In-Depth Overview of Battery Cell Assembly Processes
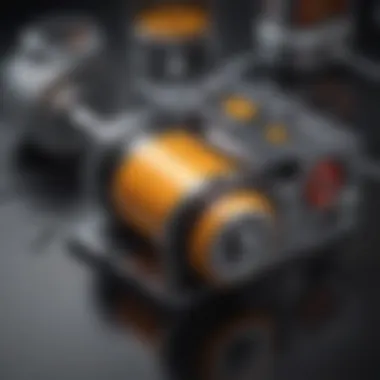
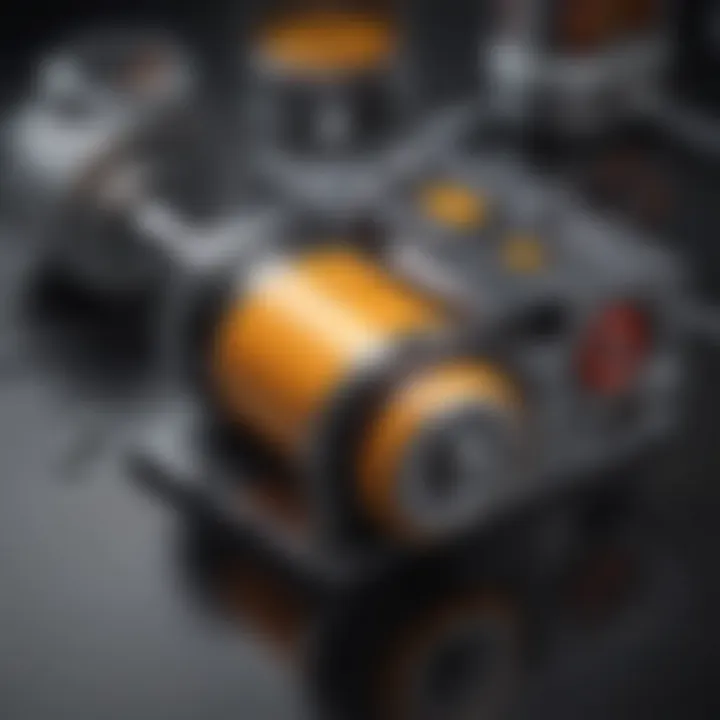
Intro
Battery cell assembly represents a crucial phase in the lifecycle of batteries, influencing their efficiency and reliability in daily applications. Understanding the intricacies of this process is essential for various stakeholders, from engineers to manufacturers and researchers. As the demand for batteries continues to rise, driven by the growth in electric vehicles and renewable energy storage, the need for knowledge about assembly techniques, components, and quality assurance becomes increasingly relevant. This article aims to dissect these elements, providing a comprehensive overview that reflects both established practices and future innovations.
Methodology
Overview of research methods used
The exploration of battery cell assembly is grounded in both qualitative and quantitative research methodologies. A systematic review of existing literature forms the backbone of this study. This approach allows for assessing scholarly articles, technical papers, and industry reports. Interviews with professionals in the field also contribute valuable insights into current practices and future directions. Collectively, these methods present a nuanced understanding of the multifaceted nature of battery cell assembly.
Data collection techniques
Data was collected through several techniques to ensure a well-rounded view:
- Literature Review: Academic journals and articles were scrutinized for the latest findings in battery technology.
- Interviews: Discussions with engineers and technicians provided real-world insights and contemporary assembly practices.
- Surveys: Questionnaires distributed within the industry helped gather quantitative data regarding assembly methodologies and challenges faced by manufacturers.
This multi-faceted approach allows researchers to grasp the breadth of techniques employed in battery cell assembly, facilitating a comprehensive analysis of the information gathered.
Key Components of Battery Cell Assembly
Battery cell assembly involves several integral components, including:
- Electrodes: The anode and cathode are crucial for energy storage and release.
- Electrolyte: This medium enables ionic movement between electrodes.
- Separator: A critical component preventing short circuits while allowing ion flow.
Understanding these components is essential for grasping how they interconnect during the assembly process. Each part plays a significant role in the battery's overall performance and longevity.
Assembly Techniques
Different techniques are employed to assemble battery cells effectively:
- Layer Stacking: This method involves stacking layers of electrodes and separators, which allows for efficient use of space and material.
- Winding: Often used in cylindrical batteries, this method rolls layers of the electrode and separator together, optimizing density.
- Laser Welding: Used for connecting terminals, this technique ensures minimal thermal impact on the materials involved, preserving battery integrity.
Exploring these techniques highlights the diversity in assembly methods, tailored to specific battery designs and applications.
Quality Control Measures
Maintaining high quality in battery cell assembly is vital for safety and performance. Key measures include:
- Visual Inspection: Regular checks to identify defects in components before assembly.
- Functional Testing: Assessing battery performance through discharge and charge cycles.
- Automated Testing Equipment: Advanced systems can detect inefficiencies or flaws in real time, ensuring precision and reliability in output.
Each quality control method addresses potential issues that could arise during assembly, contributing to the final product's efficacy.
Future Directions
Upcoming trends in research
As technology evolves, several trends are emerging in battery assembly research:
- Automation: Increased use of robots and AI-driven systems is streamlining the assembly process, improving efficiency and precision.
- New Materials: Investigating novel materials for electrodes or electrolytes could enhance performance and sustainability.
- Sustainable Practices: Research is shifting toward minimizing waste and optimizing energy usage during production.
Areas requiring further investigation
Certain areas demand more focus:
- Scalability of Advanced Techniques: Understanding how innovative methods can be applied on a large scale remains a challenge.
- Impact of Aging: Researching how components age over time and their effects on battery performance will provide useful insights for longevity.
The exploration in these areas is crucial for the future of battery technology, guiding enhancements in efficiency and sustainability.
Thorough knowledge of battery cell assembly is imperative for driving innovations in storage technology and addressing emerging energy demands.
Prologue to Battery Cell Assembly
The process of battery cell assembly plays a crucial role in the development and production of energy storage devices. In a world increasingly reliant on portable electronics and electric vehicles, understanding this discipline becomes essential. Proper assembly of battery cells ensures enhanced efficiency, safety, and lifespan of batteries. Every component, from the anode to the electrolyte, must be meticulously integrated to meet specific energy demands.
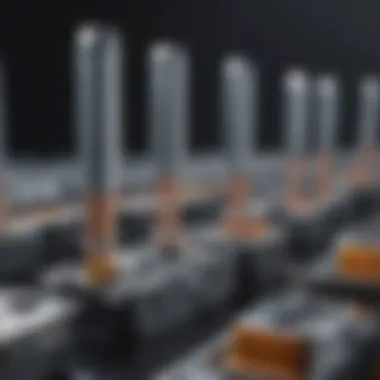
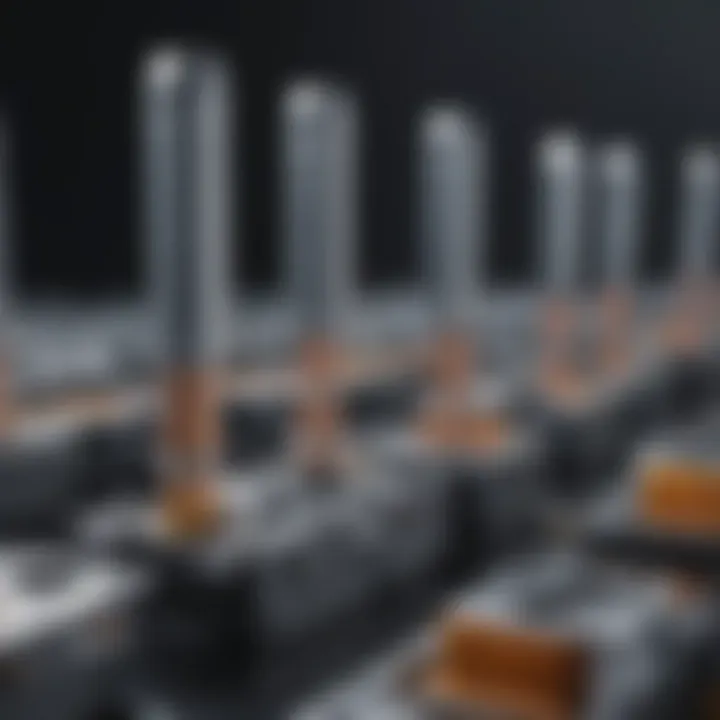
Definition and Overview
Battery cell assembly refers to the systematic process through which individual battery cells are constructed. It encompasses various stages, from selecting materials to integrating them into a functioning unit. A typical battery cell consists of an anode, cathode, electrolyte, and separator. Each of these components contributes to the overall electrochemical reactions that enable the battery to store and discharge energy.
Battery cells come in various formats, such as cylindrical, prismatic, and pouch cells. The choice of design impacts not only the manufacturing process but also the battery's performance and application areas. The objective of battery cell assembly is to create a consistent and reliable product that can efficiently store energy for its intended use.
Importance in Energy Storage Solutions
The significance of battery cell assembly cannot be understated. First, it is fundamental to achieving the performance characteristics required in modern energy storage solutions. As the demand for efficiency and longevity in batteries grows, so does the need for precision in assembly processes. Properly assembled battery cells exhibit improved charge-discharge capabilities, longer life cycles, and enhanced safety, which is vital for users and manufacturers alike.
Moreover, the assembly process directly influences the sustainability and environmental impact of battery production. A well-designed assembly technique reduces waste and optimizes resource usage, supporting broader goals of environmental responsibility.
Additionally, innovations in battery cell assembly techniques are shaping future energy storage technologies. As the industry evolves, stakeholders must adapt to emerging trends and challenges, ensuring that the assembly process remains relevant and effective in meeting future energy demands.
"The future of energy storage lies in how well we can assemble battery cells, merging technology with sustainability."
Understanding battery cell assembly is not merely a technical need; it is an engagement with the future of energy utilization. By grasping these complexities, students, researchers, educators, and professionals can contribute meaningfully to ongoing advancements in the field.
Components of Battery Cells
Understanding the components of battery cells is crucial for grasping how batteries operate and are assembled. Each component serves a specific function, dramatically influencing the overall performance, capacity, and safety of the battery. The selection of materials and their characteristics are essential not only for efficiency but also for longevity and sustainability. In the context of this article, we will explore the various components in detail: anode materials, cathode materials, electrolyte types, and separator functions. This deep dive provides insight into the assembly process and its complexities, shedding light on the advancements in battery technology.
Anode Materials
The anode is a critical part of the battery cell. Generally, it undergoes oxidation during discharge, releasing electrons that flow through an external circuit to the cathode. Common materials for anodes include graphite, silicon, and lithium titanium oxide. Each material brings distinct benefits;
- Graphite: Widely used due to its stable cycling and good electrical conductivity.
- Silicon: Offers a higher theoretical capacity than graphite, presenting potential for greater energy storage.
- Lithium titanium oxide: Known for fast charging capabilities and excellent safety features, albeit with lower capacity.
While performance is important, considerations such as cost and environmental impact also play a crucial role in material selection. With growing concern around sustainable practices, research continues into alternative materials that can deliver similar performance while reducing ecological footprints.
Cathode Materials
Cathodes act as the receptacles for the electrons released by the anode. The choice of cathode material affects the battery’s overall voltage capacity, energy density, and thermal stability. Common cathode materials include lithium cobalt oxide, lithium iron phosphate, and nickel manganese cobalt. Benefits and limitations of these materials include:
- Lithium cobalt oxide: Known for high energy density; however, its long-term stability concerns have raised some red flags among manufacturers.
- Lithium iron phosphate: Offers excellent thermal stability and longevity but has a lower energy density compared to others.
- Nickel manganese cobalt: Balances energy density and stability, providing a more versatile solution.
Understanding cathode materials helps in designing battery cells for specific applications, whether it’s in electric vehicles or consumer electronics.
Electrolyte Types
Electrolytes facilitate ionic movement between the anode and cathode, thus enabling the flow of electrical current. They can be either liquid or solid and significantly impacts the battery's overall performance. Several types include:
- Liquid electrolytes: Often preferred for their high ionic conductivity but can pose leakage risks.
- Polymer electrolytes: Solid-state options that can improve safety and are less likely to leak but have lower ionic conductivity.
- Ceramic electrolytes: Emerging technologies showing promise for high-temperature applications and improved safety.
Selection of an appropriate electrolyte type is vital for balance between performance, safety, and operational versatility.
Separator Functions
The separator is an often overlooked but essential component of the battery. It serves to prevent physical contact between the anode and cathode while allowing ionic transfer. Some properties to consider include:
- Porosity: High porosity allows for efficient ionic transport.
- Thickness: A balance between providing sufficient protection and minimizing resistance is needed.
- Chemical stability: The separator must withstand electrochemical conditions without degradation.
Common materials used for separators include polyolefin films like polyethylene and polypropylene. The development of advanced separators that enhance safety and reduce the risk of short circuits is a key area of research in battery technology.
"Each component plays a significant role in the functionality and efficiency of battery cells, impacting everything from energy density to safety and sustainability."
Battery Cell Assembly Techniques
Battery cell assembly techniques represent a pivotal aspect in the manufactury of batteries. These techniques not only dictate the efficiency and reliability of the assembly process but also affect the overall performance of the cells produced. Understanding these methods is essential for innovation in battery technologies, particularly in the context of increasing energy demands and the push for sustainable solutions.
Manual Assembly Processes
Manual assembly processes involve human operators in the construction of battery cells. This method allows for a high level of precision and flexibility. Operators can adapt quickly to changes in design or specifications, making manual methods beneficial for low-volume production or prototyping phases. Human oversight can also be advantageous for complex tasks that require delicate handling, ensuring careful placement of components such as anodes and cathodes.

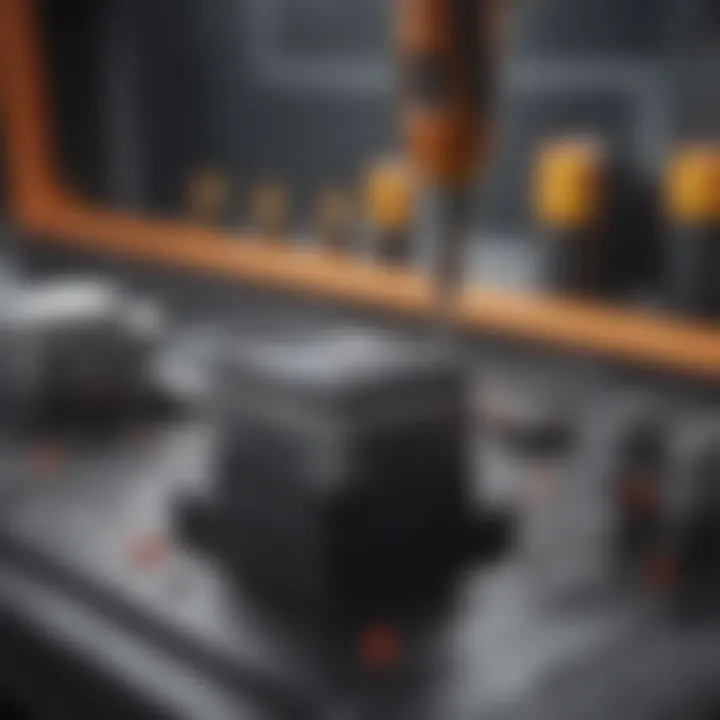
However, manual assembly is not without challenges. The reliance on human labor can introduce variability and increase the potential for errors. As a result, these processes may not be ideal for high-volume production where consistency and speed are priorities. Moreover, labor costs can escalate, impacting overall manufacturing expenses.
Automated Assembly Methods
Automated assembly methods leverage advanced technology, including robotic systems and automated machinery, to manufacture battery cells. These systems significantly enhance efficiency and precision compared to manual processes. Automation minimizes human error, leading to increased consistency in the cell assembly.
Automated methods can also optimize production speed. Automated lines can operate continuously with minimal downtime, allowing manufacturers to meet growing demand. Furthermore, the integration of artificial intelligence in these systems aids in real-time quality monitoring, thus improving yield rates. Nevertheless, the initial investment in automation technology can be substantial, and training staff to oversee these systems may also require time and resources.
High-Throughput Assembly Lines
High-throughput assembly lines are an evolution of automated methods designed to maximize output. This type of assembly involves multiple stations where various tasks occur simultaneously. It is particularly suited for large-scale battery production, where uniformity and rapid throughput are critical.
The benefits of high-throughput assembly lines include:
- Increased Production Rates: These lines can produce vast quantities of battery cells within a shorter timeframe, meeting the surging demand from sectors such as electric vehicles.
- Efficient Resource Utilization: High-throughput methods allow for optimal use of materials and labor, reducing waste.
- Enhanced Quality Control: Each stage can be monitored for consistency, ensuring that any defects are identified and corrected swiftly.
Despite these advantages, high-throughput assembly lines require significant upfront investment and continuous maintenance. The complexity of the systems can also pose challenges in terms of troubleshooting and repairs.
In summary, the choice of assembly technique can have profound implications on production efficiency, cost, and product quality. Manufacturers must consider these factors carefully when developing their production strategies.
Quality Control in Battery Assembly
Quality control is a critical aspect of battery assembly. Its significance cannot be understated, as it directly impacts the performance, safety, and reliability of the final battery products. This section delves into various elements of quality control techniques employed during the battery assembly to ensure that every unit meets the required standards.
Effective quality control in battery assembly functions as a safeguard against defects and performance failure. It encompasses systematic processes that verify adherence to design specifications and build quality. By implementing rigorous quality control measures, manufacturers can significantly reduce the likelihood of malfunctions that could lead to catastrophic failures or even safety hazards.
Further, the economic implications of quality control are profound. High defect rates can lead to increased cost of production, waste of materials, and damage to brand reputation. Thus, ensuring high standards in quality control can promote long-term sustainability and success in battery manufacturing.
Testing Procedures
Testing procedures are foundational to quality control in battery assembly. These procedures determine whether the batteries function as intended under various conditions. The common testing methods include:
- Capacity Testing: Measures the maximal amount of charge a battery can store and its ability to deliver that charge under load.
- Cycle Life Testing: Evaluates how many charge and discharge cycles a battery can undergo before its performance degrades.
- Temperature Testing: Assesses how the battery performs at extreme temperatures, both hot and cold.
- Leakage Testing: Checks for any electrolyte leakage that may occur due to defective seals.
Each testing procedure is designed to confirm that the batteries can operate efficiently in real-world scenarios. Documentation of test results is essential, as it aids in identifying trends in battery performance, ultimately leading to enhancements in manufacturing processes.
Defect Detection Technologies
Defect detection technologies play a pivotal role in identifying potential issues during the assembly process. These technologies can vary from manual inspections to advanced automated solutions. Some key defect detection technologies include:
- Machine Vision Systems: Uses cameras and image processing to detect inconsistencies in battery components and assembly quality.
- Ultrasonic Testing: Employs sound waves to identify faults in solder joints and connections.
- X-ray Inspection: Offers a non-destructive way to examine internal structures of a battery to ensure components are correctly assembled.
By integrating these technologies, manufacturers can reduce the time spent on manual inspections and improve overall accuracy in defect identification. This not only enhances product quality but also increases confidence in the safety and reliability of the batteries.
Standards and Certifications
Adhering to industry standards and obtaining certifications is vital in the battery assembly process. Standards provide guidelines that ensure quality and safety. Some important standards include:
- ISO 9001: Outlines requirements for a quality management system, applicable to any organization, including battery manufacturers.
- IEC 62133: Specifies safety requirements for batteries used in portable applications.
- UL Certification: Ensures that the battery meets certain safety and performance standards set by Underwriters Laboratories.
Achieving these certifications confirms the manufacturer's commitment to quality and safety in production processes. Compliance with such standards helps to build trust with consumers and partners. It also facilitates access to global markets, as many countries require adherence to specific regulations before allowing product entry.
Technological Innovations in Battery Cell Assembly
Technological innovations are reshaping the landscape of battery cell assembly. These advancements are essential in meeting the demands of modern energy storage solutions, particularly as the world moves toward cleaner and more efficient energy technologies. The industry faces growing pressure to enhance production efficiency, product quality, and sustainability. This section explores key innovations that are revolutionizing assembly processes and improving performance outcomes in battery production.
Advanced Robotics in Manufacturing
The adoption of advanced robotics has significantly transformed battery cell assembly. Robotics offer precise and repeatable movements, reducing variability in assembly processes. The implementation of robotic arms enables high-speed assembly, ensuring that components are aligned and fitted with exceptional precision. Companies like Universal Robots are leading the charge in automation technology, providing solutions that not only enhance production rates but also lower labor costs.
Moreover, robots can operate in environments that are hazardous to humans. This is particularly relevant in battery manufacturing, which involves handling corrosive substances and high-temperature processes. With safety as a priority, integrating robotics into the assembly process allows for safer operations while maintaining high output levels. The benefits are clear: increased efficiency, lower error rates, and reduced production time.
Digital Twins and Simulation
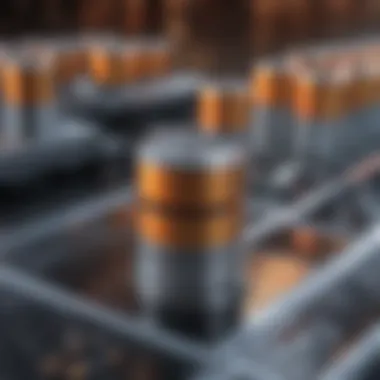
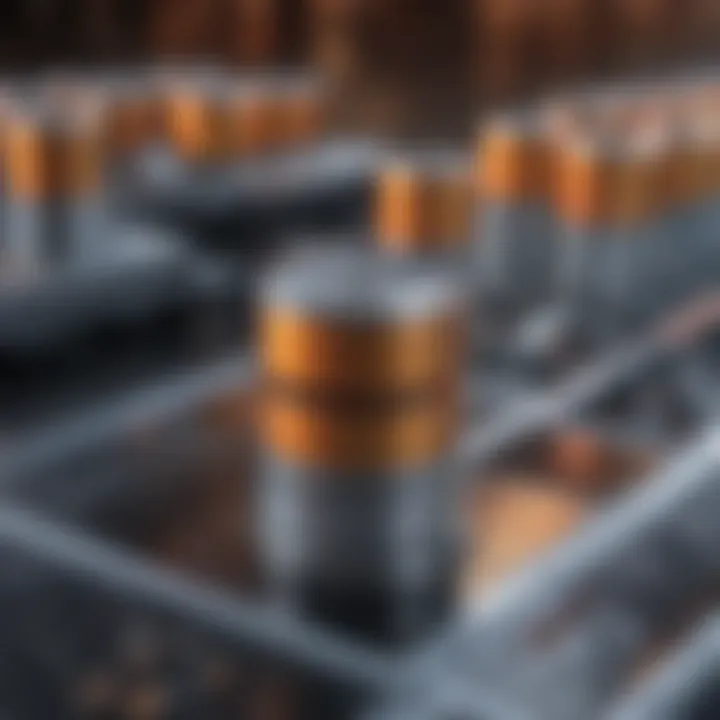
Digital twin technology plays a crucial role in optimizing battery cell assembly. By creating virtual models of the assembly line, manufacturers can simulate various processes. This helps in identifying bottlenecks before they occur and assessing the impact of changes in real-time. Using software tools, companies can analyze the digital twin to predict equipment failures and optimize maintenance schedules. This foresight aids in minimizing downtime, leading to a more efficient production cycle.
Additionally, simulations allow for better training of assembly line workers. They can experience realistic scenarios without the risks associated with actual assembly environments. Training with digital twins can enhance workers' understanding of the assembly processes, ultimately leading to improved productivity and quality control.
Sustainable Practices in Assembly
Sustainability is becoming increasingly important in battery cell assembly. The industry recognizes the need to minimize its environmental impact. Key practices include the use of eco-friendly materials, energy-efficient manufacturing processes, and waste reduction strategies. Many companies are now sourcing recyclable materials for battery components, focusing on reducing reliance on virgin resources.
Furthermore, advancements in energy storage technologies can enhance the sustainability of assembly practices. For instance, developments in solid-state batteries are paving the way for safer and more efficient production methods. These batteries often require fewer hazardous materials, resulting in a safer work environment and a smaller ecological footprint.
Challenges in Battery Cell Assembly
Battery cell assembly faces several notable challenges that can affect production efficiency, cost, and overall quality. Understanding these challenges is vital as the industry continues to evolve. The increasing demand for batteries in applications such as electric vehicles and renewable energy systems amplifies these challenges. Addressing them is important not only for companies but also for the sustainability of battery technology as a whole.
Supply Chain Issues
Supply chain issues can create significant roadblocks in the battery cell assembly process. Various factors, such as geopolitical tensions, natural disasters, or global pandemics, can disrupt the flow of raw materials needed for battery production. This instability can lead to production delays and increased costs. Many battery manufacturers rely heavily on a few suppliers for critical components, which makes them vulnerable to fluctuations in supply.
Additionally, transportation delays can further complicate matters. For instance, lithium, a vital component used in battery cathodes, often comes from remote locations far from assembly facilities. Disruptions in transportation not only increase costs but can also lead to quality issues if materials are stored for extended periods before use. Companies need to develop strategies for diversifying suppliers and improving logistics to mitigate these risks.
Material Shortages and Sourcing
Material shortages represent another high-stakes challenge in battery cell assembly. As demand increases for electric vehicles and renewable energy storage, sourcing the right materials becomes increasingly competitive. Common battery materials like nickel and cobalt face potential shortages due to limited mining locations and ethical sourcing issues.
Manufacturers must navigate a complex landscape where resource availability does not always align with production needs. The prices of these materials are also very volatile, influenced by market fluctuations and investor behavior. Maintaining a balance between material availability and production sustainability is crucial. Establishing long-term contracts and exploring alternatives such as recycled materials or synthetic options can be beneficial strategies to counteract these shortages.
Environmental Regulations
Environmental regulations add another layer of complexity to battery cell assembly. Many countries are implementing stricter laws concerning battery manufacturing's environmental impact. Regulations often focus on reducing waste, emissions, and ensuring responsible sourcing of materials. Compliance with these laws often requires substantial investments in technology and process improvements.
Moreover, regulations may require manufacturers to adopt sustainable practices such as waste management systems and energy-efficient machinery. These changes can lead to increased upfront costs but can also save money in the long run through improved efficiency and reduced energy consumption. Staying ahead of these regulatory changes is critical for companies that aim to remain competitive in a rapidly evolving landscape.
"Understanding and adapting to the challenges in battery cell assembly is not just a matter of competitive advantage; it is essential for the sustainable development of the energy storage sector."
The Future of Battery Cell Assembly
The future of battery cell assembly is critical to the ongoing evolution of energy storage technologies. As energy needs grow alongside the demand for sustainability, innovations in this field hold the potential to redefine battery production. Companies that invest in advanced methods will benefit from increased efficiency and reduced costs. This section discusses trends in battery technology, integration with renewable methods, and breakthroughs in recycling that are shaping the coming years.
Trends in Battery Technology
Battery technology is advancing rapidly. New materials and chemistries promise to enhance energy density and longevity. For instance, solid-state batteries are gaining attention for their superior performance compared to traditional lithium-ion cells. They offer higher energy capacity and improved safety. Additionally, advancements in lithium-sulfur and sodium-ion batteries could lower costs and environmental impact. Researchers are exploring novel approaches, such as using organic materials to create batteries. Overall, these trends indicate a clear shift towards more efficient and sustainable solutions in energy storage.
Integration with Renewable Technologies
The integration of battery cells with renewable energy systems is transforming both fields. As solar and wind power become more predominant, reliable energy storage solutions are essential. Batteries enable smooth energy transitions, allowing users to store excess energy generated during peak production hours. This integration facilitates energy resilience and reliability. Moreover, companies that adapt their assembly processes to incorporate renewable technology will stay competitive. Smart grids and decentralized energy systems rely heavily on effective and timely battery assembly to optimize resources and reduce waste.
Innovations in Recycling and Reuse
Recycling and reuse of battery materials is becoming a priority in the industry. As demand for batteries increases, managing waste effectively is crucial. Innovations such as hydrometallurgy and direct recycling processes can recover valuable components from old batteries. These techniques not only reduce the need for new raw materials but also minimize environmental damage. The development of closed-loop systems ensures that materials cycle back into production, reducing landfill waste and the carbon footprint. By enhancing battery recycling practices, manufacturers can position themselves to meet regulatory demands and respond to consumer expectations for environmentally responsible products.
"The future of battery cell assembly not only relies on new technologies but also on sustainable practices that ensure minimal environmental impact."
In summary, the future of battery cell assembly is driven by trends in technology, integration with renewable sources, and recycling innovations. These developments will not only define the industry landscape but also play a significant role in shaping global energy policies.
Epilogue
The conclusion is a vital component of this article. It ties together all the insights presented, providing a concise yet comprehensive overview of battery cell assembly. Understanding the intricate nature of this process allows stakeholders to appreciate its significance in the broader context of energy storage solutions.
Summary of Key Insights
In our exploration of battery cell assembly, several key insights emerge:
- Complexity of Assembly: The assembly of batteries involves a sophisticated interplay of various materials and techniques. Each component, from anodes to electrolytes, plays a critical role in the overall performance.
- Quality Control Measures: Implementing robust quality control protocols ensures the reliability and safety of batteries. Testing procedures and detection technologies are imperative in avoiding defects.
- Technological Advances: Innovations in automation and the integration of sustainable practices are reshaping assembly methodologies. These advancements are not only enhancing efficiency but also reducing environmental impact.
- Future Trends: Ongoing research indicates a strong trend towards integrating renewable technologies and improving recycling methods. The industry is moving towards a more circular economy in battery production.
The Impact of Ongoing Research
Research continuously impacts the field of battery cell assembly. Universities, private companies, and collaborative projects are pushing boundaries. Some notable areas of focus include:
- Material Development: Innovations in materials can greatly enhance battery capacity and lifespan. Research into novel anode and cathode materials could lead to significant improvements in energy density.
- Efficiency Improvements: Improving the efficiency of assembly techniques is a focal point. More advanced robotics and streamlined processes can reduce costs and time.
- Environmental Considerations: There is a significant push towards sustainable practices. Ongoing research addresses the environmental ramifications of battery production, leading to better recycling technologies.
Overall, the future of battery cell assembly hinges on these groundbreaking research efforts. As the industry continues to evolve, the integration of innovative technologies will play a crucial role in meeting global energy demands.