Exploring Aluminum Alloys: Composition and Uses
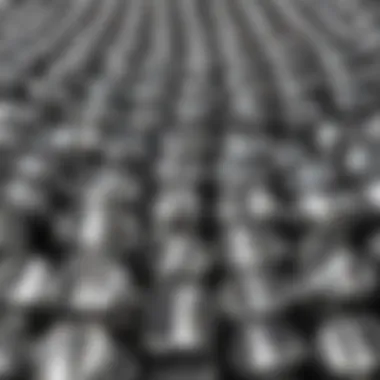
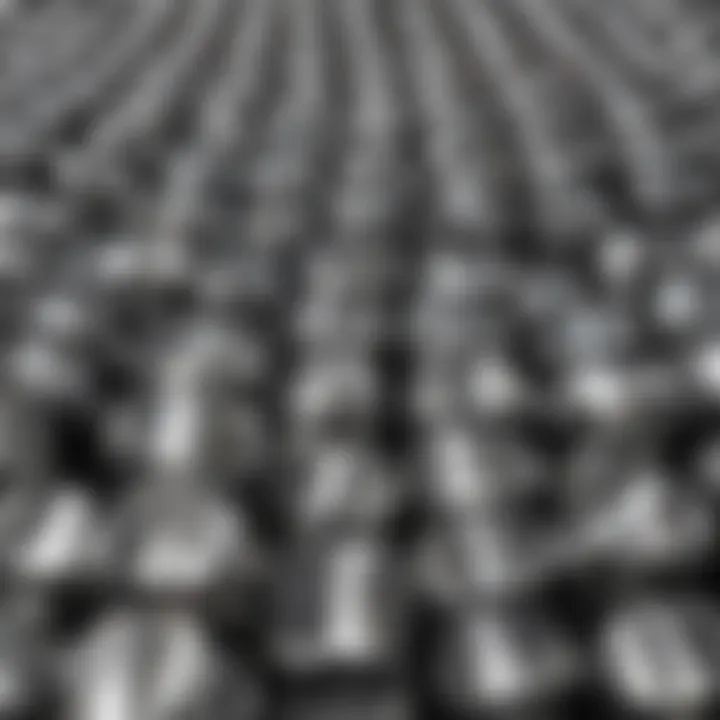
Intro
Aluminum alloys possess significant importance in the realm of engineering and manufacturing. These materials are not just lightweights; they are highly versatile, with a nuanced balance of strength, durability, and resistance to corrosion. When we think about items ranging from aircraft components to everyday household items, the use of aluminum alloys becomes apparent. Understanding the composition and properties of these alloys is crucial for those engaged in industries that demand specific material characteristics.
The allure of aluminum alloys lies in their ability to be tailored for distinct applications. By altering their constituent elements, manufacturers can adjust physical properties to fit the demands of a given use. It’s this adaptability that makes aluminum alloys a popular choice across sectors such as aerospace, automotive, construction, and even electronics.
Furthermore, while delving into aluminum alloys, it's essential to consider the environmental aspects surrounding their use. Aluminum is known for its recyclability, which adds another layer to its appeal. As industries continue to seek sustainable solutions, understanding how to balance performance requirements with environmental considerations becomes even more relevant.
In this exploration, we will take a closer look at what makes aluminum alloys tick. We will break down their composition, dive into their varied properties, and map out the scope of their applications. This article aims to furnish students, researchers, educators, and professionals with a comprehensive understanding of these vital materials.
Prelude to Aluminum Alloys
Aluminum alloys play an integral role in modern engineering and manufacturing, serving a multitude of sectors from aerospace to automotive. Understanding these alloys is essential for anyone involved in material selection, design, or production processes. Their importance can't be overstated, especially considering the blend of light weight and robust strength they offer, making them a go-to choice in many applications.
Understanding Aluminum Alloys
Aluminum alloys are primarily composed of aluminum, enriched with various elements that enhance their physical and mechanical properties. The alloying process modifies the aluminum’s inherent characteristics, resulting in materials that are not only lightweight but also exhibit excellent strength-to-weight ratios. They have low density, which makes them invaluable in weight-sensitive applications. Key benefits of these alloys include not just additional strength but also improved resistance to corrosion and fatigue, making them suitable for prolonged use in harsh environments.
The versatility of aluminum alloys divides them into categories, mainly wrought and cast, depending on the method of shaping and forming during their creation. Within these categories, a variety of specific types comprise different alloy series, each suited for distinct application needs.
Take for instance the 6000 series, which is notable for its excellent corrosion resistance and is commonly utilized in architectural structures like bridges and buildings. On the other hand, the 7000 series, primarily alloyed with zinc, is favored in the aerospace industry for its exceptional strength.
Historical Context
The story of aluminum alloys is as multifaceted as the material itself. Their journey began in the early 19th century when aluminum was first isolated. However, it wasn’t until the advent of the 20th century that significant advancements were made, particularly during World War II, when the demand for lightweight yet durable materials surged.
The military's quest for aeronautical supremacy necessitated alloys that could withstand extreme stress and conditions. This led to the development of several high-performance aluminum alloys that are still in widespread use today. Post-war innovations further expanded their application range, allowing industries to exploit not only the alloys' mechanical properties but also their potential for recycling and sustainability.
From aircraft to automobiles, aluminum alloys have remarkably reshaped the landscape of inert materials, emphasizing how innovation and practical application can spur unmatched progress in engineering. This context not only highlights their versatility but captures the ingenuity of human engineering in leveraging available materials to suit ever-evolving technological needs.
"Aluminum alloys have transformed industries, serving as a testament to the marriage of necessity and innovation."
Understanding these elements – their advantages, historical backdrop, and classifications – is foundational for professionals navigating the complex world of materials science. The ensuing sections will delve deeper into the specific types, properties, and applications of aluminum alloys, ensuring a comprehensive grasp on this essential subject.
Types of Aluminum Alloys
The classification of aluminum alloys is vital to understanding their diverse applications and unique properties. Recognizing the differences and specific advantages of various alloys helps engineers, manufacturers, and researchers to pick the right material for each unique job. Each alloy type possesses its own set of characteristics that can influence factors like strength, weight, and resistance to corrosion. This section dives into two primary categories of aluminum alloys: wrought alloys and casting alloys.
Wrought Alloys
Wrought alloys are shaped through mechanical processes such as rolling, extrusion, and forging. Their name derives from the Old English word "writan," meaning to work or shape, which perfectly suits this method. The distinctive feature of wrought alloys is their exceptional mechanical properties, particularly their formability and toughness. Commonly, wrought alloys receive a series of heat treatments to enhance strength and hardness, making them suitable for demanding applications such as in the aerospace and automotive sectors.
The wrought alloys are categorized primarily by their alloying elements, with each series exhibiting unique traits:
- 1xxx series: Primarily composed of at least 99% aluminum, these alloys boast excellent corrosion resistance and high electrical conductivity. Commonly used in electrical applications.
- 2xxx series: These alloys are rich in copper, offering superior strength but less corrosion resistance. They can be found in aircraft structures.
- 3xxx series: The addition of manganese provides good workability and moderate strength, ideal for applications such as beverage cans.
- 5xxx series: Known for their magnesium content, these alloys exhibit great weldability and corrosion resistance, making them prevalent in marine applications.
Choosing a wrought alloy often depends on the specific mechanical requirements of a project.
Casting Alloys
In contrast to wrought alloys, casting alloys are formed by pouring molten metal into a mold. This method allows for creating complex shapes and structures, which can be a challenge with wrought processing techniques. Casting alloys are typically less expensive to produce and provide a higher yield rate, making them a popular choice for mass production.
The major advantage of casting alloys lies in their ability to mold intricate geometries without the need for extensive machining. They are primarily classified by the alloying elements used and bear a systematic numerical designation system, similar to wrought alloys. The main series of casting alloys include:
- 3xx.x series: Containing silicon and copper, these alloys are noted for their fluidity and freeze resistance, suitable for high-performance components.
- 4xx.x series: These alloys are primarily silicon-based and are known for their low expansion rate and excellent corrosion resistance.
The versatility offered by casting alloys allows engineers to experiment with new designs while maintaining cost-effectiveness, positioning them as a crucial material in industries ranging from automotive to aerospace.
"The choice between wrought and casting alloys hinges on the specific needs of the project, be it strength, weight reduction, or design complexity."
In summary, understanding the types of aluminum alloys lays the groundwork for grasping how their composition and properties dictate their applications. As we dig deeper into alloy classification in the next section, clarity on these two fundamental types will pave the way for more intricate discussions on the significance of various alloy series.
Aluminum Alloy Classification
Aluminum alloy classification plays a pivotal role in understanding how these materials function across various applications. By categorizing aluminum alloys based on their composition, mechanical properties, and processing methods, one can better appreciate their suitability for specific uses. This section emphasizes the significance of classification in selecting the appropriate alloy for engineering and manufacturing projects, ensuring that the inherent properties align with the intended purpose. Understanding classification not only helps in tracking different series of alloys but also aids in making informed decisions about fabrication techniques, treatment processes, and potential applications.
Alloy Series Overview
1xxx Series
The 1xxx series primarily comprises pure aluminum, boasting an aluminum content of 99% or higher. This series is well-known for its excellent corrosion resistance and high thermal and electrical conductivity. It finds applications in areas such as electrical conductors and chemical equipment. The key characteristic that makes the 1xxx series popular is its formability; this alloy can be easily shaped and formed without losing its inherent properties. However, it does not have the same level of strength compared to other alloy series, which can be a limiting factor in high-stress applications.
2xxx Series
With a focus on high strength, the 2xxx series alloys are alloyed with copper, giving them a distinctive characteristic of increased toughness. This series is typically used in aircraft structures where strength is paramount. The unique feature of the 2xxx series is that it can achieve superior mechanical properties through heat treatment, which is particularly beneficial in aerospace applications. However, these alloys can suffer from lower corrosion resistance, which is a drawback when exposed to harsh environments.
3xxx Series
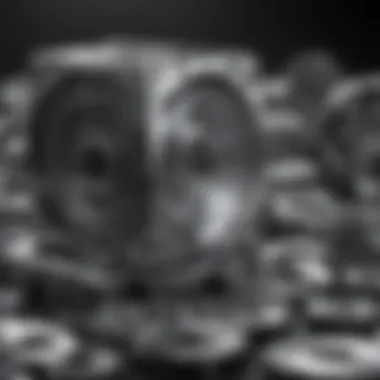
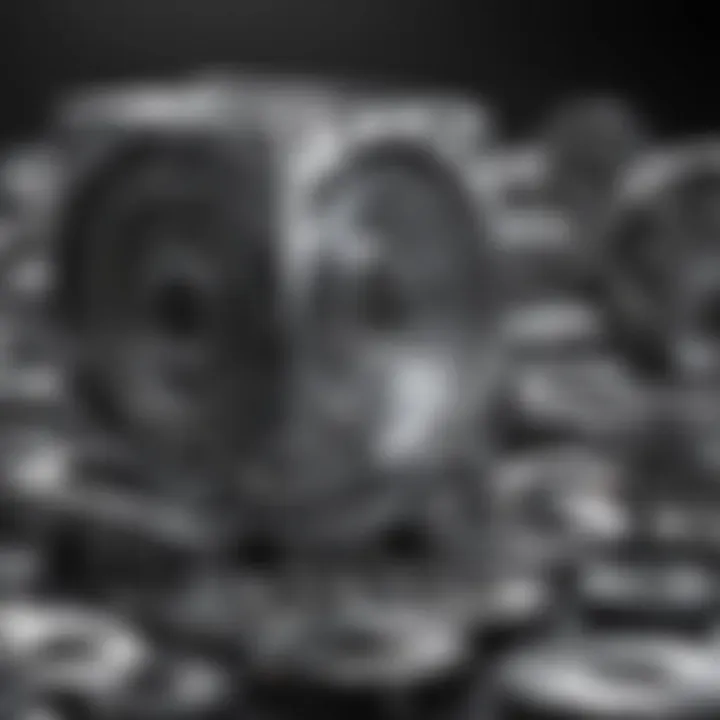
The 3xxx series is mainly alloyed with manganese and is recognized for its good workability and moderate strength. This series is often used in applications that require good formability, such as beverage and food cans. The key advantage of the 3xxx series is its ability to be welded easily, complemented by decent corrosion resistance. But, when compared with the 2xxx series, its strength is relatively lower, making it less suitable for heavy-duty applications.
4xxx Series
The 4xxx series alloys contain silicon, which enhances fluidity during casting and welding processes. This series is often utilized for welding wires and brazing applications. The significant characteristic of the 4xxx series is its lower melting point, which makes them easier to work with during fabrication. Still, the trade-off is that although they are excellent for joinery, their overall strength may not match that of other series, and their corrosion resistance can be moderate.
5xxx Series
This series is alloyed with magnesium, lending it remarkable corrosion resistance and good weldability. 5xxx series alloys are widely used in marine applications where exposure to seawater is commonplace. The strong characteristic of the 5xxx series is its high strength-to-weight ratio, which makes it a favorite in automotive and aerospace sectors. However, it might be less formable than some other aluminum alloys due to its higher strength, which could present challenges in certain manufacturing processes.
6xxx Series
The 6xxx series, which includes both magnesium and silicon, is celebrated for its versatile properties. These alloys exhibit good corrosion resistance, along with medium-to-high strength and exceptional weldability. This combination makes the 6xxx series a staple in construction and structural applications. A unique feature of this series is its adaptability in various fabrication methods, such as extrusion. The downside could be its susceptibility to stress corrosion cracking, especially in certain environmental conditions.
7xxx Series
This series is primarily alloyed with zinc and is known for its high strength, making it a suitable choice for applications requiring significant structural integrity, such as aerospace components. A notable characteristic of the 7xxx series is its ability to be heat-treated to achieve exceptionally strong properties. On the downside, these alloys can be more challenging to weld, and their corrosion resistance can be significantly lower unless specific coatings are applied.
8xxx Series
The 8xxx series includes various elements as alloying agents, making it a catch-all category for aluminum alloys not classified in other series. These alloys are used for specialized applications, such as aluminum foil and packaging materials. The flexibility to customize alloy compositions creates unique capabilities. However, the downside is that the varying properties across the series can lead to inconsistencies, requiring careful consideration before application.
Comparative Analysis
In the comparative analysis of aluminum alloys, one must look closely at the strengths and weaknesses of each series. The 1xxx series excels in conductivity but falls short on strength. Contrastingly, the 7xxx series boasts remarkable strength, albeit with potential issues related to corrosion resistance. Choosing the right alloy involves not just understanding these properties but also considering the specific requirements of the application at hand.
Understanding how these alloys stack up against each other provides more insight into their usage and helps designers and engineers make choices that enhance both performance and longevity in their projects.
Properties of Aluminum Alloys
The properties of aluminum alloys play a pivotal role in various applications, influencing their performance in diverse fields like aerospace, automotive, and construction. Different compositions of aluminum alloys give rise to unique characteristics, making it crucial to understand these properties for selecting appropriate materials.
Mechanical Properties
Mechanical properties are fundamental to understanding how aluminum alloys behave under various conditions. They dictate the alloy's ability to withstand stress, strain, and environmental factors.
Tensile Strength
Tensile strength refers to the maximum amount of tensile (pulling) stress that a material can withstand before failure. This property is paramount in applications where structural integrity is a must. For instance, aircraft wings experience significant tensile forces; hence, materials with high tensile strength are preferred. A key characteristic of tensile strength is that it doesn't only indicate how much load a material can handle, but also its reliability under everyday stress.
A unique feature of tensile strength in aluminum alloys is how it can be significantly increased through heat treatments and alloying techniques, making these alloys advantageous in multiple engineering settings. This adaptability transforms them into a popular choice across sectors like aerospace and construction, where safety is key.
Yield Strength
Yield strength marks the point at which a material begins to deform plastically. Understanding yield strength is essential for engineering because it helps to define the limits of stress a structure can endure without suffering permanent deformations. Aluminum alloys often present a favorable yield strength-to-weight ratio, making them highly beneficial in industries like automotive, where lighter materials can improve fuel efficiency.
A unique aspect of yield strength in aluminum alloys is its lower value compared to other metals, such as steel. This presents a double-edged sword: while aluminum may not be the strongest option, its lower density helps reduce overall weight, an advantageous factor in construction and transportation.
Fatigue Strength
Fatigue strength refers to the material's ability to endure repetitive loading over time without significant degradation. This property is especially critical in environments where cyclic stress occurs frequently, such as in aerospace and automotive applications. Aluminum alloys often exhibit excellent fatigue resistance, a key characteristic that enhances their longevity in demanding settings.
Unique to fatigue strength in aluminum is its influence by surface finish and alloy composition. For instance, some alloys can withstand higher cycles of loading than others, making it essential for engineers to select the right alloy for specific applications.
Impact Resistance
Impact resistance measures a material's ability to absorb and withstand shock loading. This property becomes crucial in applications where sudden influences, such as collisions or drops, can occur. Aluminum alloys typically exhibit good impact resistance, making them suitable for protective applications like safety equipment and bumpers.
The unique feature of impact resistance in aluminum alloys lies in their ductility. This allows them to deform and absorb energy under shock loads, which can provide a distinct advantage over more brittle materials. However, depending on the alloy, impact resistance may vary, so understanding the specific requirements of each application is crucial.
Physical Properties
Physical properties provide insights into how aluminum alloys interact with their environment, influencing manufacturing and applications.
Density
Density, or mass per unit volume, is a critical physical property in materials selection. Aluminum alloys are favored for their relatively low density, making them easier to work with and transport. This is particularly important in industries like aviation, where weight savings can lead to significant efficiency improvements.
A unique characteristic of density in aluminum alloys is that it can vary significantly between different alloy series. As a rule of thumb, lower-density alloys tend to be more ductile, while higher-density ones can possess better strength.
Thermal Conductivity
Thermal conductivity is the ability of a material to conduct heat. In applications where heat dissipation is vital, such as electrical components or heat exchangers, high thermal conductivity is a significant asset. Aluminum alloys are known for their excellent thermal conductivity, making them a go-to choice in many heat management applications.
What's particularly interesting is how alloying can tailor the thermal conductivity. For example, 6061 aluminum alloy exhibits great conductivity, enhancing its appeal in engineering designs that prioritize thermal performance.
Electrical Conductivity
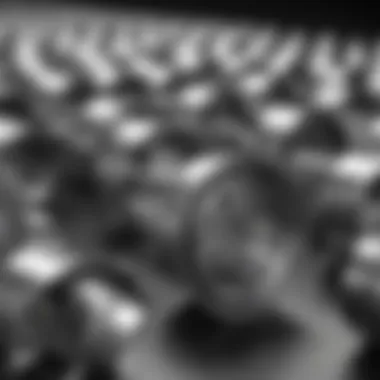
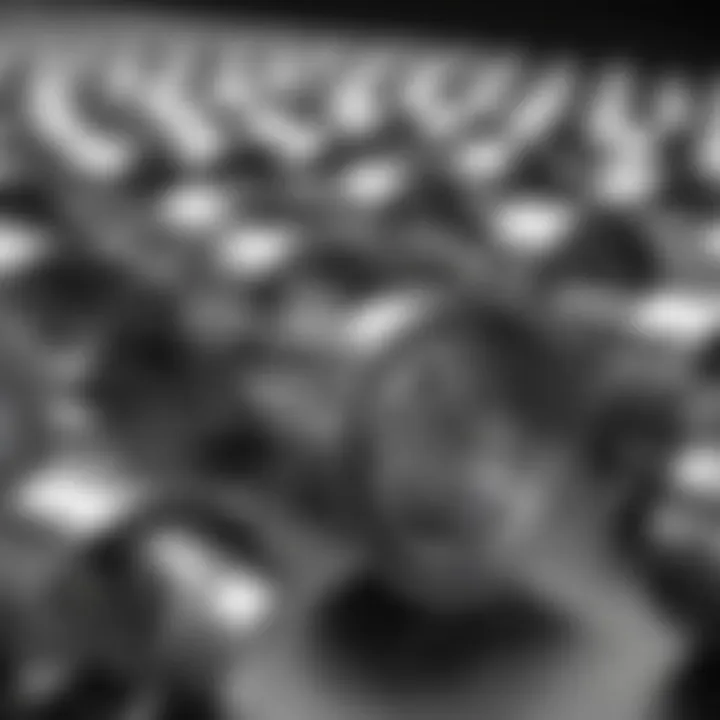
When it comes to electrical conductivity, aluminum alloys shine in many industrial applications. Their ability to carry electrical current makes them suitable for power lines and electrical engineering components. A notable characteristic is that aluminum has about 60% of copper's electrical conductivity, yet is significantly lighter and more cost-effective.
The unique aspect of electrical conductivity in aluminum alloys is their capacity for alloying. Certain combinations can yield alloys with enhanced conductivity, making them even more effective for specific applications, thus expanding their utilitarian scope in electronics and power distribution.
Corrosion Resistance
Corrosion resistance is an essential property of aluminum alloys, particularly when exposed to harsh environments. In many applications, the longevity of the material directly relates to its ability to combat deterioration from moisture, salts, and chemicals.
Aluminum naturally develops a thin oxide layer that provides some protection against corrosion—in fact, some alloys can be even more resistant when treated. However, this beneficial property can vary based on the alloy composition and the conditions it’s exposed to.
It’s important to consider how corrosion might impact the performance and lifespan of aluminum alloys. For instance, in marine environments, selection of the right alloy is imperative to ensure longevity and reliability.
"Understanding the properties of aluminum alloys opens doors to innovative applications and efficient designs across various industries."
In summary, the properties of aluminum alloys are interwoven with their performance and suitability for specific tasks. Grasping these properties not only helps in selecting the right material but also in maximizing their potential benefits.
Applications of Aluminum Alloys
The significance of aluminum alloys stretches far beyond their intricate compositions and physical attributes. They serve as foundational materials across a multitude of industries, essentially acting as the unsung heroes of modern engineering and manufacturing. Their contributing role is not merely functional; it affects safety, efficiency, and environmental sustainability.
When discussing the applications of aluminum alloys, it’s vital to recognize their versatility and the benefits they bring, which include:
- Lightweight Nature: The low density of aluminum alloys means they can help reduce overall weight in design, providing a crucial advantage in performance-driven sectors like aerospace and automotive.
- Corrosion Resistance: The innate ability of aluminum alloys to resist corrosion makes them suitable for outdoor applications, offering durability without the weight penalty.
- Cost-Effectiveness: As compared to alternative materials like titanium and steel, aluminum alloys often provide a more economical solution, balancing performance with cost.
- Fabrication Ease: Their excellent workability means they are not just easy to mold but also to join using various techniques, making them favorable for mass production.
These elements not only highlight their utility but also point toward a key consideration for professionals: the selection of the appropriate alloy can significantly enhance the product durability and performance. Next, we explore specific applications in distinct sectors.
Aerospace Industry
In the aerospace sector, aluminum alloys hold a pivotal role. The demand for lightweight yet strong materials is ever-present, and these alloys are at the forefront of innovation. An airplane's fuselage, wings, and support structures commonly use 7xxx and 2xxx series alloys due to their high strength-to-weight ratio and resistance to fatigue.
It is not just about the weight; safety plays a huge part here. By using lighter materials, planes can save on fuel costs, reduce emissions, and increase their range. Moreover, the ability to withstand extreme temperatures and conditions ensures engineers can rely on aluminum alloys to keep aircraft operations safe.
"The aerospace industry depends on materials that can withstand high stress without adding extra weight. Aluminum alloys perfectly align with this requirement, shaping the future of aviation."
Automotive Sector
In the automotive industry, the push for fuel-efficient and greener vehicles has made aluminum alloys even more relevant. Manufacturers are increasingly incorporating these materials into vehicle designs to trim weight while maintaining structural integrity. The 5xxx and 6xxx series are particularly favored in body panels to minimize overall vehicle weight.
Beyond mere aesthetics and performance, using aluminum can have substantial effects on fuel consumption. This not only benefits consumers in their day-to-day driving but also aligns with global efforts to reduce carbon footprints. With regulations evolving and consumer interest shifting toward electric and hybrid vehicles, aluminum alloys provide solutions that integrate both performance and environmental consciousness.
Construction and Building
When it comes to construction, aluminum alloys are often overlooked yet fundamental. Their strength, coupled with resistance to corrosion, makes them ideal for window frames, roofing systems, and structural components in modern buildings. The 6xxx series, known for its excellent extrudability, frequently finds its way into architectural designs, allowing for intricate shapes and sizes that enhance aesthetic appeal without compromising strength.
Additionally, their lightweight properties contribute to easier transportation and installation, speeding up project timelines and reducing costs. In times where sustainability is a crucial consideration, the recyclability of aluminum further adds to their appeal.
Consumer Goods
Aluminum alloys are also prolific in the realm of consumer goods. Examples range from sleek electronics cases to kitchenware. The widespread use of aluminum in the production of laptops and smartphones stems from its lightweight, durable, and thermal conductive properties.
In the culinary world, aluminum cookware often strikes the right balance between performance and accessibility. Its conductive prowess ensures that food heats evenly, allowing for culinary precision. As consumers become more eco-conscious, the recyclability of aluminum products becomes a significant selling point, creating a market that favors sustainable solutions without sacrificing quality.
In summary, the applications of aluminum alloys are vast and growing. From aerospace to consumer goods, their versatility has positioned them as a cornerstone in various industries, emphasizing their importance not merely as materials but as drivers of innovation and sustainability.
Fabrication Techniques
Fabrication of aluminum alloys is a critical phase in their journey from raw material to finished product. As various industries increasingly rely on the unique properties of aluminum alloys, understanding the different fabrication techniques becomes essential. These methods play a significant role in determining the mechanical characteristics, surface finish, and overall performance of the final product.
Each fabrication method carries its unique benefits and considerations. Understanding these elements can greatly enhance decision-making when selecting an optimal technique for specific applications.
Casting Methods
Casting methods involve pouring molten aluminum alloy into a mold to create specific shapes. This technique is popular due to its versatility and ability to produce complex geometries that would be challenging or expensive to achieve through other methods.
One of the significant advantages of casting is the cost-effectiveness for mass production runs. It allows manufacturers to create large quantities of identical parts without the need for expensive tooling modifications. Furthermore, castings can often achieve intricate designs with minimal waste, which is an important consideration in modern manufacturing.
However, there are drawbacks to consider. For example, the casting process can often introduce defects such as porosity and shrinkage, which may affect the material's strength and durability. As a result, the quality of the produced part often hinges on the expertise of the operator and the casting process itself.
Extrusion and Rolling
Extrusion and rolling are two fundamental processes used to shape aluminum alloys, each with its own distinct characteristics. Both methods are widely used in industries that require long sections of material, like construction and automotive sectors.
In extrusion, a billet of aluminum alloy is heated and then forced through a die to produce a specific cross-sectional shape. This process allows for the creation of lightweight structures with good strength-to-weight ratios. Additionally, the continuous nature of the extrusion process makes it ideal for producing lengthy components like tubing or railings. However, the initial setup for extrusion can be costly, which may pose a barrier for smaller production runs.
On the other hand, rolling involves passing aluminum alloy sheets through rollers to create thin sheets or foils. This method is very efficient and widely used in manufacturing items ranging from automotive parts to food packaging materials. The key advantage of rolling is its ability to produce uniform thicknesses and large surface areas, which are often required in various applications. Yet, maintaining precise control of material properties during rolling can be challenging, and the risk of work hardening must be carefully managed.
Joining Techniques
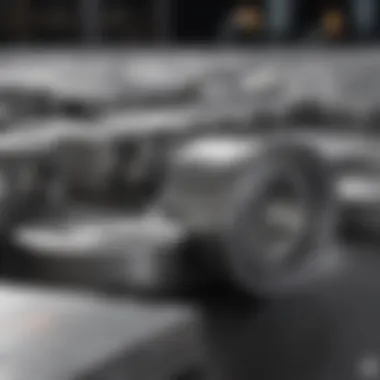
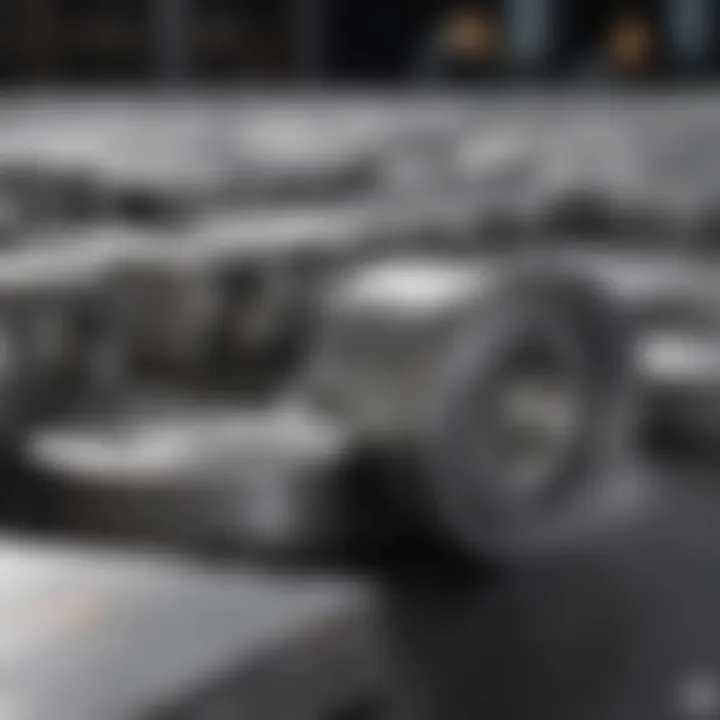
Joining techniques are paramount when assembling components made from aluminum alloys. Different methods provide options depending on the application requirements, including strength, weight, and aesthetics. The common joining methods include welding, riveting, and screwing, each offering distinct advantages and consideration.
Welding
Welding stands out as a favored technique for joining aluminum alloys. This process involves melting the base materials and adding a filler rod to create a strong bond. One key characteristic of welding is its ability to produce a continuous joint that can withstand considerable stress and strain.
Using welding can be particularly advantageous when needing to create strong, permanent connections, which is often required in structural applications like aerospace and automotive manufacturing. A unique feature of welding is that it can accommodate thin-walled sections, although achieving good results with thicker materials can be more complex. The possible downsides of welding include difficulties in managing heat-affected zones, which can lead to changes in mechanical properties of the base material.
Riveting
Riveting has a long-standing history in construction and transportation applications, often leading to robust and reliable connections. This method physically joins overlapping materials using a metal pin or rivet, creating a mechanical bond. The key characteristic of riveting is its simplicity and ability to deliver quick assembly without the need for elaborate machinery.
One of the beneficial aspects of riveting is that it can maintain the material's original strength, making it a reliable choice for lightweight aircraft structures. However, riveted joints can experience loosening over time, especially under cyclic loading conditions, which is a crucial factor to consider in design.
Screwing
Screwing represents another effective method of joining aluminum alloys, especially when temporary connections are desired. Using screws or bolts, this technique allows for easy disassembly for repair or modification purposes. The key characteristic here is flexibility. Screwing allows for quick assembly and has potential for adjusting the tightness or strength of joint connections.
However, a unique feature of screwing is that it can lead to stress concentrations at the thread interfaces, which may compromise the joint under significant loading. While it might not provide the same strength as welding, the ease of use and flexibility often makes screwing an appealing choice in various applications.
In the realm of aluminum alloy fabrication, understanding these methods is key to optimizing the material's properties for specific applications, ensuring efficiency and effectiveness in production.
Environmental Considerations
The discussions surrounding aluminum alloys can't sidestep their environmental implications. As industries chase innovation, the tension between economic growth and ecological preservation becomes ever more pronounced. The usage of aluminum alloys not only overlaps with modern engineering needs but also has vital sustainability aspects that are increasingly important in today's world.
Sustainability of Aluminum Alloys
When dissecting aluminum alloys in the context of sustainability, one must first grasp why they are deemed favorable in this arena. They’re lightweight, which directly correlates with energy efficiency. For instance, in the aerospace sector, using aluminum alloys instead of heavier materials can boost fuel economy significantly. It’s not all about reducing weight, though. The inherent properties of these alloys can also extend the life cycle of products, curtailing waste and promoting a more circular economy. The softness and malleability of certain aluminum alloys make them easy to reshape rather than dispose of.
Also worth noting is their role in reducing overall greenhouse gas emissions. Aluminum alloys can be produced with a lower environmental footprint, especially if sourced from recycled materials. For manufacturers aiming to align with stringent environmental regulations, opting for aluminum isn’t just a smart move; it’s often a necessity.
Ultimately, sustainability in aluminum alloys goes beyond just their usage. It encompasses every facet of their lifecycle, from production to end-of-life considerations.
Recycling Practices
Speaking of end-of-life, let's chew on recycling practices. Aluminum is often termed the 'green metal' for a reason: it is infinitely recyclable without degrading its properties. When aluminum alloys are recycled, about 95% of the energy used in the original production can be saved. This is no small measure. Imagine harnessing energy efficiency where the cost of recycling falls dramatically compared to primary production.
Yet, the road to effective recycling isn't that simple. Contamination during collection can pose issues, often requiring additional processing to separate aluminum from other materials. Still, many industries are mapping out ways to improve their recycling processes and infrastructure. The gradual rise of initiatives like closed-loop systems in manufacturing is another innovative tactic that optimizes recycling opportunities, ensuring that more aluminum makes its way back into production cycles.
In practice, when products reach their array of potential end-of-lives, like in vehicles or consumer goods, having a plan for recycling extends the lifecycle of aluminum alloys. Inevitably, all these practices combine into a grander narrative, highlighting how choosing aluminum is not just a matter of functionality but also stems from a commitment to environmental stewardship.
"The sustainability of aluminum alloys is not just about using a material; it is about transforming our interaction with our planet for better outcomes."
Understanding the ecological advantages of aluminum alloys will empower students, researchers, educators, and professionals alike to make informed choices in material selection, thus contributing to a more sustainable future.
Future Trends in Aluminum Alloys
In the realm of engineering and manufacturing, aluminum alloys are increasingly taking center stage. These materials are not just vital components; they are shaping the future of various industries. With the growing need for lightweight materials that do not compromise strength or durability, aluminum alloys hold great promise in multiple applications. Understanding the future trends in aluminum alloys is crucial for students, researchers, and industry professionals alike.
One significant aspect of future trends is the continuous innovation in alloy development. This encompasses a range of factors including enhanced mechanical properties, improved fabrication techniques, and sustainable practices. These advancements not only optimize existing alloys but also lead to the creation of new ones that meet specific requirements across different sectors.
Innovations in Alloy Development
The industry is witnessing a renaissance in the arena of aluminum alloy engineering. Researchers and engineers are collaborating intensively to bring forth new alloys tailored for specific functionalities.
- High-Strength Alloys: For sectors like aerospace and automotive, there’s a push toward creating aluminum alloys that can withstand intense stresses without adding excessive weight. The use of elements like lithium can significantly improve strength-to-weight ratios, making these materials more desirable.
- Corrosion-Resistant Compositions: With environmental considerations gaining traction, alloys that resist oxidation and corrosion are becoming essential. Incorporating elements such as magnesium or chromium can enhance these traits, extending the lifespan of products, which is a win-win for manufacturers and consumers.
- Smart Alloys: As technology progresses, the development of intelligent materials that respond to environmental or physical stimuli is on the rise. These smart alloys are designed to change their properties or features — for example, adjusting stiffness — in response to varying conditions, thereby adding a new level of versatility.
The emphasis on sustainability has not been overlooked. There’s a distinct focus on using recycled materials in alloy production. This not only minimizes waste but also lowers the energy consumption associated with traditional aluminum production methods.
Emerging Applications
The landscape of aluminum alloy applications is ever-expanding. As these materials continue to evolve, new sectors are creatively integrating aluminum alloys into their stages of production to leverage their unique characteristics.
- Renewable Energy: With the significant shift towards renewable sources, aluminum alloys are being used in solar panels and wind turbine structures. Their lightweight nature helps improve efficiency while reducing the overall weight of these installations.
- Transportation: The automotive industry is a major player in this arena. Vehicle manufacturers are increasingly utilizing aluminum alloys in body panels and frames, aiming to enhance fuel efficiency while maintaining structural integrity. The trend is clear: lighter vehicles equate to lower emissions.
- Consumer Electronics: In gadgets and devices, aluminum not only provides a sleek look but also fosters better heat dissipation. Laptop manufacturers are particularly keen on utilizing aluminum alloys for their casing to ensure both functionality and aesthetic appeal.
"The future development of aluminum alloys promises to break traditional boundaries, blending innovation with sustainability to meet the evolving demands of today’s industries."
Closure
Aluminum alloys play a pivotal role in modern manufacturing, and understanding their importance is crucial for engineers, researchers, students, and enthusiasts alike. This article has explored various facets of aluminum alloys, shedding light on their composition, properties, applications, and the environmental considerations surrounding them. The discussion emphasizes that these alloys are not just materials but critical components that influence the design and efficiency of countless products across multiple industries.
Summary of Key Points
- Composition and Types: The characteristics of aluminum alloys, both wrought and casting, were discussed, highlighting the elemental makeup that affects their behavior and application.
- Properties Overview: Key properties such as mechanical, physical, and corrosion resistance were elaborated upon, noting how tensile strength, thermal conductivity, and durability under environmental stress influence choices in manufacturing.
- Applications Across Industries: Various industrial applications—from aerospace and automotive to consumer goods—underline the versatility of aluminum alloys, showcasing their critical role in engineering innovations.
- Fabrication Techniques: The methods of shaping and joining aluminum alloys were reviewed, pointing to the technical know-how required for effective processing.
- Environmental Impact: The article addressed sustainability issues, recalling how recycling practices and the ecological implications of aluminum production are becoming ever more relevant in today’s world.
Final Thoughts
As industries continue to evolve, so too will the applications and innovations surrounding aluminum alloys. The future points toward advanced alloy development, potentially leading to new properties and capabilities. The intersection of engineering, ecology, and resource management will no doubt keep aluminum alloys at the forefront of materials science. Those who grasp the complexity and significance of these alloys position themselves to contribute meaningfully to advancements in technology and environmental stewardship.
In summary, aluminum alloys are more than a mere collection of metals; they are integral to the fabric of modern manufacturing and engineering solutions. Recognizing their qualities equips professionals and enthusiasts to make informed decisions, ensuring that the developments in this field continue to drive progress and sustainability.
"The future of aluminum alloys lies not just in new alloy compositions but in the astute understanding of how to utilize these materials within the constraints of our environment."
For further reading on aluminum properties and trends, resources such as Wikipedia and Britannica provide valuable insights.