costs. By consolidating parts and reducing the number of subsequent assembly operations, manufacturing becomes more economically viable.
Ultimately, DfAM represents a paradigm shift in how products are conceived, offering a pathway to widely innovative designs.
Topology Optimization
Topology optimization takes DfAM to the next level by using advanced computational algorithms to analyze and determine the best material layout within a given design space. The goal is to enhance the performance of a structure while minimizing weight and material use. Here’s how this concept plays out in multi-material printing:
- Performance-Centric Design: Topology optimization leverages performance criteria, ensuring that only the necessary material is used where it counts. This is especially vital in industries like aerospace, where weight reduction is linked directly to fuel efficiency.
- Stress Distribution: The optimization processes examine stress flows within a component and redistribute material to areas of high stress while removing it from less critical areas. This data-driven approach leads to structures that are light yet robust, essential for high-stress applications.
- Incorporation of Multiple Materials: In multi-material contexts, topology optimization not only suggests where to place materials but also which materials are best suited for different areas of the design based on their specific properties. For example, softer materials might be optimal in areas needing flexibility, while rigid materials could reinforce stressed locations.
"Topology optimization can dramatically revolutionize how products are designed, enabling the creation of components that are not only lighter but also more efficient and effective."
- Rapid Prototyping Benefits: When combined with rapid prototyping technologies, topology optimization results in innovative designs that can quickly transition from concept to reality. This adaptability is a game changer for industries requiring fast-paced development.
Listing the Benefits of Topology Optimization:
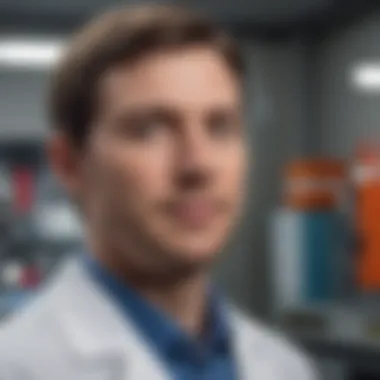
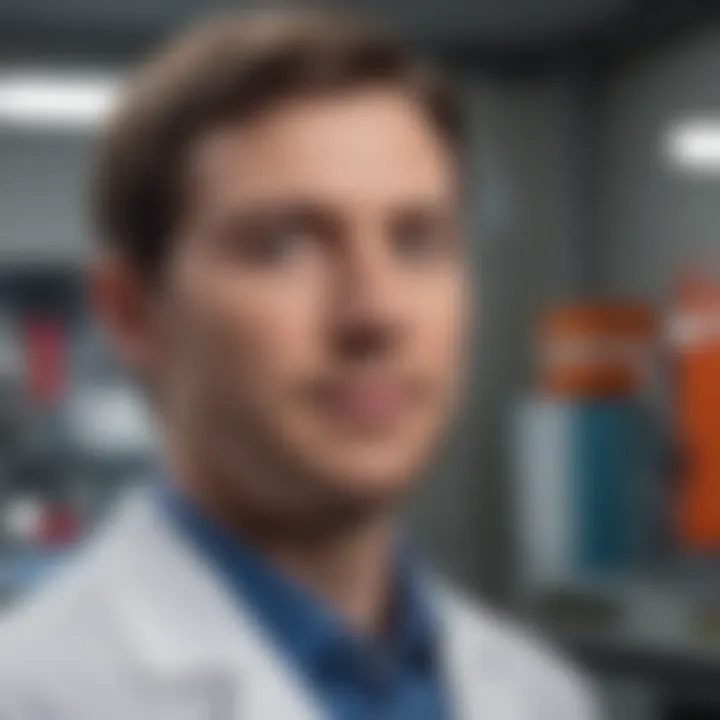
- Reduces material waste
- Increases structural efficiency
- Enhances performance and reliability
- Accelerates the design process
- Decreases overall production costs
Applications Across Various Sectors
In the landscape of manufacturing, the integration of multi-material additive technologies is a game changer. This advancement enhances creativity and problem-solving capability across diverse fields. By enabling the combination of various materials within a single construct, it leads to unprecedented improvements in performance, functionality, and sustainability. Five key benefits stand out in these practical applications while incorporating innovative approaches into manufacturing processes:
- Enhanced Performance: Using multiple materials can create components that outperform those made from a single material. Different parts can be tailored for specific tasks, leading to optimized efficiency.
- Waste Reduction: The precision of additive manufacturing often means less material wasted compared to traditional methods that rely on subtractive approaches.
- Design Flexibility: Designers and engineers are free to explore complex geometries and structures that were previously thought impractical or impossible.
- Cost Efficiency: In the long run, while the initial setup of multi-material systems might be higher, the savings accrued from reduced material waste and enhanced functionality justify the investment.
- Rapid Prototyping: The ability to quickly produce prototypes from various materials allows for efficient testing of concepts, speeding up the time to market.
The next sections will dive into how these multi-material capabilities are reshaping specific industries, such as aerospace, healthcare, and automotive, pushing boundaries and redefining standards.
Aerospace Industry Innovations
In aerospace, where weight reduction and mechanical strength are critical, multi-material additive manufacturing paves the way for tailored solutions like never before. Aircraft components that traditionally utilized heavy metals are now being designed with advanced composites and lightweight polymers. This shift not only contributes to fuel efficiency but also reduces greenhouse gas emissions, aligning with global sustainability goals.
For example, Boeing has been exploring multi-material lattice structures that can provide superior strength at a fraction of the weight. This innovation directly impacts fuel efficiency and overall performance. These structures also allow for more complex geometries that are necessary for optimizing air currents around the aircraft’s form.
Moreover, the industry's leading firms focus on integrating various functionally graded materials to tailor properties in specific regions of components. Think of a component that is hard on the surface for wear resistance but softer beneath to absorb impacts. This approach is transforming design philosophies in the sector.
Healthcare and Bioprinting Applications
Healthcare is undergoing an impressive transformation thanks to multi-material additive manufacturing. This technology supports the creation of customized implants, prosthetics, and even bioprinted tissues that match an individual’s unique biological profile, significantly improving patient outcomes.
A striking case is the 3D printing of bioactive scaffolds, which serve as support structures for tissue growth. These scaffolds are often made from materials like hydrogels combined with biological tissues, promoting cell growth and integration with the surrounding area.
In dental applications, companies are employing multi-material printers to fabricate crowns and bridges that possess a natural aesthetic and superior durability. By layering different materials, practitioners can achieve the necessary translucency and strength that mimics the natural teeth. Add to this, the innovation of using multi-material strategies to create drug delivery systems, offering precise dosages and targeted treatments, it becomes clear how significant this technology is for the future of medicine.
Automotive Manufacturing Enhancements
The automotive sector has seen remarkable advancements through multi-material additive manufacturing. Engineers are leveraging this technology to produce lighter, safer, and more fuel-efficient vehicles. Notably, the use of polymer-metal hybrid components is gaining traction, presenting enhanced performance without a substantial weight penalty.
For instance, companies like Ford are exploring the amalgamation of polymers with metals in parts such as brackets and structural panels. This not only offers increased strength but also reduces the number of parts required, streamlining assembly and further decreasing potential points of failure.
In terms of consumer vehicles, multi-material approaches enable faster customization. Consumers can choose specific configurations and materials for interior components, creating a unique identity for each vehicle.
Additionally, electric vehicles benefit from this technology, as lighter constructs directly influence battery range and performance, making it a highly relevant field of exploration.
As we can see, the applications spread across different sectors signify the transformative power of multi-material additive manufacturing and its potential to redefine products and processes - a real leap toward the future of manufacturing.
Challenges and Limitations
In the realm of multi-material additive manufacturing, recognizing the challenges and limitations is pivotal. The dynamic nature of integrating varying materials introduces a suite of hurdles that can thwart even the most innovative designs. Understanding these impediments is crucial for students, researchers, educators, and industry professionals who are diving into this technology. Tackling these limitations head-on not only fosters better designs and efficiency but also enhances the potential for successful applications in various sectors.
Material Compatibility Issues
A critical aspect to consider in multi-material additive manufacturing is the compatibility of materials. In simple terms, not all materials get along well when they are combined. Each material has its unique properties—such as thermal expansion rates, adhesion strengths, and chemical sensitivities—that can impede the performance of the final product. For example, when attempting to bond a suitable polymer with metal components, differences in how they react to temperature fluctuations can lead to warping or delamination.
Stakeholders need to examine the relationship between materials closely; compatibility should play a central role in the design process. It's beneficial to conduct thorough material testing to assess not just adhesion but also long-term durability. For instance, some polymers may swell when exposed to specific chemicals, which could compromise a composite structure’s integrity.
Technological Constraints
Adapting technology to fit the complexities of multi-material structures presents its own share of problems. The hardware and software used in additive manufacturing must evolve alongside materials to enable the creation of these sophisticated products. Some printers, designed for specific materials, may struggle with others due to nozzle design or limitations in their software capabilities. Additionally, variations in the processing conditions—for example, how fast a print head moves or the heat applied—can lead to uneven results.
Investing in advanced technology that supports multiple materials is essential. Systems like laser sintering or material jetting provide higher degrees of control and precision, but adoption can be costly. These technological investments must align with expected returns, meaning that industries should perform comprehensive analyses before proceeding. Having a strategy that anticipates future needs will be crucial in overcoming current limits.
Regulatory and Standardization Hurdles
In any industry, adhering to standards and regulations is paramount, and multi-material additive manufacturing is no exception. The lack of established guidelines for using multiple materials can stall projects and deter investment. Different sectors, like aerospace or healthcare, have stringent certifications. For instance, materials used in medical devices must not only be effective but also safe for human use. Here, variability in material properties can pose significant challenges.
Moreover, the fragmented regulatory landscape complicates the situation further. Standards vary across regions and industries, meaning that a technology compliant in one area may falter in another. This unpredictability can delay market entry and lead to increased costs, profoundly affecting competitiveness.
"Understanding the challenges of multi-material additive manufacturing is essential for paving the way to innovative solutions. Recognizing these limitations fosters a culture of continuous improvement and growth."
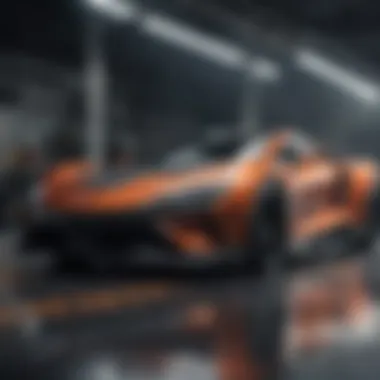
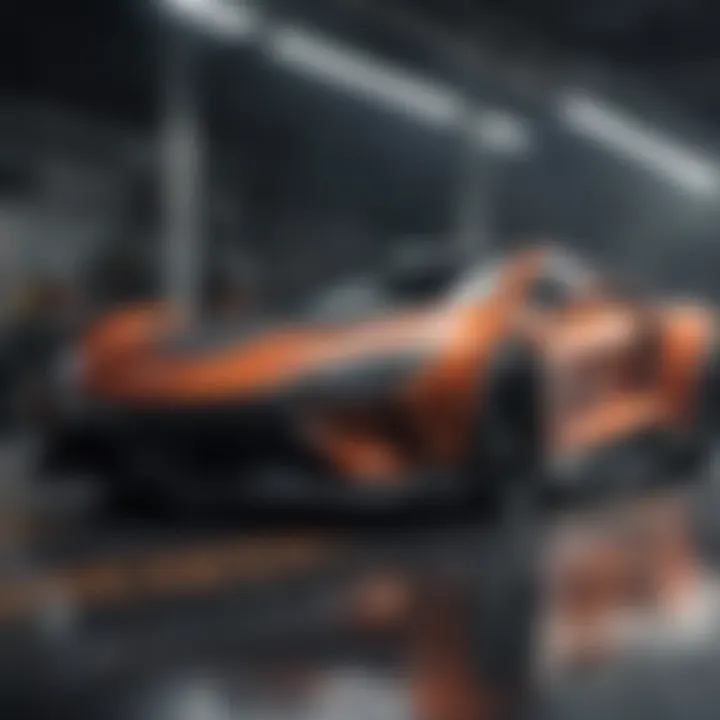
In summary, drawing a clear picture of the challenges involved in multi-material additive manufacturing is essential for anyone engaged in the field. From material compatibility issues to the technological constraints and regulatory hurdles, each aspect presents a unique landscape that needs to be navigated meticulously to harness the full potential of this exciting frontier.
Emerging Trends in Multi-Material Additive Manufacturing
As the landscape of manufacturing evolves, emerging trends in multi-material additive manufacturing not only shape the current industry but also set the stage for future innovations. These trends reflect a shift toward greater efficiency, sustainability, and adaptability, ensuring production processes can meet the increasing demands of various sectors. Understanding these trends is essential for stakeholders looking to leverage multi-material capabilities to maintain a competitive edge.
Integration of IoT and Smart Manufacturing
The integration of the Internet of Things (IoT) into multi-material additive manufacturing represents a game-changer. Traditionally, manufacturing processes operated in silos, where data remained trapped. Now, smart manufacturing, driven by IoT, merges data analytics with manufacturing techniques, leading to several notable advantages:
- Real-Time Monitoring: Manufacturers can track production processes in real-time, allowing for immediate adjustments as needed. This reduces waste and enhances efficiency.
- Predictive Maintenance: Sensors can predict when a machine is likely to fail or need maintenance, minimizing downtime and keeping production on track.
- Enhanced Customization: With data flowing seamlessly, it becomes easier to adapt designs and production lines to meet specific client requirements.
In practical terms, consider an automotive firm utilizing IoT-enabled 3D printers for component creation. By linking each machine to a central data framework, they can quickly respond to changing designs, test new materials, and produce prototypes faster than ever before. This integration not only boosts productivity but also optimizes resource management, making operations more sustainable.
Sustainability Practices in Material Selection
Sustainability is increasingly becoming a central tenet of manufacturing practices. As environmental concerns continue to grow, the emphasis on sustainable practices in material selection for multi-material additive manufacturing is more critical than ever. Key practices include:
- Use of Bio-based Materials: Companies are sourcing renewable materials derived from plants or biodegradable substances to create products less taxing on the environment.
- Recyclability: Many manufacturers are focusing on developing products that can be recycled at the end of their life-cycle, ensuring a circular economy approach.
- Energy Efficiency: Innovations that reduce energy consumption during production processes are gaining traction. For instance, seeking out 3D printing technologies that require less energy can directly contribute to sustainability goals.
Implementing these sustainable practices enhances not only the eco-friendliness of the products but also enriches brand reputation. Consumer interests are shifting toward brands showcasing a commitment to sustainable practices.
"The transition toward sustainable materials in manufacturing practices is not just a trend; it represents what the future of our industries ought to aspire to." - Industry Expert
Future Perspectives and Research Directions
Looking ahead in the field of multi-material additive manufacturing, it becomes clear that this technology harbors significant potential to evolve. As industries demand more intricate designs coupled with improved materials, the direction of future research needs to be reassessed frequently. By seizing the opportunities presented by advanced technologies, stakeholders—from manufacturers to research institutions—can address impending challenges while tapping into fresh market avenues.
Scalability Concerns
One of the major hurdles remains the scalability of multi-material additive manufacturing processes. As businesses gear up to explore how to churn out products in larger quantities without compromising on quality, various factors come into play.
- Production Rates: Technology must push boundaries to enhance production rates. While rapid prototyping services already exist, the leap to mass production needs more innovative solutions.
- Cost Efficiency: High material costs can make large scale production financially burdensome. Researchers must focus on reducing the costs of materials used without sacrificing their properties and performance characteristics.
- Standardization: It is essential to create industry standards that assure consistency in production, especially with multiple materials in play. This requires a cooperative effort across various horizontal sectors, from manufacturers to regulatory bodies.
Scaling up effectively could lead to the implementation of multi-material techniques in everyday production scenarios. The urgent need is to answer questions concerning which practices can provide both efficiency and affordability.
Advancements in Software and Simulation Tools
The role of sophisticated software and simulation tools cannot be overstated. They are the backbone of optimizing designs and streamlining the manufacturing process.
- Design Optimization: Software advancements allow for better design visualization and optimization techniques. Tools can simulate how different materials behave when combined, identifying issues before production even occurs.
- Predictive Analytics: With the rise of machine learning, predictive analytics can forecast potential failures in the multi-material printing process. This minimizes downtime and shapes more reliable manufacturing workflows.
- User Accessibility: Enhanced user interfaces make it easier for designers and engineers to enter the multi-material realm. By simplifying complex data, even those new to this technology can engage effectively.
In summation, the concerted evolution of scalability techniques and software advancements can usher in a new era for multi-material additive manufacturing, enabling it to secure its place within mainstream manufacturing more distinctly than ever before.
Culmination
The conclusion highlights the relevance of multi-material additive manufacturing in today’s rapidly evolving industrial landscape. As this technology continues to gain traction, it is crucial to reflect on its implications for industries, economies, and the future of production itself.
Reflecting on the State of the Industry
The current state of multi-material additive manufacturing is characterized by both excitement and caution. Many sectors, from aerospace to healthcare, are recognizing the transformative potential of using diverse materials within a single build process. This shift is not merely a technical milestone; it shapes design philosophies and operational strategies across fields.
One must consider how industries traditionally reliant on single-material processes are adapting. For example, in aerospace, the integration of lightweight polymers with robust metals is optimizing component performance while reducing overall weight.
Moreover, current innovations are facilitating faster prototyping and lowering production costs. Increased efficiency and customized solutions are becoming norms rather than exceptions. The challenge lies in balancing innovation with regulation. Companies must navigate standards while pushing the boundaries of what is possible. As much as technology advances, the need for safety and compliance is never far behind.
"Adoption of this technology is less about the materials themselves and more about redefining what is manufacturable."
The Path Forward for Multi-Material Additive Manufacturing
Looking forward, the trajectory for multi-material additive manufacturing seems bright yet complex. Scalability is a pressing concern—how to efficiently move from small-scale production to full-blown manufacturing without sacrificing quality.
Advancements in software and simulation tools also promise to enhance this transition. Innovative design software that accommodates multi-material aspects is becoming essential. Engineers are increasingly using simulation tools to predict how different materials will interact during the manufacturing process.
Research continues to push the envelope on material combinations. We could see an explosion of hybrid materials that combine functionalities or even self-healing properties.
On the regulatory side, it's crucial for industry leaders to collaborate with policymakers to streamline standards. The faster they address regulatory hurdles, the quicker the technology can proliferate.