3D Printer Material Strength: An In-Depth Analysis
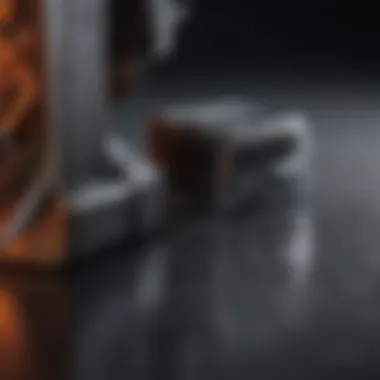
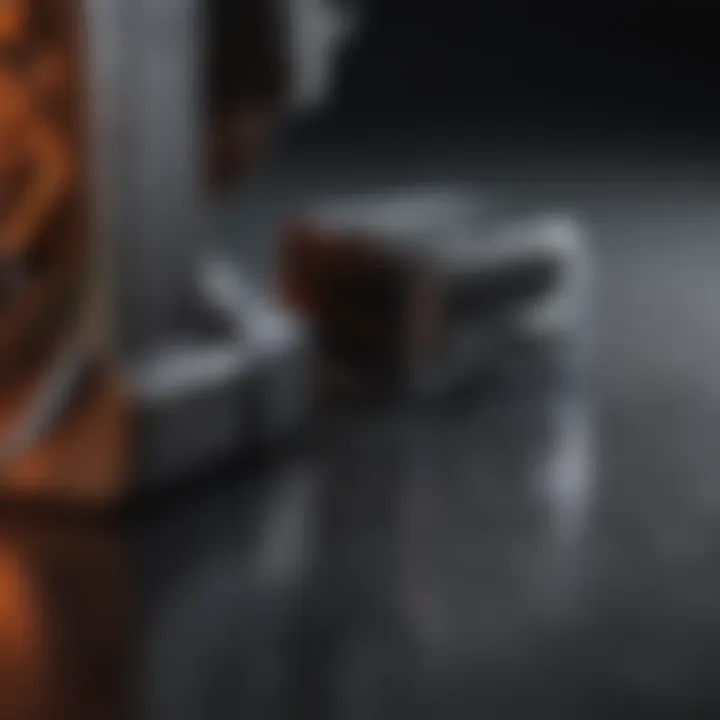
Intro
The world of 3D printing is rapidly evolving, with innovations in materials continuously reshaping what is possible. Understanding material strength is crucial for anyone involved in additive manufacturing, whether it be students, researchers, or professionals. Material strength encompasses various mechanical properties that influence the performance and usability of printed parts. This article aims to explore the critical aspects of material strength in 3D printing, focusing on the interplay between different materials and their attributes.
As industries embrace the possibilities of 3D printing, suffice to say, proper material selection becomes paramount. This leads to a quest for deeper knowledge about factors such as tensile strength, impact resistance, and other relevant mechanical properties. Knowing how to measure these factors can greatly influence the success of a project, considering specific application needs.
By delving into the complexities surrounding material strength, we can better understand the implications for various applications in fields like aerospace, automotive, and biomedicine. Each industry may demand unique characteristics from 3D printed materials, which drives the need to scrutinize what is available and what might be developed in the future.
Methodology
Overview of research methods used
A combination of qualitative and quantitative research methods was employed to analyze material strength in 3D printing. This dual approach facilitates a comprehensive understanding of existing materials and their properties.
Interviewing experts in materials science provided valuable insights on current trends and areas needing exploration. The inclusion of academic papers, industry reports, and case studies reinforced the data collected. Moreover, a meticulous review of recent advancements in material technology was performed to update the findings.
Data collection techniques
Data collection was performed using several techniques:
- Literature Review: Comprehensive reviews of academic journals and articles helped identify key theories and principles related to material strength.
- Expert Interviews: Conversations with materials scientists and industry professionals provided first-hand knowledge on practical applications.
- Case Studies: The investigation of successful 3D printing projects provided practical examples of material strength in action.
The synthesis of these various methods allows us to paint a clearer picture of material strength's role in 3D printing and its future trajectory.
Future Directions
Upcoming trends in research
One remarkable trend is the ongoing exploration of bio-based materials for 3D printing. These materials promise various advantages, including sustainability and customizability, thus appealing to environmentally conscious sectors. Research into composites is also gaining attention, combining different materials to achieve enhanced properties, thus opening doors to new applications.
Areas requiring further investigation
While significant strides have been made, several areas still need more focused investigation:
- Impact of Temperature Variations: Understanding how temperature fluctuations affect material properties during the printing process is essential for optimizing performance.
- Durability Testing: Long-term studies on the durability of printed parts can provide critical data for industries relying on 3D printing for functional products.
Prelude to 3D Printing
The realm of 3D printing has gained significant traction in recent decades, transforming various industries by enabling rapid prototyping, custom manufacturing, and innovative design processes. Understanding this technology is crucial not only for professionals directly involved in additive manufacturing but also for students and educators who are shaping the future of this field. The selection of materials plays a pivotal role in the effectiveness of 3D printing. By grasping the foundational elements of 3D printing, such as its evolution and significance of material choice, one can better appreciate the ongoing advancements in this technology.
Definition and Evolution of 3D Printing
3D printing, also known as additive manufacturing, is a process that creates three-dimensional objects by layering materials based on digital models. The concept has roots that extend back to the 1980s, when Charles Hull invented stereolithography, the first 3D printing technology. Since its inception, the field has evolved rapidly, expanding in both technique and application.
Initially, 3D printing was primarily used for prototyping in product development, allowing for faster iterations and modifications. The broadened range of materials, designs, and processes has allowed industries from aerospace to healthcare to harness the benefits of additive manufacturing.
Various technologies, including fused deposition modeling (FDM), selective laser sintering (SLS), and polyjet printing, enhance the capabilities of 3D printing. Each process has unique strengths that influence the material properties and overall performance of the final product.
Importance of Material Selection
Material selection is vitally important in 3D printing. The chosen material directly impacts the final product's strength, flexibility, durability, and suitability for specific applications. For instance, materials such as polylactic acid (PLA) are popular for their ease of use and biodegradability, while nylon is favored for its strength and resistance to wear.
Critical factors to consider when selecting materials include:
- Mechanical properties: Tensile strength, durability, and temperature resistance
- Cost-effectiveness: Availability and pricing of the material
- Application compatibility: Suitability for intended use and performance requirements
Adopting appropriate materials ensures that the resulting objects meet the performance criteria necessary for their respective applications. Therefore, understanding the implications of material choice is integral to a successful 3D printing project.
Understanding Material Strength
Understanding material strength is a pivotal aspect in the realm of 3D printing. It provides insights into how well a printed object can withstand various forces during its intended use. This knowledge is essential for several reasons. First, it guides designers and engineers in selecting suitable materials that can endure specific applications. Second, it shines a light on the mechanical properties that dictate the durability and functionality of the final products. Identifying how these factors interconnect allows for optimizing the 3D printing process to achieve desired outcomes in functionality and longevity.
Moreover, understanding material strength empowers professionals across industries to make informed decisions. Knowledge in this area yields significant advantages, such as lowering material waste, improving product quality, and enhancing safety. With the right understanding, one can appreciate the complexities involved in creating reliable, resilient, and robust 3D-printed parts.
Definition of Material Strength
Material strength is defined as the ability of a material to withstand an applied load without failure or plastic deformation. This characteristic varies significantly among different materials. Understanding this concept is particularly vital for 3D printing, where materials undergo various stresses based on their intended use. Knowledge of material strength assists in predicting how a print will behave under different conditions.
Key Mechanical Properties
The key mechanical properties that define the strength of a material include tensile strength, compressive strength, and flexural strength. Each of these properties has unique implications for the performance and application of 3D printed materials.
Tensile Strength
Tensile strength refers to the maximum amount of tensile (pulling) stress that a material can withstand before failure. It is a critical factor in applications where the printed part will experience stretching or pulling forces. High tensile strength is particularly valued in structural applications because it ensures that components can endure significant loads without breaking. For instance, materials like Nylon exhibit excellent tensile strength, making them suitable for mechanical parts that require durability. However, this strength can vary based on print quality and orientation, which are important considerations during the design phase.
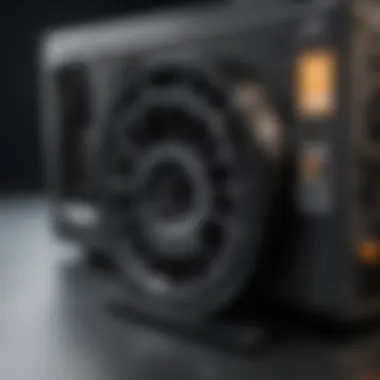
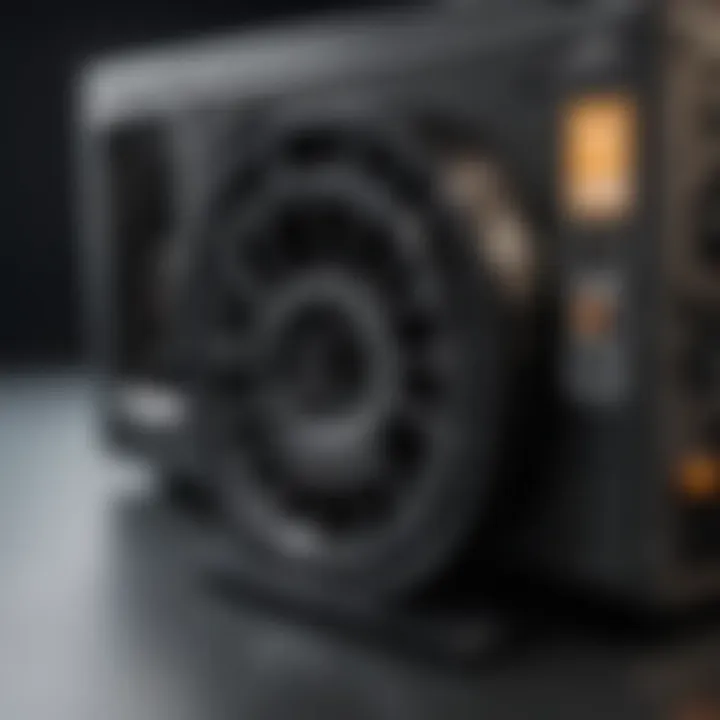
Compressive Strength
Compressive strength is the measure of a material's ability to withstand axial loads without being crushed or deformed. This property is essential for designs that must support loads from above, such as bases or supports in larger structures. In 3D printing, materials like concrete composites are often selected for their high compressive strength, which is beneficial in construction applications. Understanding the limitations of compressive strength helps avoid structural failures in weight-bearing components, ensuring safety and stability in various applications.
Flexural Strength
Flexural strength, or the ability of a material to resist deformation under load, is critical in applications where parts are subject to bending or flexing stresses. This property is particularly relevant for brackets, beams, and many other parts that must maintain their shape under various forces. Certain thermoplastics, such as ABS, are recognized for their good flexural strength, making them ideal choices for diverse applications that demand durability and resistance to bending. Identifying the appropriate flexural strength helps in designing prints that can bear specific loads without permanent deformation.
Understanding these mechanical properties is vital for optimizing 3D printing processes and ensuring that the final product meets the necessary functional requirements. By carefully selecting materials based on tensile, compressive, and flexural strengths, engineers and designers can achieve superior results that align with the demands of their projects.
Common 3D Printing Materials
Understanding the range of materials available for 3D printing is essential. Various materials offer different properties, allowing designers and engineers to choose those best suited for their specific applications. These materials can be categorized primarily into thermoplastics, metals, composites, and specialty materials. Each category brings something unique to the table. Along with that, their mechanical properties can greatly influence the effectiveness of the final product. Selecting the right material is a key part of achieving desired strength and durability. Therefore, exploring common materials reveals not only their characteristics but also their practical applications in different industries.
Thermoplastics
Thermoplastics are among the most widely used materials in 3D printing due to their versatility and ease of use. They are characterized by their ability to become moldable when heated and solidify upon cooling. This property allows for the creation of intricate designs and robust structures. The most popular thermoplastics include PLA, ABS, and Nylon.
PLA
PLA, or Polylactic Acid, is a biodegradable thermoplastic derived from renewable resources like corn starch or sugarcane. Its key characteristics include low shrinkage and warp resistance. PLA is popular for its ease of printing and decent strength, making it a go-to material in the consumer 3D printing marketplaces. Its unique ability to print at lower temperatures means less energy consumption, which is an advantage in many applications.
However, PLA does have disadvantages. It can be more brittle compared to other materials, which limits its use in applications requiring high durability or impact resistance. Overall, PLA is excellent for prototypes or decorative models but not suitable for functional parts in demanding conditions.
ABS
Acrylonitrile Butadiene Styrene, commonly known as ABS, is another prevalent thermoplastic in 3D printing. Its key feature is its superior toughness and ability to withstand higher temperatures. ABS prints can be finished smoothly for aesthetics, making it suitable for functional parts and engineering applications.
This material’s strength-to-weight ratio is an advantage, allowing for the production of lightweight yet strong pieces. On the downside, ABS can emit unpleasant fumes during printing and is prone to warping if not managed properly. Therefore, while it is effective in many scenarios, care is needed during the printing process to avoid these issues.
Nylon
Nylon is known for its high strength, flexibility, and impact resistance, making it ideal for functional parts that need durability. Its key characteristic is its excellent fatigue resistance, meaning it can endure repeated stress without failure. Nylon is often used in applications like gears, bearings, and other mechanical components.
The unique feature of Nylon is its hygroscopic nature, which means it absorbs moisture from the air. This can compromise the strength and quality of printed parts if not stored correctly. Consequently, while Nylon offers significant advantages in terms of strength and resilience, users must consider its moisture sensitivity carefully.
Metals
Metal 3D printing materials offer significant advantages, particularly in strength and durability. Stainless Steel, Aluminum, and Bronze are commonly used, each providing distinct benefits suitable for various applications.
Stainless Steel
Stainless Steel is often favored for its exceptional strength and corrosion resistance. It plays a crucial role in engineering applications where durability is paramount. Its key characteristic is resistance to rust and staining, which allows stainless steel parts to maintain integrity in harsh environments.
This material’s unique feature is its ability to be welded easily. This aids in post-processing, where separate parts can be seamlessly combined. However, the printing process can be complex and requires precise conditions to prevent defects.
Aluminum
Aluminum is another metal widely used in 3D printing, especially for lightweight applications. Its key characteristic is its excellent strength-to-weight ratio, making it suitable for aerospace and automotive industries. The unique feature of Aluminum lies in its thermal conductivity, which helps in efficient heat dissipation.
On the downside, it can be more challenging to print than plastics due to its higher melting point. This may require specialized equipment and techniques, which can limit accessibility for some users.
Bronze
Bronze is a metal alloy that adds aesthetic value and strength to 3D printed parts. Its key characteristic is its resistance to wear and corrosion, making it a reliable choice for components exposed to harsh conditions. The unique feature of Bronze is that it can be polished to achieve a desirable finish, often utilized in art and decorative items.
However, it comes with added complexity during the printing process and can be more costly than other materials. Therefore, while bronze offers distinct advantages in many applications, careful consideration is required regarding cost and compatibility.
Composites
Composites combine the properties of different materials to achieve superior performance. Carbon Fiber Reinforced and Glass Fiber Reinforced composites are popular choices in specific applications requiring enhanced strength and stability.
Carbon Fiber Reinforced
Carbon Fiber Reinforced materials provide high strength and very low weight. Their key characteristic is stiffness, which allows parts to maintain shape under stress. This is beneficial in applications like aerospace and automotive, where weight reduction can significantly improve performance.
The unique feature of these composites is their ability to reduce vibration, making them ideal for moving components. However, they can be more expensive to print, and the print process might require specific considerations to prevent delamination.
Glass Fiber Reinforced
Glass Fiber Reinforced composites also offer an improvement in strength without a significant weight increase. They share a similar use case with carbon fiber variants but tend to be cheaper and easier to work with. Their key characteristic is decent impact resistance, allowing them to withstand mechanical stresses effectively.
However, they also have limitations. These materials can sometimes lead to brittle failures after a prolonged period, which makes constant monitoring necessary in critical applications.
Specialty Materials
Specialty materials, such as Flexible Filaments and Biocompatible Materials, cater to niche applications where standard materials may not suffice.
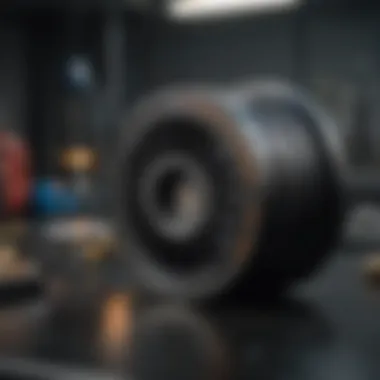
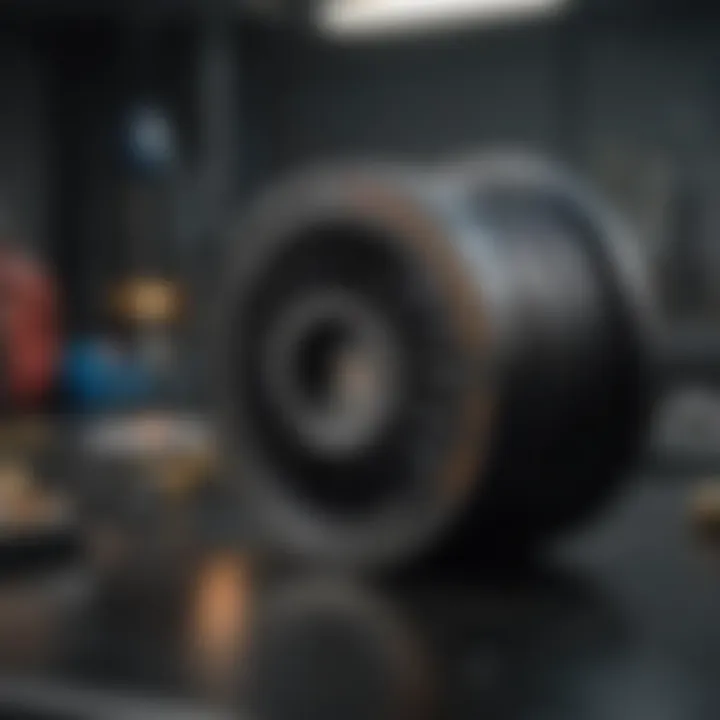
Flexible Filaments
Flexible Filaments enable the production of parts that can bend and stretch without breaking. Their key characteristic is elasticity, making them ideal for making soft, rubber-like products as gaskets or wearables. This unique feature allows for innovative design options in consumer products.
However, printing with these materials can be challenging. They require specific printer settings and may not work well in standard printers. This can limit their applicability for some users who cannot adjust their printing setups.
Biocompatible Materials
Biocompatible Materials are essential in medical applications, where safety and compatibility with living tissue are crucial. Their key characteristic is that they do not cause adverse reactions in the human body. This is vital in creating implants or prosthetics.
The unique feature of these materials is their ability to be sterilized, making them suitable for medical environments. On the downside, they often come at a higher cost than traditional materials, which can limit accessibility for research and development in some areas.
In summary, this section on common materials in 3D printing illustrates the breadth of choices available. Selecting the right material based on properties and applications is crucial for achieving optimal results.
Factors Influencing Material Strength
The strength of materials in 3D printing is not solely determined by the materials themselves. Various factors play a significant role in defining the final properties and usability of printed objects. Understanding these factors is crucial for optimizing output and enhancing performance. It also holds the potential for producing reliable prototypes and end-use products suited for specific applications.
Printing Parameters
Temperature
Temperature is a critical factor in additive manufacturing that affects the bond strength between layers. When materials are heated appropriately during printing, their thermoplastic properties come into play, allowing for effective layer adhesion. If the temperature is too low, inadequate flow may occur, leading to weak bonding. Conversely, excessive temperature can cause warping or degradation of materials.
Thus, finding the ideal temperature is essential. Where PLA usually prints around 180°C to 220°C, ABS requires higher temperatures, typically around 220°C to 260°C. This parameter's key characteristic is its direct influence on mechanical properties. Proper temperature control results in improved impact resistance and tensile strength, making it a beneficial choice for ensuring performance integrity.
Speed
Speed is another significant parameter that can influence material strength. It refers to how quickly the printer lays down the material during each pass. Higher speeds may lead to faster prints but can compromise the quality of layer adhesion. Insufficient time for layers to meld can result in weak points within the printed object. Therefore, it is often recommended to balance speed with the specific material used.
A typical print speed for PLA can range from 40 mm/s to 60 mm/s. The main focus here is on achieving an effective output without sacrificing essential strength characteristics. While faster prints are desirable, achieving this without compromising material performance is a challenge.
Layer Height
Layer height, which pertains to the thickness of each layer deposited during the printing process, also significantly impacts the final strength. A smaller layer height can improve surface finish and accuracy in details, leading to better overall strength. However, this often results in longer printing times. An optimal layer height may range from 0.1 mm to 0.3 mm depending on the material and object application.
This parameter's unique feature is how it interacts with other settings, such as speed and temperature, to influence structural integrity. While finer layer heights improve strength, they can also increase production time and resource consumption. Finding a middle ground is critical for practical usage in various applications.
Post-Processing Techniques
Sanding
Sanding is a commonly employed post-processing technique that enhances the surface finish of 3D printed parts. By smoothing out the outer layer, it can help reduce stress concentrations that may lead to failure under load. This practice can particularly benefit high-detail areas that require precision in form and aesthetics.
A key characteristic of sanding is its simplicity; it can be executed with basic tools. While it is not a drastic enhancer of strength, it can yield significant aesthetic improvements. However, excessive sanding may compromise the structural integrity if too much material is removed.
Annealing
Annealing involves heating the completed print to a temperature below the melting point, allowing the material to relieve internal stresses. This process is beneficial in improving the tensile strength and structural performance of many materials, especially those that are prone to warping. The primary objective of annealing is to enhance isotropy in materials, which contributes to uniform strength in varied directions.
The notable uniqueness of this technique lies in its ability to effectively target specific stress points without altering overall geometry. While it does require additional time and energy resources, the trade-offs often justify the improved material characteristics.
Coating
Coating serves as a means to enhance the properties of printed parts by adding a protective layer to the surface. Various coatings can protect against moisture, UV damage, or chemical exposure, thus prolonging the life of the printed object. It also provides an added layer of physical protection that can help shield from impact damage.
This process is particularly beneficial for applications where environmental endurance is crucial, which is evident in outdoor applications or where parts may be subjected to mechanical wear. However, selection of the right coating material is critical, as some may add weight or alter the printed object's thermal properties.
In summary, understanding factors influencing material strength such as printing parameters and post-processing techniques leads to improved results in 3D printing. Optimizing these elements can significantly enhance the performance and durability of printed products, thus broadening their application across industries.
Testing Material Strength
Testing material strength is a crucial element in understanding how different 3D printing materials perform under various conditions. This section covers the importance of standardized testing methods and how they help determine the usability of materials in practical applications. By employing these methods, researchers and manufacturers can ensure their printed products meet the required strength specifications. Knowing how materials hold up under different stresses is essential in fields such as aerospace and medical applications, where safety and reliability are paramount.
Standard Testing Methods
Standard testing methods provide a structured way to measure the strength of materials used in 3D printing. Various tests focus on different mechanical properties, which include tensile strength, impact resistance, and compressive strength. Each method has unique characteristics and serves specific purposes in evaluating material performance.
Tensile Testing
Tensile testing measures how a material reacts to being pulled apart. The key characteristic of tensile testing is its focus on the maximum amount of stretching a material can endure before it breaks. This method is a popular choice due to its straightforwardness and the clear relationship it establishes between different materials. A primary advantage of tensile testing is that it provides precise data about yield strength and elongation, which are critical for applications that require materials to manage forces effectively. However, tensile testing can require careful sample preparation to ensure accurate results.
Impact Testing
Impact testing evaluates a material's capability to withstand sudden forces or shocks. The primary feature of impact testing is the assessment of how energy is absorbed during a rapid impact. This method is valuable in applications where materials face unexpected loads or harsh environments. One notable advantage of impact testing is that it helps identify potential failure modes and can relate directly to real-world scenarios. On the downside, varying testing conditions can lead to inconsistent results, necessitating rigorous control over testing parameters.
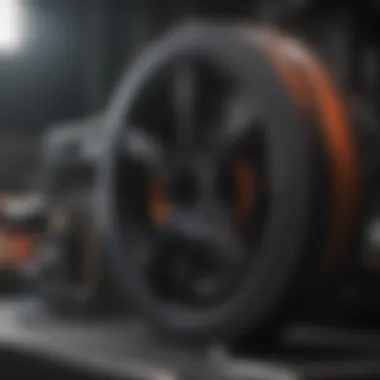
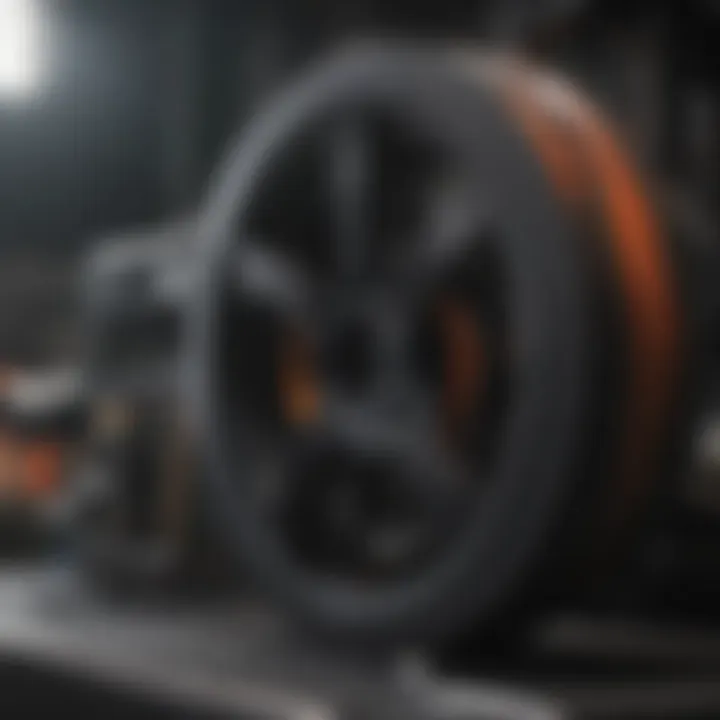
Compression Testing
Compression testing determines how materials react under compressive loads. The key aspect of this method is to evaluate the behavior of materials when forces press them together. Compression testing is particularly beneficial in applications where materials are subjected to heavy loads. One unique feature is that it simulates actual scenarios in construction and manufacturing where compressive forces are common. Nevertheless, compression testing may not provide complete information about tensile properties, which can limit a full understanding of the material's range of durability.
Evaluating Test Results
Evaluating test results is essential to interpret the data gathered from testing methods accurately. Each testing method yields data that reflect the intrinsic properties of the materials and their potential applications. When analyzing results, attention must be paid to the conditions under which the tests were conducted. Individual test outcomes can vary based on factors such as the temperature, rate of load application, and the specific geometry of the test specimen. By collating this information, professionals can draw informed conclusions about material suitability and safety in practical uses.
Proper evaluation techniques significantly enhance the reliability of test results and support informed decisions about material selection.
Applications of Strong Materials in 3D Printing
Strong materials play a critical role in the realm of 3D printing. Their applications extend across multiple fields, facilitating innovations and solutions that traditional manufacturing methods often can't achieve. This section delves into the significance of strong materials in various industries, emphasizing the benefits they bring and considerations to keep in mind. As 3D printing technology continues to evolve, understanding the applications of strong materials becomes essential for maximizing their potential.
Aerospace Industry
The aerospace sector stands as a prime example where strong materials are indispensable. Components made through 3D printing are increasingly favored due to their lightweight and high-strength properties. Aerospace engineers seek to reduce weight to improve fuel efficiency, and strong materials like titanium and high-grade polymers serve this purpose well.
- Weight Reduction: By employing strong lightweight materials, manufacturers can enhance fuel efficiency.
- Complex Geometries: 3D printing allows for intricate designs that are often not possible with traditional manufacturing methods.
- Customization: Custom parts can be produced in shorter timeframes, catering to specific needs of aircraft designs.
Overall, the use of strong materials in the aerospace industry not only helps in advancements in design but also aids in meeting strict regulatory standards, ensuring safety and reliability.
Medical Applications
In the medical field, strong materials provide vital solutions that enhance patient care and surgical outcomes. The ability to personalize medical devices and implants through 3D printing is revolutionary. Materials such as biocompatible titanium and specialized polymers are common because of their strength and compatibility with the human body.
- Customized Implants: Strong materials permit the production of tailored implants that fit perfectly to individual patient anatomy.
- Prosthetics: Strong, lightweight materials improve the comfort and functionality of prosthetic limbs.
- Surgical Tools: 3D printed tools made with strong materials demonstrate durability and precision, essential for complex surgeries.
By leveraging strong materials, the medical industry is pushing the boundaries of innovation, resulting in improved health outcomes and increased patient satisfaction.
Automotive Industry
The automotive sector is rapidly embracing 3D printing, driven by the desire for stronger, more resilient materials that reduce overall vehicle weight while enhancing performance. Strong materials in automotive applications lead to more efficient vehicle designs.
- Component Strength: High-strength polymers and metals enhance durability and performance of automotive parts.
- Rapid Prototyping: Manufacturers can quickly prototype new designs using strong materials, speeding up the process of testing and iteration.
- Cost Efficiency: 3D printing reduces waste and can lower production costs in the long run.
In summary, the automotive industry significantly benefits from applying strong materials, improving vehicle performance and sustainability while capitalizing on innovative design and manufacturing techniques.
Future Trends in 3D Printer Materials
The domain of 3D printing continues to evolve rapidly, with material science at the forefront of this transformation. Understanding future trends in 3D printer materials is crucial for researchers, educators, and professionals as they navigate the complexities of design and manufacturing. This section aims to explore upcoming advancements and methodologies that will redefine material selection and application in 3D printing.
Advancements in Material Science
Recent advancements in material science play a significant role in enhancing the strength and versatility of 3D printed components. Researchers are focusing on the development of new polymers and composite materials that offer improved mechanical properties. For example, materials like Polycarbonate and Nylon blend are being optimized for higher tensile strength and impact resistance. This can lead to broader applications in industries requiring robust materials,
In addition to thermoplastics, the exploration of high-performance metals and alloys has gained traction. Innovations in metal 3D printing, such as those involving titanium and stainless steel, exhibit remarkable enhancements in load-bearing capacities. These advancements are often achieved through novel printing techniques including selective laser melting (SLM) and electron beam melting (EBM).
- Biomaterials: There is an increasing push towards materials that are not only strong but also biocompatible. These materials are significant in medical fields, where they can be used for implants and prosthetics.
- Smart Materials: The development of smart materials that respond to environmental stimuli is also a trending area. These materials can change their properties based on temperature, pressure, or other variables, opening new avenues in adaptive design.
"As material science advances, the possibilities for 3D printing become limitless, pushing the boundaries of traditional manufacturing processes."
Sustainability Considerations
Sustainability is becoming a pressing concern in all industries, including 3D printing. As awareness about environmental impacts of material production grows, there is a shift towards selecting eco-friendly materials. This shift has important implications for material strength and performance.
Many companies are now focusing on bio-based filaments, such as those made from PLA (Polylactic Acid), derived from renewable resources like corn starch. This reduces reliance on fossil fuels and minimizes the carbon footprint associated with material production.
Moreover, recycling initiatives are gaining traction within the 3D printing community. Materials like PETG and certain ABS products are being developed to be more easily recyclable, thus promoting a circular economy.
Here are key areas of focus:
- Reduced Environmental Impact: Developing materials that require less energy for production.
- Energy Efficiency: Innovations aimed at reducing energy consumption during the printing process itself.
- Lifecycle Assessment: Examining the long-term sustainability of materials from production to disposal.
The future of 3D printing materials seems to lean heavily on the balance between enhancing material properties and maintaining environmental responsibility. Addressing these concerns will not only improve sustainability outcomes but will also align the industry with broader societal goals.
Ending
Understanding the intricacies of material strength in 3D printing is of paramount importance for both practitioners and researchers in the field. This section consolidates the key findings of the article and lays the groundwork for future inquiry. In examining the various materials used in additive manufacturing, along with their mechanical properties, we can discern fundamental trends that affect not only product quality but also the sustainability of the manufacturing processes. Considering the significant implications of material selection on performance outcomes, the insights garnered herein also serve as a guide for industries reliant on robust and versatile components.
Summarizing Key Insights
Throughout this exploration, several pivotal insights surface:
- Different 3D printing materials showcase distinct mechanical properties. For instance, thermoplastics like PLA and ABS offer varying tensile strengths and flexural properties that determine their suitability for specific applications.
- Post-processing techniques are critical in enhancing the strength and durability of printed objects. Methods such as annealing and coating can significantly augment performance metrics.
- Testing methods are essential for evaluating material strength. They provide quantifiable results that ensure the printed objects meet industry standards for safety and effectiveness.
These insights affirm the necessity of careful material selection based on intended application, as well as the value of rigorous testing protocols to ensure reliability and performance.
Implications for Future Research
The future of 3D printer materials is bright yet complex. One of the most pressing areas for further investigation is the development of new materials that can offer enhanced properties. As technology advances, the potential for biocompatible materials and sustainable composites grows, which could reshape how we view manufacturing and its impact on the environment. Moreover, detailed studies into the relationship between printing parameters and material strength may yield optimized processes that minimize waste and increase efficiency.
Additionally, interdisciplinary approaches combining material science, engineering, and environmental studies could lead to innovative solutions that address current limitations faced in additive manufacturing. Overall, ongoing research is essential to unlock the full potential of 3D printing technologies in various applications across industries.