Exploring 3D Printing Innovations for Large Objects
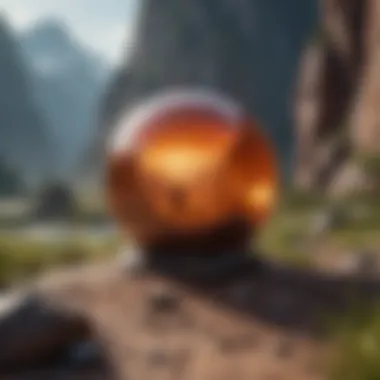
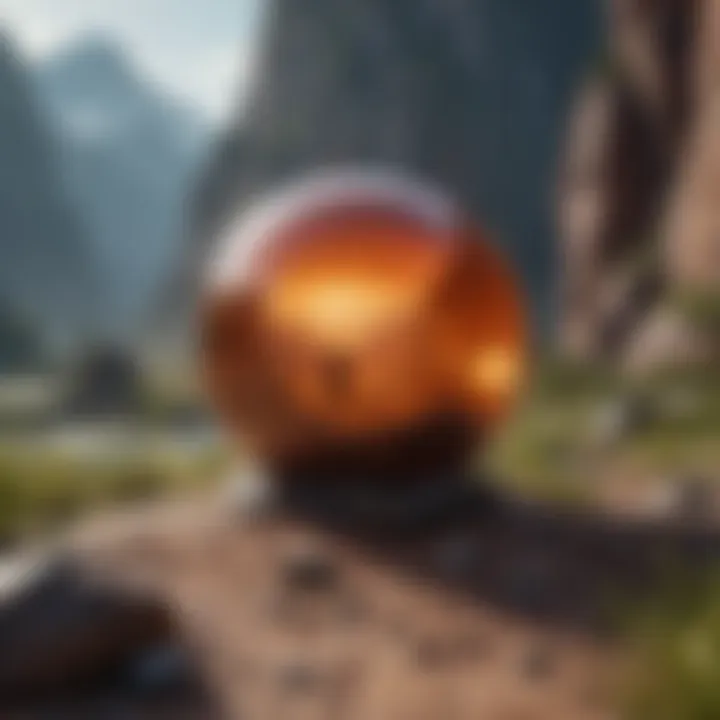
Intro
The landscape of 3D printing has seen significant evolution in recent years, particularly when it comes to large-scale objects. The intersection of technology and creativity has enabled industries to explore new avenues for design and manufacturing. In this article, we will investigate several key themes, including methodologies, materials, applications, and the unique challenges faced in the realm of large object 3D printing.
Methodology
Overview of Research Methods Used
To analyze the complexities associated with large-object 3D printing, a multi-faceted research approach is essential. This includes both qualitative and quantitative methods, enabling a comprehensive examination of current practices. Surveys and interviews with industry experts help to gather firsthand insights. Additionally, literature reviews of academic and industry publications form the backbone of our understanding.
Data Collection Techniques
Detailed data collection is critical for a robust analysis. Various techniques are employed:
- Surveys: These gauge the perceptions and experiences of professionals in the field.
- Interviews: Engaging in one-on-one discussions with pioneers provides depth and context.
- Case Studies: Examining real-world applications of large-scale 3D printing allows for practical insights into its efficacy.
Research in 3D printing technology not only identifies existing innovations but also pinpoints gaps in knowledge and opportunity for further growth.
Challenges in Large Object 3D Printing
One significant aspect worth discussing is the hurdles that practitioners encounter in this domain. The constraints could range from limitations in material properties to the technological capabilities of current 3D printing machines. It is important to understand these challenges to appreciate the innovations arising from the field.
Future Directions
Upcoming Trends in Research
Looking ahead, several trends are shaping the future of large-object 3D printing. These include:
- Advancements in Materials: New materials that can withstand greater stress and environmental challenges.
- Automation and AI: Integrating artificial intelligence to enhance printing accuracy and efficiency.
- Sustainability: A shift towards more eco-friendly materials and processes is anticipated.
Areas Requiring Further Investigation
While progress is evident, further investigation is necessary in various areas:
- Standardization of Practices: Developing industry standards to ensure quality and reliability.
- Interdisciplinary Research: Encouraging collaboration between fields like engineering, materials science, and design.
Prelude to 3D Printing
3D printing represents a pivotal shift in manufacturing and design, impacting various industries including aerospace, automotive, and healthcare. This technology has enabled the creation of complex geometries and structures that were once thought impossible. In this article, we will explore the significant role that 3D printing plays in the context of large-scale objects. The ability to produce sizable items opens up a plethora of applications and possibilities.
A core element of 3D printing is its ability to reduce lead times. In traditional manufacturing, producing large objects often requires extensive tooling and setup, which can take considerable time and resources. 3D printing, on the other hand, streamlines this process. It allows for rapid prototyping and production by simply altering a digital model. This efficiency is particularly valuable in industries that require customization to meet specific needs.
Moreover, 3D printing promotes sustainability in production. Large-scale printing can minimize material waste, as it uses only the necessary amount of material required for creating the object. This contrasts sharply with subtractive manufacturing techniques, which often generate significant waste during production.
As we delve into the specifics of large-scale 3D printing, it is essential to understand the foundational aspects of this technology.
Definition and Overview
3D printing, often referred to as additive manufacturing, is the process of creating three-dimensional objects from a digital file. The technology involves layering materials to build a product from the ground up. This technique contrasts with traditional manufacturing, which typically involves cutting away material to achieve the desired shape.
Materials used in 3D printing can vary widely, from plastics like PLA and ABS to metals and ceramics. The choice of material impacts the final object's properties, including strength, durability, and thermal resistance.
The transition from concept to reality in 3D printing is primarily achieved through Computer-Aided Design (CAD) software. Users can design a model, which is then sliced into layers to guide the printing process. This level of precision allows for intricate designs that may not be feasible with conventional methods.
Historical Evolution of 3D Printing Technologies
The history of 3D printing can be traced back to the 1980s when Chuck Hull invented Stereolithography (SLA). This revolutionary technique laid the groundwork for what we now understand as additive manufacturing. Initially, the technology found its place in rapid prototyping, allowing companies to create physical models from digital designs quickly.
Since the inception of SLA, numerous advancements have occurred. Fused Deposition Modeling (FDM) emerged in the 1990s, making 3D printing more accessible to hobbyists and small businesses. FDM operates by extruding thermoplastic materials through a heated nozzle, building objects layer by layer.
Over the years, the spectrum of 3D printing technologies has expanded to include methods such as Selective Laser Sintering (SLS), which uses lasers to fuse powdered materials, and Binder Jetting, which employs a liquid binder to bond powder together. These innovations have diversified the applications of 3D printing, enabling its integration into sectors like medicine for custom implants and the automotive industry for prototype parts.
Understanding the evolution of 3D printing technologies not only highlights their unique characteristics but also points to a future where large-scale 3D printing could become standard practice across product development processes.
"As 3D printing continues to advance, its potential applications are limited only by our imagination."
Large Scale 3D Printing Explained
Large scale 3D printing represents a significant leap in manufacturing and design capabilities. This technique allows for the production of objects considerably larger than traditional methods. The ability to produce larger items has practical implications across various industries, from construction to aerospace. One notable benefit is the capability to create complex geometries that were previously impossible with conventional manufacturing. These advancements can lead to innovative designs and functional improvements.
As industries evolve, the demand for custom solutions increases. Large-scale 3D printing provides the flexibility needed to create tailored products efficiently. It can significantly reduce lead times, allowing businesses to respond quickly to changing market demands. However, this method does have its considerations regarding cost, technology readiness, and material suitability.
Specifics of Large Objects
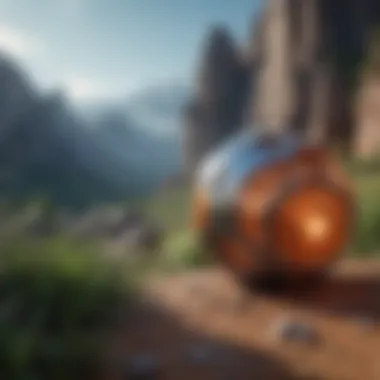
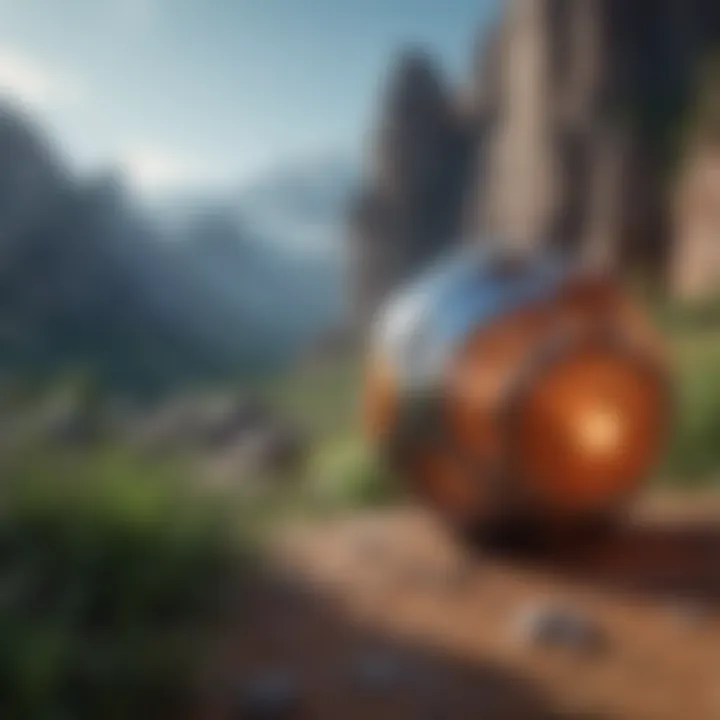
Large objects in 3D printing require specialized technologies and approaches. The size increases the challenges faced during production. Stability and precision become critical factors. For instance, large prints may be more susceptible to warping and other defects, which can compromise the final product. Moreover, the printing process must be carefully controlled to ensure uniform layer adhesion and structural integrity.
Printing larger items also requires a consideration of the materials used. Many materials suitable for smaller prints may not perform well at scale. Therefore, selecting the appropriate material is key to achieving the desired strength and durability. Efficient management of printing time and resources, alongside optimized designs, is crucial in this area.
Comparative Analysis of Different Printing Techniques
Fused Deposition Modeling (FDM)
Fused Deposition Modeling is one of the most widely used techniques in 3D printing. It involves the extrusion of heated thermoplastic filament through a nozzle, layer by layer. A distinctive aspect of FDM is its accessibility, making it a popular choice for both large and small-scale projects. The technique is notable for its affordability and ease of use.
Pros of FDM:
- Low material cost
- Wide selection of filament types
- Good for prototyping.
Cons of FDM:
- Limited resolution compared to other methods
- May require post-processing for optimal finish.
Stereolithography (SLA)
Stereolithography utilizes a laser to cure liquid resin into solid parts. This method is appreciated for its high precision and ability to produce intricate details. SLA is ideal for applications requiring smooth surfaces and complex geometries.
Pros of SLA:
- High accuracy and detail
- Smooth finishes without extensive post-processing.
Cons of SLA:
- More expensive compared to FDM
- Limited to resin materials which may require special handling.
Selective Laser Sintering (SLS)
Selective Laser Sintering employs a laser to fuse powdered material, layer by layer, into a solid object. This technique is especially valuable for producing functional parts and complex geometries that are difficult to achieve with other methods. SLS enables the use of a diverse range of materials, including plastics and metals.
Pros of SLS:
- Strong mechanical properties
- No need for support structures
- Suitable for end-use parts.
Cons of SLS:
- Higher costs
- More complex setup and operation.
In summary, large scale 3D printing is at the forefront of manufacturing innovation. Each technique has its unique characteristics, influencing the choice of method based on project needs.
Materials Used in Large-scale 3D Printing
Materials play a crucial role in the field of large-scale 3D printing. Selecting the right material influences the quality, strength, and potential applications of printed objects. As industries increasingly adopt 3D printing, understanding the benefits and considerations regarding different materials is essential. This section’s focus is on both common materials used and newer innovations, showcasing the vast potential of 3D printing.
Common Materials Employed
Engineering Plastics
Engineering plastics are among the most preferred materials in large-scale 3D printing. They offer a unique combination of strength, flexibility, and resistance to chemical impacts. The most common types include ABS, PLA, and PETG. The high durability of engineering plastics makes them particularly beneficial for functional prototypes and end-use parts.
One key characteristic of engineering plastics is their ability to be easily processed and molded into intricate shapes, a necessity for large objects. This feature greatly enhances design freedom. However, while engineering plastics are versatile, they can be less environmentally stable. Some may degrade under the influence of UV light or high temperatures, which can limit their applications.
Metals
Metal materials like aluminum, titanium, and stainless steel have significantly impacted large-scale 3D printing. They are commonly used in industries such as aerospace and automotive for their outstanding strength-to-weight ratios. The distinct property of metals is their thermal conductivity, which allows for effective heat dissipation in demanding applications.
Metals are a formidable choice for structural components due to their resilience. However, the high cost of metal powders and the complex post-processing requirements can pose dual challenges. These factors make metals both advantageous and limiting in certain contexts related to large-scale 3D printing.
Composites
Composite materials are another critical aspect of large-scale 3D printing. They combine two or more materials to create properties not found in a single material alone. For instance, carbon fiber composites provide exceptional stiffness while remaining lightweight.
The key benefit of using composites is their ability to enhance strength while reducing weight, making them crucial for industries that prioritize efficiency. Nonetheless, the complexity in processing composites can pose challenges for printers, requiring advanced equipment and knowledge. Despite the hurdles, composites offer significant potential in advancing large-scale 3D printing.
Innovative Material Advancements
Biodegradable Plastics
The rise of biodegradable plastics marks a significant development in large-scale 3D printing. Made from renewable resources, these materials break down naturally over time. This aspect is particularly valuable in combating environmental challenges associated with conventional plastics.
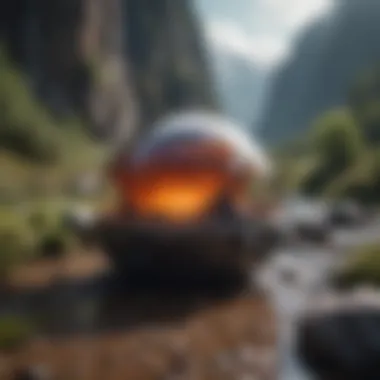

Biodegradable plastics are popular for their eco-friendly attributes. However, they also come with limitations. For example, they may not offer the same strength or durability as traditional plastics, which can restrict their usability in certain applications.
High-Temperature Materials
High-temperature materials have emerged as indispensable in sectors requiring thermal resilience. Materials like PEEK and ULTEM can withstand extreme conditions without compromising performance. This feature is essential in industries such as aerospace and automotive.
These materials are beneficial because they expand the range of potential applications for large-scale 3D printing. However, high-cost and the need for specialized printing conditions are significant barriers to widespread adoption.
Smart Materials
Smart materials offer exciting possibilities in large-scale 3D printing. These materials can respond to environmental changes, leading to applications in various fields, including robotics and medical devices.
The versatility of smart materials is a key attraction. However, the complexity involved in their manufacturing process can limit accessibility. Understanding how to effectively incorporate these materials can open new doors to innovative products.
Applications of Large Object 3D Printing
The field of large object 3D printing is rapidly expanding, making significant impacts across various sectors. The applications of this technology are not just innovative; they are transformative. By examining the following sectors, one can appreciate how 3D printing alters conventional processes, enhances efficiency, and opens new avenues for design and functionality.
In essence, applications in different industries showcase the versatility and potential of large-scale printing, leading to improvements in production quality and speed. Furthermore, the ability to create customized solutions fosters creativity and pushes the boundaries of traditional manufacturing
Construction Industry
In the construction industry, large object 3D printing is reshaping how structures are designed and built. The adoption of this technology allows for faster construction timelines and reduced labor costs. For instance, large-scale printers can fabricate entire building components, such as wall panels and even house foundations, using materials like concrete.
This method not only simplifies the construction process but also allows for intricate designs that might be challenging to achieve with traditional methods. Projects such as the 3D-printed homes developed by ICON illustrate the potential of this technology. These homes can be constructed in just days and are environmentally friendly, reducing waste compared to conventional building techniques.
Key benefits include:
- Speed: Structures can be printed significantly faster, addressing urgent housing needs.
- Cost Reduction: Reduced material waste and labor costs lead to economic advantages.
- Design Flexibility: Architects have the freedom to realize designs that traditional construction cannot accommodate.
Aerospace and Automotive Sectors
Aerospace and automotive industries can greatly benefit from large object 3D printing. By utilizing this technology, companies can create complex components that are lightweight yet strong. This is crucial in industries where every gram can impact performance and fuel efficiency.
For example, aerospace manufacturers are using 3D printing to produce parts for aircraft engines. These components can be optimized for performance while minimizing weight. The General Electric's LEAP engine showcases how metal additive manufacturing enables the production of intricate and high-performance components.
Key advantages for aerospace and automotive applications include:
- Weight Reduction: Lighter parts can lead to improved fuel efficiency.
- Part Consolidation: Traditional assembly can be simplified, as fewer components are needed.
- Rapid Prototyping: Quickly create prototypes to test designs before mass production.
Art and Design
The intersection of 3D printing and artistry is particularly exciting. Artists and designers are embracing large object 3D printing to explore new creative avenues. This technology enables the creation of larger sculptures and installations that were previously impractical to produce.
By utilizing various materials, artists can experiment with scale, shape, and texture in their work. Large-format printers can handle unique materials, contributing further to creative possibilities.
Notable projects include large-scale installations showcased at art museums and galleries. These works spark dialogue about creativity, technology, and the future of art. Benefits in this sector include:
- Creative Freedom: Artists can materialize their most ambitious concepts.
- Customization: Unique pieces can be produced without the constraints of traditional methods.
- Innovation: The blending of art and technology encourages new forms and styles.
"3D printing is not just about creating objects; it’s about redefining the artistic process itself."
Advantages of 3D Printing Large Objects
3D printing large objects not only alters the way products are manufactured, but also brings several strategic advantages that are shaping industries today. The potential for cost efficiencies, customization, and the reduction of material waste are critical factors that underline the significance of this technology. Each of these advantages plays a pivotal role in making large-scale 3D printing an appealing option for many sectors.
Cost Efficiency
The cost efficiency that arises from 3D printing large objects stems from multiple facets. Traditional manufacturing methods often involve complex procedures that require significant labor, time, and overhead costs. In contrast, 3D printing offers a streamlined production process that can cut down on these expenses.
For instance, once a digital model is created, it can be printed multiple times with minimal additional costs. This reduces the expenses associated with tooling or molds, which are typically necessary in conventional manufacturing. Additionally, maintenance costs can be lower since there are fewer machines involved in the process. Moreover, companies can reduce storage costs. 3D printing facilitates on-demand production, eliminating the need to maintain large inventories of products that may not sell.
Another consideration is energy consumption. 3D printing can often use less energy compared to traditional methods, resulting in lower utility bills. This aspect is especially significant in large production runs, where the cumulative savings become substantial.
Customization Capabilities
One of the most notable advantages of large-scale 3D printing is its ability to facilitate customization. Tailoring products to meet the specific needs or preferences of consumers has become increasingly popular across various industries. 3D printing technologies enable manufacturers to create highly individualized products without the complications typically associated with custom production.
This customizability is particularly evident in sectors like healthcare, where prosthetics and implants can be designed to fit the exact specifications of a patient’s anatomy. In the automotive industry, personalized designs for fittings and components can easily be produced.
Moreover, the iterative design process in 3D printing allows for rapid prototyping, where modifications can be applied to a design and tested almost instantly. This flexibility significantly shortens the time from concept to production, enabling companies to respond swiftly to market changes or customer demands.
Reduction of Material Waste
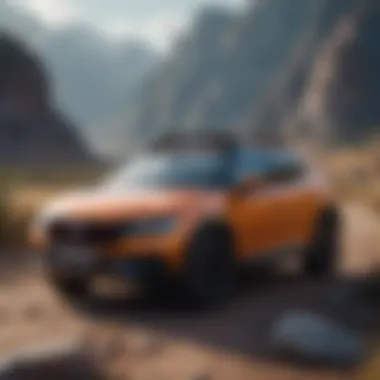
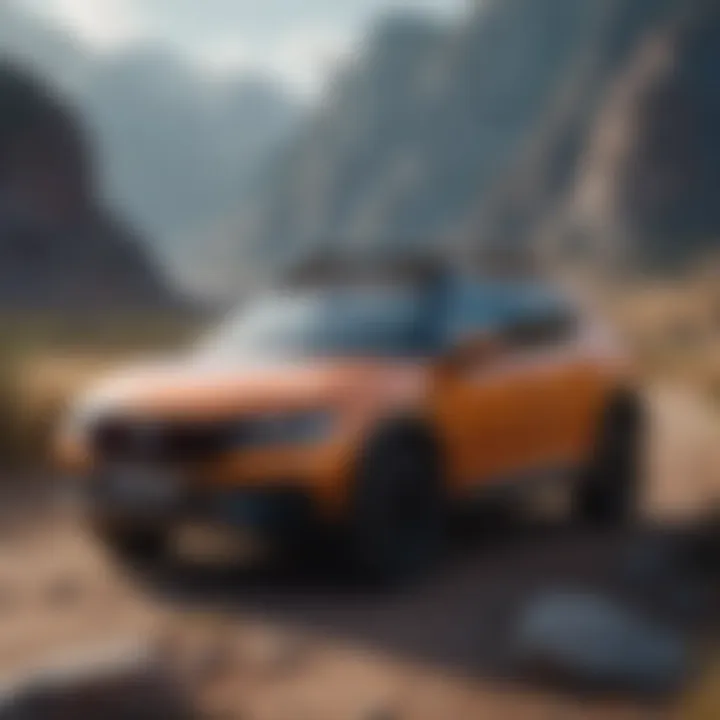
Large-scale 3D printing considerably reduces material waste compared to traditional subtractive manufacturing methods. Conventional processes often involve cutting away from larger blocks of material, generating scraps that are discarded. This not only wastes resources, but also incurs additional costs associated with disposal and recycling.
In contrast, additive manufacturing, which is at the core of 3D printing, involves building up layers of material, thereby creating objects only as needed. This technique dramatically minimizes waste because only the necessary amount of material is used to produce the final object.
Furthermore, advancements in material science are leading to the development of new biodegradable and recyclable materials specifically designed for 3D printing. This evolution not only conserves resources but also aligns with global efforts towards sustainability, making large-scale 3D printing a more eco-friendly approach to manufacturing.
"The integration of cost efficiency, advanced customization, and reduced material waste positions 3D printing as a frontrunner in reshaping modern manufacturing practices."
Challenges Faced in Large-scale 3D Printing
The ongoing evolution of large-scale 3D printing presents numerous obstacles. Understanding these challenges is critical for those engaging with this technology. Various factors may impede the advancement and adoption of large object 3D printing. Addressing them ensures project success and drives broader acceptance in different industries.
Technical Limitations
Technical limitations remain a significant hurdle for large-scale 3D printing. Notably, the size of the print bed and related machinery restricts the dimensions of printed objects. Most printers currently available have size constraints. Additionally, some materials can only be processed at certain scales or speeds.
Another consideration is print resolution and layer adhesion. For large prints, achieving good surface quality can be challenging. As the size of the object increases, the likelihood of imperfections and warping also rises. The thermal properties of the materials can result in uneven cooling, leading to dimensional inaccuracies.
Aspects like technology reliability can also affect productivity. Equipment failures during long print jobs can lead to wasted time and resources, thereby increasing costs. To mitigate these issues, research into advanced printing techniques and materials continues. But challenges persist.
Regulatory and Compliance Issues
Regulatory and compliance issues introduce complexities in the large-scale 3D printing space. Various industries have specific regulations. For example, in aerospace and healthcare, safety is paramount.
These sectors require rigorous testing and certification processes for any components made through additive manufacturing. The intricate nature of large-scale 3D printing often makes it difficult to ensure compliance. Manufacturers must navigate the existing regulatory landscape to avoid violations. This can require significant time and investment.
Moreover, countries may have different regulations regarding material use and manufacturing processes. International collaborations can further complicate compliance efforts. Therefore, companies in this field must be well-informed on local and global standards. Adherence to regulations is crucial for market entry and operational viability.
Market Acceptance and Perception
Market acceptance and perception heavily influence the expansion of large-scale 3D printing. Many potential users remain skeptical about the capabilities and benefits of this technology. This skepticism can stem from a lack of understanding or knowledge about how 3D printing works.
Companies may hesitate to invest in large-scale solutions due to concerns over reliability and quality. The stigma that 3D printing primarily serves prototyping rather than full-scale production lingers. Consequently, industries may be slow to transition from traditional manufacturing methods to additive ones.
Educating stakeholders about the advantages and potential of large-scale 3D printing is essential. As awareness increases, so does the likelihood of broader acceptance. Ultimately, overcoming these perceptions is vital for fostering innovation and exploring new applications in various fields.
"Addressing the challenges of large-scale 3D printing is crucial for its growth and integration into mainstream industries." - Industry Expert
The landscape of large-scale 3D printing is ever-changing. Each of these challenges presents unique considerations that must be navigated for successful implementation. Tackling technical limitations, understanding regulatory requirements, and positively influencing market perception are key to ensuring the effective use of this revolutionary technology.
Future Trends in Large Object 3D Printing
The future of large-scale 3D printing is promising and full of innovative possibilities. As technology advances, various sectors are poised to benefit from emerging trends in this field. Understanding these trends is vital for researchers, students, and industry professionals keen on harnessing the full potential of 3D printing. The importance of future trends lies in their ability to shape manufacturing methods, improve sustainability, and enable interdisciplinary collaboration that factors in diverse fields.
Emerging Technologies
New technologies are revolutionizing the landscape of large-object 3D printing. Companies are investing heavily in research and development to create devices that enhance efficiency and precision. One key trend is the use of multi-material printing, where a single printer can process different types of materials simultaneously. This innovation could lead to more complex designs and functional prototypes.
Moreover, advancements in artificial intelligence (AI) are enabling smarter printing processes. AI can optimize designs, predict errors, and improve overall print quality. Another emerging technology is the integration of robotics in 3D printing. Automated systems can handle larger objects more effectively, significantly reducing the time and labor needed for production.
Sustainability Practices
Sustainability is increasingly becoming a vital consideration in manufacturing processes, including 3D printing. The rise in consumer demand for eco-friendly products is pushing companies to adopt sustainable practices. Large-object 3D printing supports these efforts through techniques that minimize waste and utilize recycled materials. This is crucial as industries aim to meet stricter environmental regulations.
Additionally, some innovators explore bio-based materials that offer compatibility with large-scale printing. These materials are sourced from renewable resources, which contribute to reducing the carbon footprint. Companies can also adopt local production strategies, significantly cutting down on transportation emissions and promoting a circular economy.
Interdisciplinary Collaborations
Collaboration across disciplines is integral to advancing large-object 3D printing. When engineers, designers, and scientists work together, they can exchange knowledge and develop solutions that meet various challenges. For instance, architects collaborating with material scientists can create structures that blend aesthetic appeal with the latest material advancements, maximizing both function and sustainability.
Higher education institutions are increasingly recognizing the value of these collaborations. Many programs now promote hands-on learning experiences that connect students to industry partners. This prepares graduates to contribute effectively in settings where multiple fields intersect, thus fostering innovation and enhancing competitiveness in the field of large-object 3D printing.
"As 3D printing technology continues to evolve, the interplay between technology, sustainability, and interdisciplinary effort is crucial to unlocking its full potential in the manufacturing domain."
Epilogue
The conclusion serves as a vital element of this article, allowing for the synthesis of insights gained throughout the exploration of large-scale 3D printing. This section is essential for reinforcing the main arguments and concepts presented in previous sections, fostering a deeper understanding of the implications and future possibilities of this technology.
Summary of Key Points
Reflecting on the various facets of large-object 3D printing, there are several key points to consider:
- Technological Progress: We have examined the evolution of 3D printing technologies, noting significant advancements in methods like Fused Deposition Modeling, Stereolithography, and Selective Laser Sintering.
- Material Variety: The discussion on materials highlighted the versatility of options such as engineering plastics, metals, and innovative biodegradable substances. Each type brings distinct advantages to various applications.
- Real-World Applications: Industries like construction, aerospace, and art have embraced large-object 3D printing, aiding in both cost-efficiency and customization.
- Current Challenges: The technical limitations and regulatory issues posed challenges that need continued attention for the industry to thrive.
- Future Directions: The article elaborated on emerging technologies, sustainability practices, and the importance of interdisciplinary collaboration, suggesting a vibrant future for large-scale 3D printing.
This summary encapsulates the critical insights that outline the landscape of 3D printing for large objects, emphasizing its importance in advancing design and manufacturing methodologies.
Final Thoughts on the Impact of 3D Printing
The impact of 3D printing extends beyond mere technological innovation. It reshapes the way industries approach design, manufacturing, and even sustainability. The ability to create large objects on demand streamlines supply chains and reduces waste, which is increasingly essential in today’s eco-conscious market.
Moreover, 3D printing fosters a new era of customization. This was particularly evident in sectors like art and design where unique creations are highly valued. In construction, the integration of this technology results in faster project timelines and potentially significant cost reductions. These factors contribute to broader changes, influencing market dynamics and consumer expectations.